In the world of welding, two popular methods stand out: socket weld and butt weld. These techniques are widely used in various industries to join metal components securely. Each method has its advantages and considerations, and understanding the differences between socket weld and butt weld can help you make informed decisions for your welding projects.
Difference Between Socket Weld vs Butt Weld
Socket weld refers to a welding technique that involves inserting the end of a pipe or fitting into a socket of another pipe or fitting. The joint is then welded around the outside to create a secure and leak-proof connection. Socket weld joints are commonly used for pipes and fittings ranging from half an inch to 4 inches in diameter.
Butt weld is another popular welding technique used to join two pieces of metal together along their edges. The process involves heating the ends of the metal pieces and then applying pressure to fuse them together. Butt welds are commonly used for pipes and fittings of various sizes, ranging from small diameters to large ones.
What is Socket Weld?
Socket weld joints offer several advantages. Firstly, they provide excellent structural integrity, making them suitable for high-pressure applications. Secondly, socket welds have a smooth interior, reducing the risk of turbulence and pressure drops in fluid flow. Lastly, socket weld connections are more resistant to corrosion compared to threaded connections.
However, socket weld joints also have some disadvantages. They can be time-consuming and require skilled labor for proper installation. Additionally, the welded area can create stress concentrations, which may affect the fatigue life of the joint.
Pros | Cons |
Excellent structural integrity: Socket weld joints provide strong and reliable connections, making them suitable for high-pressure applications. Smooth interior: The smooth interior of socket weld connections reduces turbulence and pressure drops in fluid flow. Corrosion resistance: Socket weld joints are more resistant to corrosion compared to threaded connections. Suitable for smaller pipes: Socket weld is commonly used for pipes and fittings ranging from half an inch to 4 inches in diameter. | Time-consuming installation: Socket weld joints can be more time-consuming to install compared to other welding methods. Skilled labor required: Proper installation of socket weld joints requires skilled labor with experience in socket welding techniques. Stress concentrations: The welded area in socket weld joints can create stress concentrations, which may affect the fatigue life of the joint. |
What is Butt Weld?
Butt weld joints offer several advantages. They provide excellent strength and durability, making them suitable for high-stress applications. Butt welds also have a smooth, continuous surface, which reduces the risk of leaks or weak points. Furthermore, the joint maintains the same thickness as the parent material, resulting in a uniform structure.
Despite their advantages, butt weld joints also have some considerations. The welding process requires precise alignment and skilled labor to ensure proper fusion. Additionally, the joint may introduce some deformation and residual stresses into the material, which can affect its mechanical properties.
Pros | Cons |
Excellent strength and durability: Butt weld joints provide exceptional strength and durability, making them suitable for high-stress applications. Smooth, continuous surface: Butt welds have a smooth, continuous surface, reducing the risk of leaks or weak points. Uniform structure: The joint maintains the same thickness as the parent material, resulting in a uniform structure. | Precise alignment required: Butt weld joints require precise alignment of the metal pieces to ensure proper fusion. Skilled labor required: Skilled welders with expertise in butt welding techniques are needed for accurate and reliable welds. Deformation and residual stresses: Butt welds may introduce some deformation and residual stresses into the material, which can affect its mechanical properties. |
Differences between Socket Weld and Butt Weld
Now that we understand the basics of socket weld and butt weld, let’s explore the key differences between the two methods:
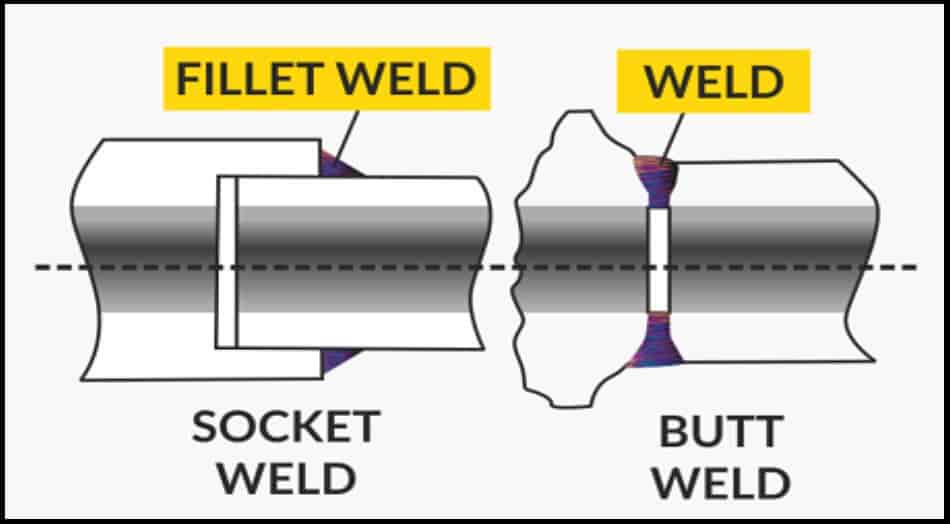
- Joint configuration: In socket weld, the pipe or fitting is inserted into a socket, while butt weld joins the edges of two pieces of metal.
