Fluid transfer in industrial settings plays a pivotal role in various processes. The need to transfer fluids efficiently, safely, and without leaks is critical to ensure smooth operations. This article delves into the common problems that arise during fluid transfer and provides ten practical ways to ensure leak-free operation in industrial pumps.
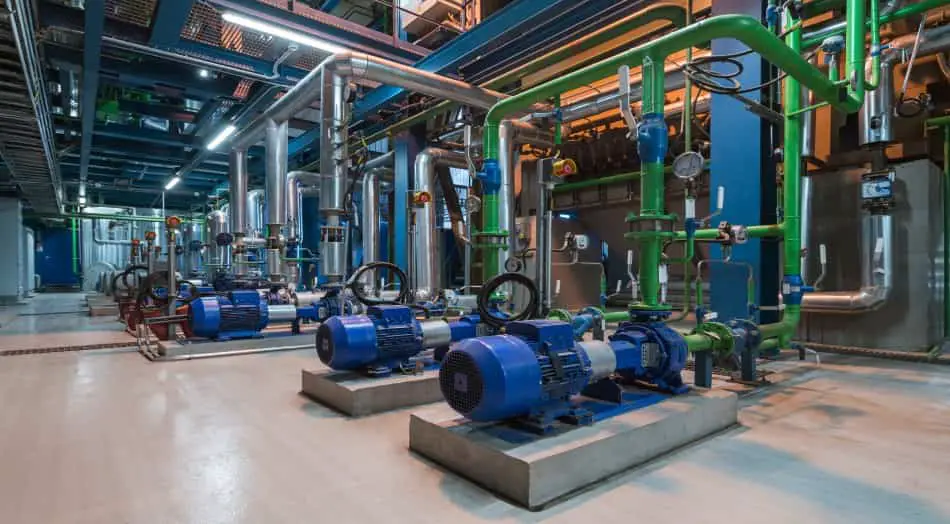
Problems In Transferring Fluids in Industrial Pumps
Fluid transfer in industrial pumps is not without its challenges. One of the most common issues encountered is mechanical seal failure. Mechanical seals are typically used to prevent leaks between rotating and stationary components, but they are subject to wear and tear. This is due to high temperatures, abrasive particles, and chemical reactions. As these seals degrade over time, they can lead to significant fluid leakage, causing operational inefficiencies, contamination risks, and safety hazards. In some cases, the maintenance and replacement of mechanical seals can be time-consuming and expensive, further adding to operational costs.
Another common issue is corrosion and erosion in the pump’s components. Industrial pumps often handle highly corrosive or abrasive fluids, which can damage internal parts over time. This deterioration weakens the pump’s integrity, leading to leaks and system failures. Furthermore, improper pump installation, lack of regular maintenance, and misaligned components can exacerbate these problems, reducing the pump’s lifespan and causing unexpected leaks.
