Let us explore the difference between Soldering vs Brazing! Soldering and brazing are distinct joining processes utilized in various industries and applications, each offering unique advantages and characteristics. The dissimilarities between soldering and brazing arise from their specific methods and the materials involved.
Just as hot and cold rolled steel diverge due to their processing techniques, soldering and brazing differ in their approaches to achieving secure and durable connections between metals. To make an informed choice between soldering and brazing, it is crucial to comprehend the disparities that set them apart.
Soldering vs. Brazing: Difference between Soldering and Brazing Overview
Soldering and brazing are two distinct methods of joining metals, each with its own set of characteristics and applications. These processes offer tailored solutions for creating strong and durable connections in various industries, depending on the materials being joined and the specific requirements of the application.

Soldering:
- Soldering involves melting a filler material (solder) with a lower melting point than the base metals, which then flows into the joint by capillary action.
- The melting point of solder used in soldering is generally below 840°F (450°C), making it suitable for joining materials without melting the base metals.
- Soldering is performed at relatively low temperatures, which reduces the risk of damaging delicate or heat-sensitive components.
- It is commonly used in electronics, jewelry making, plumbing, and other applications where precision and low heat are crucial.
- Soldered joints are generally weaker than brazed joints due to the lower melting point of the filler material.
- Soldering does not require the base metals to be heated to their melting point, which helps preserve the structural integrity of the joined materials.
- Soldered connections are more flexible and allow for slight movement between the joined parts.
- Soldered joints are more susceptible to the effects of temperature variations and mechanical stress.
- The joint appearance after soldering is often neat and clean, with minimal visible distortion.
Brazing:
- Brazing involves melting a filler metal (brazing alloy) with a higher melting point than that of solder, typically above 840°F (450°C).
- The base metals being joined in brazing do not melt; instead, the filler metal bonds them together.
- Brazing is carried out at higher temperatures than soldering, making it suitable for applications that demand stronger and more heat-resistant connections.
- It is used in industries such as aerospace, automotive, construction, and metalworking, where joint strength and durability are paramount.
- Brazed joints are generally stronger than soldered joints due to the higher melting point of the filler material.
- The high temperatures involved in brazing can potentially alter the properties of the base metals, but this can be managed with proper technique.
- Brazing allows for the joining of dissimilar metals and materials with varying melting points, expanding its range of applications.
- The resulting brazed joints are robust and capable of withstanding mechanical stress, vibration, and high temperatures.
- Brazing offers excellent hermetic seals, making it suitable for applications requiring air or fluid-tight joints.
- The appearance of brazed joints can vary, and they may exhibit slight distortion due to the higher temperatures involved.
While both soldering and brazing are effective methods for joining metals, they offer different levels of strength, heat resistance, and versatility. Soldering is ideal for delicate work and applications where lower temperatures are essential, offering flexibility and a clean appearance.
On the other hand, brazing provides a robust and durable connection for more demanding scenarios, making it suitable for industries requiring high strength and hermetic seals. Choosing between soldering and brazing depends on the specific needs of the project and the desired properties of the jointed materials.
Why to Learn About Soldering and Brazing Differences?
Understanding the differences between soldering and brazing has broad implications across industries. This knowledge empowers professionals to make informed material selections, optimizing performance for specific project needs. Leveraging the strengths of soldering and brazing ensures high-quality outcomes through cost-effective production, improved functionality, and enhanced aesthetics.
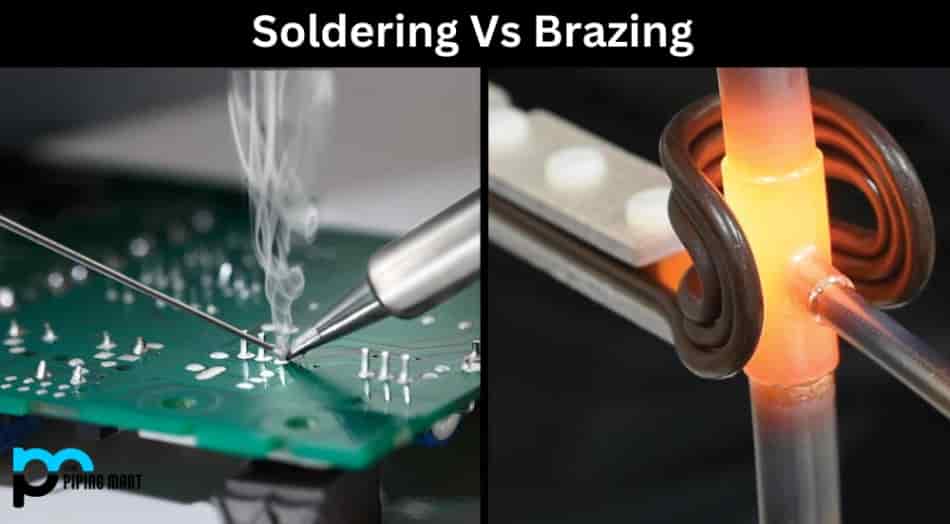
Furthermore, proficiency in these techniques extends beyond individual projects. It facilitates effective collaboration within multidisciplinary teams and equips individuals to make sustainable choices, considering factors such as material compatibility and environmental impact. In a rapidly changing landscape, this expertise enables professionals to adapt to emerging trends, fostering innovation and maintaining a competitive edge. It empowers engineers, students, and enthusiasts to navigate challenges and anticipate future obstacles.