- Welding process: Socket weld involves welding around the outside of the joint, while butt weld requires fusing the edges together.
- Strength and durability: Butt welds generally provide higher strength and durability due to the fusion of the entire joint area.
- Cost and complexity: Socket weld joints can be more time-consuming and require skilled labor, while butt weld joints may have higher initial costs due to equipment and setup requirements.
- Applications and suitability: Socket welds are commonly used for smaller pipes and low-pressure applications, while butt welds are preferred for larger pipes and high-pressure applications.
Choosing Between Socket Weld and Butt Weld
When deciding between socket weld and butt weld, it’s essential to consider the following factors:
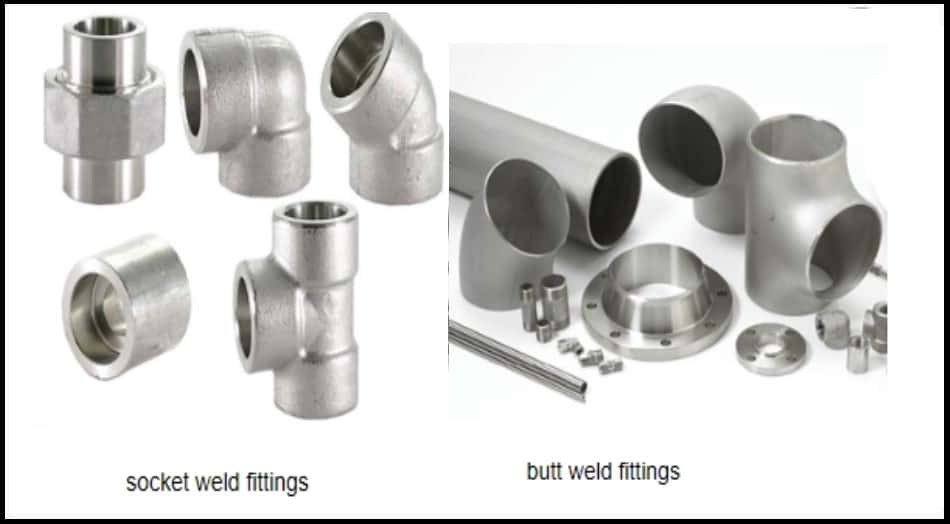
- Operating conditions: Evaluate the pressure, temperature, and fluid characteristics to determine the appropriate welding method.
- Pipe diameter and thickness: Socket weld is typically used for smaller diameters, while butt weld is more suitable for larger pipes.
- Joint strength requirements: If the joint needs to withstand high pressures or stresses, butt weld may be the preferred option.
- Installation time and complexity: Consider the available resources and expertise for the welding process.
- Industry standards and regulations: Ensure compliance with relevant codes and standards governing welding procedures.
By assessing these factors, you can make an informed decision based on the specific requirements of your project or application.
FAQs
Can socket weld and butt weld joints be interchangeable?
Socket weld and butt weld joints have different configurations and welding processes, making them generally non-interchangeable. The choice between the two depends on factors such as joint configuration, strength requirements, and operating conditions.
Which type of weld is stronger?
Butt weld joints are generally considered stronger due to the fusion of the entire joint area. However, both socket weld and butt weld can provide strong and reliable connections when applied correctly and suitable for the intended application.
Are socket weld joints more expensive to produce?
Socket weld joints may require more labor and time for installation, which can result in higher initial costs. However, the overall cost depends on factors such as the pipe diameter, project scale, and available resources.
What industries commonly use socket weld and butt weld?
Socket weld and butt weld are widely used in industries such as oil and gas, petrochemical, power generation, chemical processing, and HVAC (heating, ventilation, and air conditioning).
Can socket weld and butt weld joints be used for high-pressure applications?
Both socket weld and butt weld joints can be suitable for high-pressure applications. However, the choice depends on factors such as pipe diameter, operating conditions, and industry standards governing welding procedures.
Conclusion
Socket weld and butt weld are two popular welding methods used in various industries. Each technique has its advantages and considerations, and selecting the appropriate method depends on factors such as joint configuration, strength requirements, pipe diameter, and operating conditions. By understanding the differences between socket weld and butt weld, you can make informed decisions to ensure the integrity and reliability of your welded joints.