Let us try to understand the roles of Antiscalants In Managing Industrial Scale And Corrosion! Industrial facilities often grapple with the challenges of scale and corrosion, two formidable foes that can significantly hamper operational efficiency and equipment longevity. Scale, the accumulation of mineral deposits like calcium and magnesium, can obstruct fluid flow, reduce heat transfer efficiency, and lead to increased energy consumption. Corrosion, conversely, is the gradual degradation of materials, typically metal, due to chemical reactions with their environment, which can lead to structural weaknesses and potential failures.
Understanding Industrial Scale And Corrosion
The importance of managing these issues cannot be overstated. Unchecked scale and corrosion can lead to costly repairs, decreased equipment life, safety hazards, and even unplanned shutdowns, impacting the financial bottom line and the environmental footprint of industrial operations.
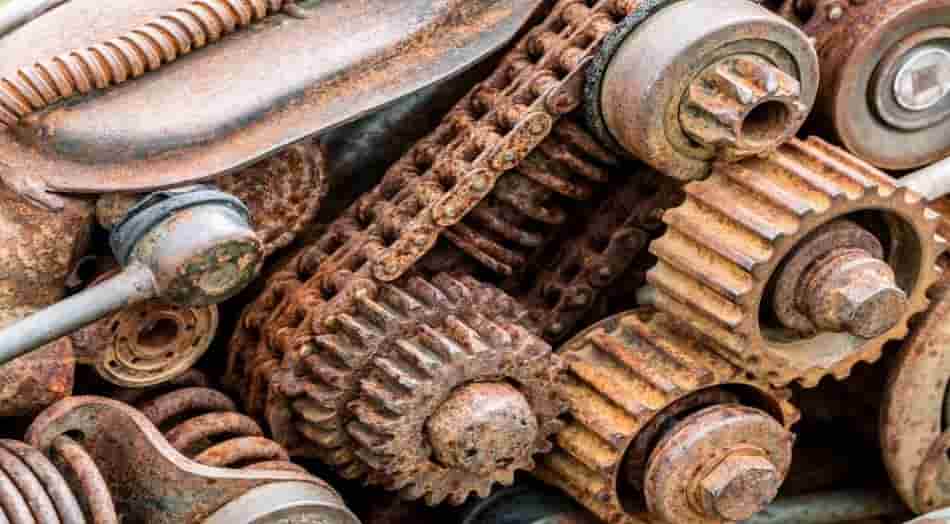
In this context, antiscalants emerge as a critical solution. These chemical agents are designed to prevent scale formation and mitigate the risks of corrosion, ensuring industrial systems’ smooth and sustainable operation. This article delves into the mechanisms of action of antiscalants, their application across various industries, and their role in prolonging equipment life and optimizing operational efficiency in the battle against industrial scale and corrosion.
Definition Of Industrial Scale And How It Forms
Industrial scale primarily refers to accumulating hardened mineral deposits on surface contact with water. This phenomenon typically occurs in water-intensive industrial systems like boilers, cooling towers, and pipelines. The formation process begins when water, especially hard water containing high levels of minerals like calcium and magnesium, is heated or evaporates, leaving behind these minerals. Over time, these deposits build up, creating an insulating layer that diminishes heat transfer efficiency, obstructs fluid flow, and increases the likelihood of equipment damage and energy loss.
Types Of Industrial Corrosion And Their Impacts
Corrosion in industrial settings manifests in various forms, each with distinct characteristics and consequences:
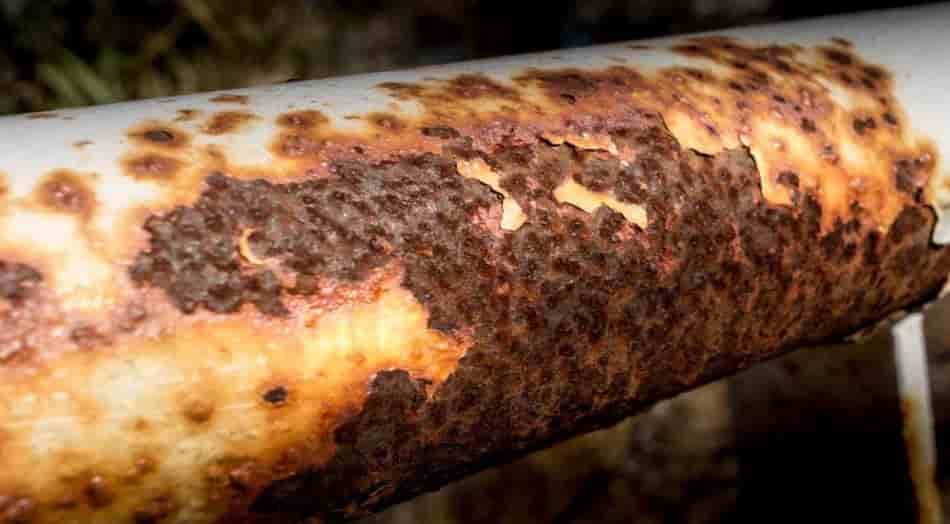
- Uniform Corrosion: This is the most common type, occurring evenly across the surface, leading to a uniform material loss.