Learning the distinctions between soldering and brazing is pivotal for professional growth, enabling informed decisions, effective collaboration, and adaptability in dynamic industries.
Soldering vs. Brazing: Working Principle
Understanding the working principles of soldering and brazing is fundamental to comprehending the nuances of these metal joining processes. Soldering and brazing, while both aimed at creating strong connections between metals, rely on distinct mechanisms that leverage the properties of filler materials with varying melting points. These principles dictate the temperatures, techniques, and outcomes of each process, playing a pivotal role in determining their respective applications and advantages
Soldering: Working Principle
The principle behind soldering lies in melting a filler material called solder, which has a lower melting point than the base metals being joined. The process can be outlined as follows:

- The surfaces of the metals to be joined are meticulously cleaned and prepared. This step ensures the removal of any contaminants, oxides, or residues that could hinder the proper adhesion of the solder.
- The soldering process requires the use of a soldering iron, a torch, or other heat sources. The solder is heated until it reaches its specific melting point, which is typically below 840°F (450°C).
- Once the solder reaches its melting point, it transforms into a liquid state. Through capillary action, the liquid solder is drawn into the joint due to the molecular attraction between the solder and the clean metal surfaces.
- As the solder flows into the joint, it forms a metallurgical bond with the base metals. This bond occurs through intermolecular forces and solidifies as it cools down, securing the connection.
- After the soldering process is complete, the joint is allowed to cool and solidify. During this phase, the solder hardens and creates a strong, permanent connection between the metals.
The working principle of soldering hinges on using a low-melting-point filler material to create a secure bond between the base metals without melting them. This process is commonly employed in electronics, jewelry making, plumbing, and other applications where precision and lower heat levels are crucial.
Brazing: Working Principle
Brazing, on the other hand, relies on a filler material with a higher melting point than solder. Following is a brief description of how it works:
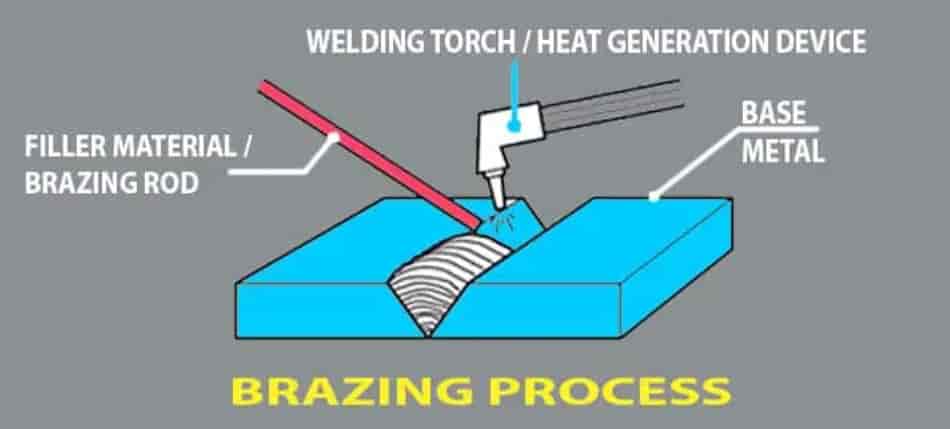
- Just like in soldering, the base metals being joined undergo thorough cleaning and preparation to ensure successful bonding.
- A filler material, known as a brazing alloy, is placed strategically between the metals in the joint. This alloy, chosen for its higher melting point, is often in the form of a paste, wire, or pre-formed shape.