10 Ways To Achieve Leak-Free Fluid Transfer in Pumps?
Addressing these problems requires a combination of proper design, material selection, and preventive maintenance strategies. Here are ten strategies to consider:
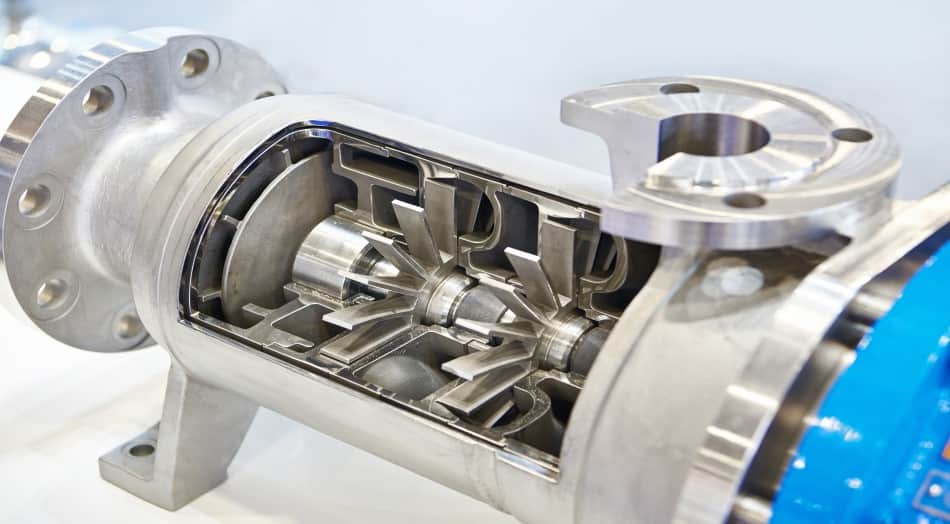
1. Use Magnetic Coupling Technology
Magnetic coupling eliminates the need for mechanical seals, thereby preventing the risk of seal failure and leakage. To optimize torque transfer efficiency, it’s important to ensure proper alignment during installation. Regular checks for any signs of wear or misalignment in the coupling magnets are also crucial to maintaining optimal performance. Magnetic couplings are particularly effective in systems handling hazardous or corrosive fluids, as they help reduce contamination risks.
When choosing a magnetic coupling, consider key factors for optimal performance. Start with the required torque capacity, which determines the size and strength of the magnets. For handling corrosive or abrasive fluids, select couplings made from durable, chemical-resistant materials. Moreover, consider the operating temperature, as extreme conditions can weaken the magnets.
2. Select the Right Pump Materials
The choice of materials plays a critical role in preventing leaks, especially when handling corrosive or abrasive fluids. Selecting materials based on the specific fluid’s chemical properties is essential, with stainless steel and corrosion-resistant alloys being ideal for aggressive fluids.
In some cases, advanced fabrication methods like plasma cutting are used to precisely shape and form durable pump components, ensuring that they can withstand harsh conditions. Additionally, using composite or coated materials can enhance resistance to chemical and mechanical wear.
Implementing a regular inspection schedule helps identify signs of material fatigue or degradation early, further reducing the likelihood of leaks. Consult with a certified pump technician or mechanical engineer. They can provide guidance on the appropriate inspection intervals based on the fluid type, pump operation conditions, and material composition.
3. Implement Regular Maintenance Programs
Implementing regular maintenance programs is essential for preventing leaks by keeping critical pump components in optimal condition. Developing a preventive maintenance schedule that includes routine inspections of seals, bearings, and lubrication systems is crucial. It’s also important to train operators and technicians to recognize early warning signs such as unusual vibrations, misalignment, or leakage around seals.
Predictive maintenance tools like vibration and temperature sensors work by continuously monitoring the equipment for anomalies. These sensors detect changes in the pump’s normal operating conditions, such as increased vibration or unusual temperature spikes, which may indicate wear or misalignment. When these changes are detected, the system can trigger an alert, allowing maintenance teams to address the issue before a leak or failure occurs.
4. Optimize Pump Installation and Alignment
Proper installation and alignment are crucial to prevent unnecessary stress on pump components, which can lead to leaks. It’s important to carefully follow the manufacturer’s installation guidelines to ensure correct pump alignment. For added precision during installation, using laser alignment tools is recommended, and alignment should be periodically checked as part of routine maintenance.
Laser alignment tools work by projecting a laser beam from one pump component to a target on the other, allowing for precise measurement of misalignment between the two. The tool detects any angular or parallel misalignment, providing real-time feedback to adjust the components until they are perfectly aligned. This ensures optimal alignment, reducing wear and stress on the pump, which helps prevent leaks and prolongs equipment life.
Monitoring for excessive vibration with sensors can also help identify misalignment or balance issues that need correction before they cause leaks. Sensors are placed on critical pump components to measure oscillations during operation. These sensors collect real-time data that can detect irregularities, such as imbalances or misalignments, which could lead to leaks if not corrected.