- Pitting Corrosion: More dangerous and less predictable, pitting corrosion leads to small, localized areas of metal loss, potentially causing rapid failure in affected equipment.
- Galvanic Corrosion: Occurs when two different metals are in contact in a corrosive environment, leading to the deterioration of the more reactive metal.
- Crevice Corrosion: Similar to pitting, it occurs in confined spaces, where the lack of oxygen leads to a localized breakdown of the passive metal layer.
- Intergranular Corrosion: This happens along the grain boundaries of metal, weakening the structural integrity without affecting the overall appearance.
Each type impacts industrial operations differently. However, they commonly result in equipment failure, increased maintenance costs, safety hazards, and reduced operational efficiency.
Common Industries Affected By Scale And Corrosion
A wide range of industries faces the challenges of scale and corrosion. Key sectors include:

- Water Treatment Plants: Scale and corrosion can impair filtration systems and pipes, affecting water quality and system efficiency.
- Power Generation: Scale in boilers and cooling towers can significantly reduce efficiency. At the same time, corrosion can lead to failures in critical components.
- Oil and Gas: Pipelines, refineries, and processing equipment are particularly susceptible to corrosion, impacting safety and productivity.
- Manufacturing: Various manufacturing processes involve water and metals, making them vulnerable to scale and corrosion, impacting equipment life and product quality.
- Chemical Processing: Chemical plants often experience aggressive corrosive environments, requiring continuous monitoring and maintenance to prevent equipment degradation.
Understanding the intricacies of scale and corrosion is crucial for developing effective management strategies in these industries. The subsequent sections will explore how antiscalants are pivotal in mitigating these challenges. Let us see the overview of Antiscalants:
Definition And Basic Functioning Of Antiscalants
Antiscalants are specialized chemical agents employed to prevent scale formation in various industrial systems where water usage is essential. They function by interfering with the scaling process at a molecular level. When added to water, antiscalants disrupt the normal growth of mineral crystals such as calcium carbonate, a common scale component. They achieve this by binding to the developing scale crystals, distorting their shape and size, and ultimately preventing them from adhering to surfaces. This action helps maintain the efficiency of heat transfer surfaces, pipelines, and membranes, reducing the energy and maintenance costs associated with scale removal.
Types Of Antiscalants Commonly Used In The Industry
Different types of antiscalants are formulated to target specific types of scale and operating conditions. Some of the most commonly used types include:
- Phosphonates: Effective in controlling calcium carbonate and calcium sulfate scales, these are widely used in cooling and boiler water systems.
- Polyacrylates: These polymers function well in high-temperature environments, making them suitable for industrial boilers and heat exchangers.
- Polyphosphates: These are used for controlling iron and manganese scales, often in potable water systems.
- Organic Polymers: These versatile antiscalants are effective against various scales and are frequently used in membrane-based systems like reverse osmosis.
- Silicates: Employed primarily in cooling water systems, they are effective against silica scales.
How Antiscalants Differ From Other Scale And Corrosion Management Methods
Antiscalants offer a distinct approach to scale management compared to traditional methods. Unlike physical treatments like water softening, which removes hardness ions from water, or acid dosing, which dissolves scale after it forms, antiscalants prevent scale formation from the outset. This proactive approach can lead to significant cost savings, as it reduces the need for frequent equipment cleaning and maintenance.
Moreover, antiscalants differ from corrosion inhibitors, chemicals used to protect metal surfaces from corrosive reactions. While some products combine the properties of both antiscalants and corrosion inhibitors, they function through different mechanisms. Corrosion inhibitors typically form a protective film over the metal surface, whereas antiscalants disrupt scale formation at a molecular level.
The selection of antiscalants over other methods depends on various factors, including the industrial process type, the scaling problem’s nature, and the specific operational conditions. Their use represents a sophisticated and targeted approach to managing the universal challenge of industrial scale.
Mechanisms Of Antiscalants In Controlling Scale
The Chemical Process Of Antiscalants In Preventing Scale Formation
At the heart of an antiscalant’s effectiveness is its ability to modify the crystallization process of scale-forming minerals. The primary chemical process involves two key actions: threshold inhibition and crystal modification.