- The assembly is then heated to a temperature higher than the melting point of the brazing alloy but below the melting point of the base metals. This is typically achieved using a torch or a controlled furnace.
- As the brazing alloy reaches its melting point, it flows through capillary action into the joint. The high heat allows the alloy to bond metallurgically with the base metals.
- After bonding, the assembly is gradually cooled down. The brazing alloy solidifies, resulting in a strong, durable connection that possesses properties distinct from the base metals.
A high-melting-point filler material is used in brazing to create a robust and durable bond between the base metals. Application of this process requires high strength, temperature resistance, and mechanical stress resistance, as well as compatibility with a variety of materials.
Choosing the right method for a specific application requires an understanding of these working principles. Various factors influence whether soldering or brazing is the right process for a particular joint, such as its strength and heat sensitivity, as well as its material compatibility.
Soldering vs. Brazing: Which is more efficient?
In order to comprehensively assess the efficiency of Soldering versus Brazing, a detailed comparison of their characteristics, applications, and performance is essential. By analyzing their distinct strengths and limitations, a clearer understanding emerges regarding the suitability of each metal joining technique in various scenarios. Presented below is an exhaustive breakdown of the efficiency aspects associated with Soldering and Brazing:
Efficiency Aspect | Soldering | Brazing |
Process Complexity | Soldering entails a relatively simple process, often involving lower heat requirements. | Brazing is comparatively more complex, demanding precise control of temperature and pre-heating. |
Joint Strength | Soldered joints tend to be relatively weaker compared to brazed joints. | Brazing yields stronger joints due to the higher melting point of the filler material. |
Heat Sensitivity | Soldering is well-suited for heat-sensitive materials and delicate components. | Brazing accommodates materials with higher heat tolerance and is preferable for applications where heat dissipation is crucial. |
Temperature Requirement | Soldering requires lower temperatures, usually below 840°F (450°C). | Brazing necessitates higher temperatures, often exceeding 840°F (450°C). |
Material Compatibility | Soldering’s low melting point limits compatibility, suitable mainly for joining similar materials. | Brazing’s higher temperatures facilitate compatibility with a broader range of metals and materials. |
Process Speed | Soldering typically offers a faster process due to its lower temperature requirements. | Brazing involves a slower process, including pre-heating and post-cooling stages. |
Precision | Soldering excels in precision, making it ideal for intricate projects like electronics and fine jewelry. | Brazing demands careful alignment for successful joints but may not offer the same level of precision as soldering. |
Appearance | Soldering results in a neat appearance with minimal distortion. | Brazing’s appearance can vary, with slight distortion due to higher temperatures. |
Mechanical Strength | Soldered joints are less mechanically robust compared to brazed joints. | Brazing produces joints with enhanced mechanical integrity, suitable for load-bearing applications. |
Heat Affected Zone | Soldering generates a minimal heat-affected zone, preserving material properties. | Brazing’s higher temperatures lead to a moderate heat-affected zone, potentially affecting material properties. |
Environmental Impact | Soldering consumes less energy due to lower temperatures, making it more environmentally efficient. | Brazing’s higher energy consumption contributes to a relatively greater environmental impact. |
Application Diversity | Soldering is versatile, suitable for intricate tasks, electronics, and various projects. | Brazing is more specific in application, often employed in industries requiring durability and robust connections. |
This detailed table meticulously dissects the efficiency aspects associated with Soldering and Brazing, encompassing factors like process complexity, joint strength, temperature requirements, precision, appearance, and environmental impact.
Soldering vs. Brazing: Efficiency Considerations
Joint Strength and Durability: Brazing’s propensity to yield stronger joints is notably advantageous, making it efficient for applications necessitating load-bearing capabilities and resilience against mechanical stress.
Heat Sensitivity and Material Compatibility: Soldering’s lower temperature requirements render it ideal for heat-sensitive materials, while brazing’s higher temperature range enhances its compatibility across a broader spectrum of metals and materials.
Process Complexity and Speed: Soldering’s simplified process and quicker execution align with projects demanding swift completion. In contrast, brazing’s intricate procedure, involving precise temperature control and supplementary stages, proves advantageous for intricate or load-bearing applications.
Application Precision and Appearance: Soldering’s lower temperatures make it conducive to precision work, lending itself to tasks where minimal distortion and fine alignment are essential. While brazing requires meticulous alignment, it may not achieve the same level of precision as soldering but can be more efficient for durable connections.