5. Utilize Double-Seal or Gas-Seal Configurations
Double-seal or gas-seal configurations provide extra protection in critical applications where leakage could have catastrophic consequences. For double-seal setups, it’s essential to maintain the barrier fluid at the correct pressure and ensure it is compatible with both the internal process fluid and the external environment. In gas-seal configurations, the gas supply, often nitrogen, must be clean and maintained at the appropriate pressure to create a reliable barrier. Regularly checking the integrity of both seal systems is important, and seals should be replaced if they show any signs of wear.
6. Ensure Proper Operating Conditions
Ensuring pumps operate within their specified design limits is essential for preventing excessive wear and leaks. Continuously monitoring parameters like temperature, pressure, and flow rate is important to keep them within recommended levels. Installing automatic control systems can help make real-time adjustments if conditions exceed design limits, thereby preventing seal damage or overheating. It’s also critical to train operators to understand the consequences of running pumps outside their specifications and how to make necessary adjustments to maintain optimal performance.
7. Reduce Cavitation and Vibration
Cavitation and vibration can cause seal damage and lead to leakage, so reducing these forces is crucial to maintaining pump integrity. Installing suction stabilizers or dampeners helps minimize pressure drops that can result in cavitation. Ensuring proper fluid levels and maintaining optimal flow rates are also essential to prevent the formation of vapor bubbles.
Using vibration isolators or dampers to reduce the impact of vibrations caused by misalignment or imbalance is highly recommended. This can significantly extend the life of the pump and prevent leaks. When choosing vibration isolators or dampers, consider factors such as the pump’s operating conditions, weight, and the frequency of vibrations it generates. It’s crucial to select isolators or dampers that match the pump’s vibration frequency range and load-bearing capacity to ensure effective absorption and long-term protection against leaks.
8. Install Pressure Relief Valves
Pressure relief valves protect pumps from overpressurization, a common cause of leaks. Position these valves at critical points in the system where pressure spikes are most likely to occur. Regularly testing the relief valves is important to ensure they function correctly and that their settings align with the system’s pressure rating.
When a pressure relief valve is triggered, the immediate corrective action is to reduce the system’s pressure to a safe operating level. This can be achieved by adjusting control valves, reducing pump speed, or shutting down the system to prevent further pressure buildup. Once the pressure is stabilized, the valve should be inspected to ensure it has reseated correctly and is not damaged.
9. Use Proper Gaskets and O-Rings
Gaskets and O-rings are essential for sealing joints and preventing leaks at connection points in industrial pumps. Selecting gaskets and O-rings that are compatible with the fluid being transferred and suitable for the operating conditions, such as temperature and pressure, is crucial.
Proper sizing and fit during installation are also important. Following the manufacturer’s torque guidelines ensures that connections are neither over-compressed nor under-sealed. Over-tightening can damage the valve, while under-tightening can lead to improper sealing. Regularly checking and adjusting the torque during routine maintenance helps maintain the valve’s integrity and effectiveness.
10. Upgrade to Leak Detection Systems
Upgrading to leak detection systems provides early warnings, enabling immediate corrective action before leaks escalate. When selecting a detection system, choose one that monitors key variables like pressure, temperature, or flow rate to catch anomalies early. Opt for systems with automated shutdown capabilities in the event of significant leaks to minimize potential damage and downtime.
Furthermore, integrating leak detection technology with a broader monitoring system provides real-time alerts and data analysis. These systems can continuously track the condition of pumps, pipes, and other components. When paired with data analytics, the system can predict potential issues and improve operational efficiency. It ensures that fluid transfer remains smooth, minimizing the risk of leaks, equipment failure, and costly repairs. It ultimately supports long-term reliability and sustainability in industrial operations.
End Note
Achieving leak-free fluid transfer in industrial pumps is crucial for maintaining operational efficiency, ensuring the safety of workers, and reducing environmental hazards. To avoid costly downtimes and prevent leaks, consult with a professional who can help you implement the best solutions for your specific industrial needs.