- Threshold Inhibition: Antiscalants are effective even in minute concentrations, often less than the stoichiometric amount of the scaling mineral. They work by adsorbing onto the active growth sites of the mineral crystals (such as calcium carbonate), thus inhibiting further crystal growth. This process effectively reduces the rate at which scale forms on surfaces.
- Crystal Modification: Antiscalants also alter the shape and size of the scale crystals, making them less likely to adhere to surfaces. The modified crystals become distorted and more soluble, which prevents them from forming hard, adherent scales. This crystal distortion also leads to a softer, non-adherent scale that can be easily removed, if formed at all.
Different Application Methods And Their Effectiveness
The application of antiscalants varies depending on the industrial system in use, and each method has its specific considerations for effectiveness:

- Dosing in Feed Water: Antiscalants are often dosed continuously into the feed water in systems like boilers or cooling towers. This ensures a consistent concentration of the chemical throughout the system, providing ongoing protection against scale formation.
- Batch Treatment: Antiscalants are added per batch in certain processes, especially when water is used in batch operations. This method requires careful monitoring to maintain effective concentrations and prevent overdosing.
- Membrane Systems: For reverse osmosis and other membrane systems, antiscalants are injected into the feed water to prevent scale formation on the membrane surface, which is crucial for maintaining the efficiency and longevity of the membranes.
- Automated Dosing Systems: Advanced industrial setups use automated dosing systems that continuously monitor water quality parameters and adjust antiscalant dosing accordingly. This method ensures optimal antiscalant performance, adapting to water chemistry or flow rate changes.
Each application method is designed to maximize the effectiveness of antiscalants, taking into account the specific dynamics of the industrial system in question. The choice of application method is critical and depends on the type of system, the nature of the water being treated, and the specific scaling risks present. let us learn about the Role Of Antiscalants In Preventing Corrosion:
How Antiscalants Protect Against Corrosion
While antiscalants are primarily designed to prevent scale formation, they also significantly mitigate corrosion. This protection is achieved through several mechanisms:
- Inhibiting Scale Formation: Antiscalants indirectly protect surfaces from under-deposit corrosion by preventing scale buildup. Scale deposits can create localized environments that accelerate corrosion, particularly under the scale where the metal surface is deprived of oxygen.
- Maintaining Flow Efficiency: By keeping the water flow smooth and uninterrupted, antiscalants help maintain a uniform distribution of oxygen and other chemicals, reducing the risk of localized corrosion.
- Stabilizing Water Chemistry: Some antiscalants also help stabilize the water’s pH and other chemical properties, creating less aggressive environments for the metal surfaces.
Synergy Between Scale Prevention And Corrosion Control
The effectiveness of antiscalants in scale prevention indirectly contributes to corrosion control. Scale and corrosion often go hand in hand; scale can harbor corrosive agents and create differential aeration cells that lead to localized corrosion. By preventing scale, antiscalants help maintain the integrity of the metal surfaces, reducing the sites where corrosion can initiate.
Moreover, certain formulations of antiscalants include components that specifically target corrosion. These compounds can form a protective film on metal surfaces, further preventing the metal from interacting with corrosive elements in the water.
Examples Of Corrosion Control In Industries Using Antiscalants
- Cooling Towers in Power Plants: In cooling towers, antiscalants prevent scaling on heat exchangers and reduce the corrosion rate of the cooling system’s metal components, thereby prolonging the system’s operational life.
- Oil and Gas: In the oil and gas industry, where water injection systems are used for enhanced oil recovery, antiscalants are added to the injection water to protect the pipelines and reservoirs from scaling and corrosion.
- Water Treatment Facilities: Many water treatment plants use antiscalants to prevent scaling in their pipes and filtration systems, which helps minimize corrosion-related damages and leaks.
These examples illustrate the dual role of antiscalants in industries where both scale and corrosion pose significant threats to the efficiency and integrity of the systems. The use of antiscalants in these settings demonstrates their vital role in extending equipment life and reducing maintenance costs.
Conclusion
The role of antiscalants in industrial settings is undeniably critical. They not only effectively combat scale formation but also contribute significantly to reducing corrosion, thus enhancing the efficiency and longevity of industrial equipment. The synergy between scale prevention and corrosion control underscores the multifunctional nature of antiscalants, making them indispensable in various sectors, from power generation to water treatment. The importance of continued research and development in this field cannot be overstated, as evolving industrial challenges necessitate more advanced and environmentally friendly solutions. For industry professionals, staying abreast of the latest advancements in antiscalant technology and adopting best practices in their application is crucial. By doing so, they can ensure optimal operational efficiency, prolong equipment life, and ultimately contribute to their industries’ sustainable and economical functioning.