Environmental Considerations: Soldering’s energy-efficient nature, attributed to lower temperature requirements, contributes to a relatively lower environmental impact compared to brazing. However, brazing’s potential for producing stronger and longer-lasting joints could mitigate the need for rework, potentially leading to greater long-term efficiency.
Soldering vs. Brazing: Which is more Costly?
When it comes to choosing between soldering and brazing as metal joining methods, understanding their relative costs and benefits is paramount. While upfront costs may differ, the long-term advantages of one over the other can significantly impact your overall investment. Below is a comprehensive comparison of key factors to consider when deciding between soldering and brazing:
Type | Process Complexity | Initial Equipment Costs | Filler Material Costs | Joint Strength |
Soldering | Simpler process | Lower | Moderate | Weaker joints |
Brazing | More complex process | Higher | Higher | Stronger joints |
Comparing soldering and brazing involves exploring their costs and considerations thoroughly. Each technique has its own merits and drawbacks, demanding careful assessment for specific projects. Soldering is simpler and more affordable initially, but its weaker joints suit delicate tasks and electronics where strength is less critical. In contrast, brazing is complex and costly to start, but its stronger joints make it ideal for robust applications like load-bearing structures. While soldering boasts lower upfront expenses, it’s essential to weigh this against joint strength and durability. Your choice should align with your project’s needs, including joint strength, longevity, and application.
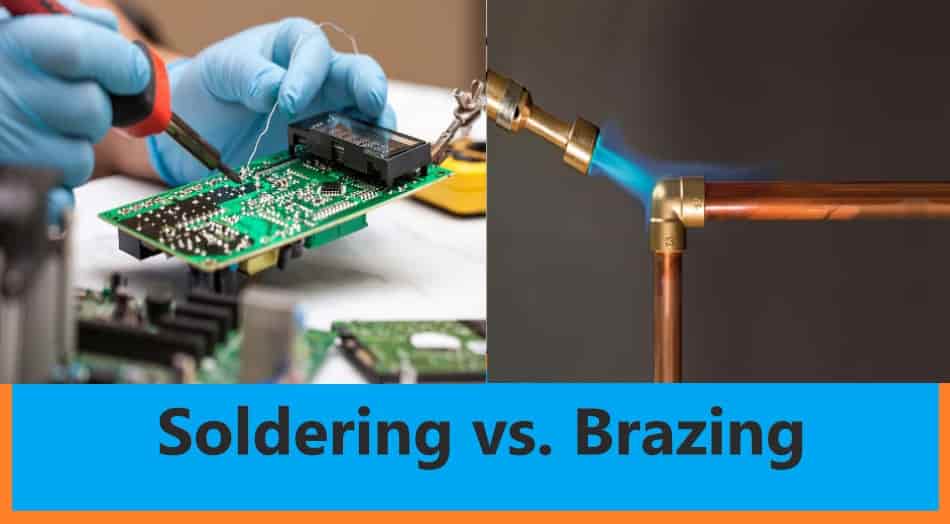
The decision between soldering and brazing surpasses mere initial costs. While soldering offers lower upfront expenses, brazing provides stronger joints and enhanced durability, potentially offering superior value in the long run. Deliberating the attributes of each technique and how they align with your project objectives is pivotal. This informed approach ensures a choice that optimizes both short-term investments and long-term outcomes, aligning with your project’s unique needs.
Differences between Soldering and Brazing
Let us see the tabulated difference between soldering vs brazing below:
Aspect | Soldering | Brazing |
Temperature | Lower temperatures, typically below 840°F (450°C) | Higher temperatures, often exceeding 840°F (450°C) |
Filler Material Melting Point | Low-melting-point solder (below base metal) | Higher-melting-point brazing alloy (above base metal) |
Joint Strength | Weaker joints due to lower-melting-point filler material | Stronger joints due to higher-melting-point filler material |
Application | Preferred for delicate work, electronics, and fine jewelry | Ideal for load-bearing structures, high-stress environments |
Heat Affected Zone | Minimal heat affected zone, preserving material properties | Moderate heat affected zone due to higher temperatures |
Surface Appearance | Neat appearance with minimal distortion | Variation in appearance due to higher temperatures |
Precision | Precise work possible due to lower temperatures | Careful alignment required, may not achieve same level of precision as soldering |
Process Complexity | Simpler process with lower heat requirements | More complex process demanding precise temperature control and additional stages |
Material Compatibility | Limited due to low melting point of filler material | Wider compatibility due to higher melting point of filler material |
Environmental Impact | Lower energy consumption due to lower temperatures | Higher energy consumption due to higher temperatures |
Cost | Lower initial cost due to simplicity and lower temperatures | Higher initial cost due to complexity and higher temperatures |
This table offers a comprehensive overview of the differences between soldering and brazing, covering aspects such as temperature, joint strength, application, heat affected zone, precision, process complexity, material compatibility, environmental impact, and cost.
Soldering vs. Brazing: Pros & Cons
Soldering Pros and Cons:
Pros | Cons |
Low-temperature process, suitable for delicate materials | Soldered joints tend to be weaker |
Precise and intricate work possible | Suitable for applications with lower mechanical stress |
Minimal heat-affected zone | Limited joint strength for load-bearing applications |
Less expensive equipment and materials | May require additional cleaning for effective bonding |
Well-suited for electronics and fine jewelry joints | Not ideal for high-temperature or heavy-duty applications |
Brazing Pros and Cons:
Pros | Cons |
High-strength joints, suitable for load-bearing structures | Higher-temperature process may affect heat-sensitive materials |
Stronger and more durable connections | More complex process with specific temperature control |
Effective in high-stress and elevated-temperature environments | Joint appearance may vary due to higher temperatures |
Wider material compatibility due to higher temperatures | Initial costs higher due to specialized equipment and materials |
Suitable for a broad range of applications | Joint alignment and preparation are crucial for successful brazing |
Which Method Should You Choose – Soldering vs. Brazing?
When deliberating between soldering and brazing, your decision hinges on aligning the requirements of your project with the desired attributes of the final joint.
If strength and load-bearing capacity are paramount, brazing is often favored due to its robust connections, well-suited for structural applications. For materials sensitive to high temperatures, soldering’s lower-temperature process prevents damage. Precision-demanding tasks benefit from soldering’s accurate joints with minimized distortion. On the other hand, brazing suits applications with elevated mechanical stress and temperatures, ensuring durability. Initial and long-term costs differ, soldering requires less specialized equipment, while brazing offers potential savings through stronger joints.
The choice should factor in material compatibility, production scale, and environmental impact. Supplier availability, industry standards, and complexity are crucial, and expert consultation aids well-informed decisions. Prototyping both methods and assessing specific needs help guide your selection.
Ultimately, the choice between soldering and brazing depends on your project’s requirements, the materials involved, and your long-term goals. Evaluating these considerations diligently will guide you towards selecting the most appropriate method that optimizes joint strength, durability, aesthetics, and overall efficiency.
FAQs
Is there a significant distinction between soldering and brazing?
Absolutely, soldering and brazing differ in their methods and materials. Soldering utilizes a lower-melting-point filler material that flows into joints, while brazing involves a higher-melting-point filler alloy that bonds metals without melting them.
Which method produces stronger joints, soldering or brazing?
Brazing typically results in stronger joints due to the higher melting point of the filler material. This strength makes brazing favorable for load-bearing structures and applications subjected to mechanical stress.
Where is soldering commonly applied?
Soldering is commonly used in delicate work such as electronics, jewelry, and plumbing, as well as applications where lower temperatures are essential to prevent damage to heat-sensitive components.
What advantages does brazing offer over soldering?
Brazing provides stronger and more durable connections, making it suitable for high-stress environments and load-bearing structures. It also allows for a wider range of material compatibility and excels in applications that demand elevated temperature resistance.
How should I decide between soldering and brazing for my project?
To make the right choice, consider your project’s specific needs. If precision, lower heat, and delicate work are essential, soldering is suitable. For applications requiring strength, durability, and resistance to high temperatures, brazing is the preferred option. Evaluate joint strength, appearance, material compatibility, and process complexity to align with your project goals.
Conclusion
The choice between soldering and brazing extends far beyond metal connections; it defines the success of diverse projects across industries. Soldering’s finesse and lower temperatures make it ideal for delicate applications, while brazing’s strength and durability suit heavy-duty scenarios.
Efficiency and cost considerations further guide the decision. Soldering’s lower upfront costs and energy efficiency contrast with brazing’s robust joints and durability. This choice reflects a careful evaluation of project goals, materials, and long-term benefits.
Mastering the nuances of soldering and brazing empowers professionals to create high-quality products while adapting to evolving challenges. This knowledge goes beyond technique, embodying informed decision-making, expert collaboration, and sustainable practices that drive progress.
As we conclude this exploration, we recognize that the choice between soldering and brazing mirrors the broader journey of using knowledge to shape a better future across industries.