Heat exchangers are described along with the basic definition, parts, types, applications, advantages, disadvantages, etc. Let’s start heat exchangers! The heat exchanger, one of the most important equipment in all types of industries and without it, we cannot even imagine any systems nowadays.
Whether you are working in thermal plant or steel plant or nuclear plant, or HVAC system or piping or automotive industry, everywhere heat exchanger comes into play a crucial role as it helps to transfer or exchange energy which is the main concept for almost all types of system. Hence, it is essential to have knowledge on this item as well as its parts to learn the task of cooling or heating which enables heat transfer.
What are Heat Exchangers? Basics & Definition
We will start with the basics of heat exchangers!
Heat Exchanger Basics
If you are into a thermal system, you may have heard about heat exchangers. Basically, as the name exchange suggests the heat exchangers are the device that transfers heat between two or more fluids. So, the heat exchangers can be used in cooling as well as the heating processes. The heat exchangers can be seen in various applications, such as,
- space heating,
- refrigeration,
- air conditioning,
- power stations,
- chemical plants,
- petrochemical plants etc.
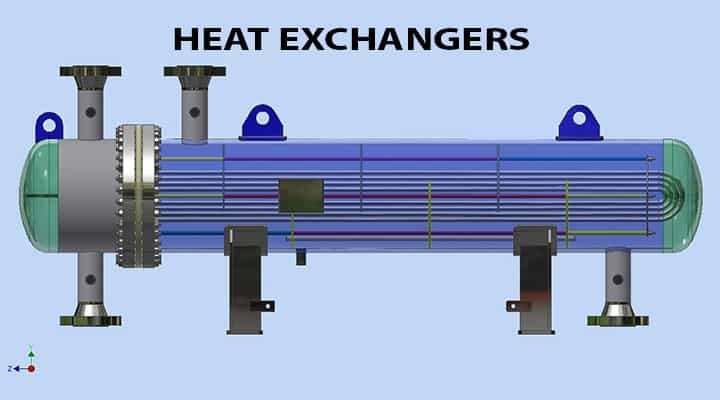
The most familiar example would be the heat sink. It is used to cool the electronic devices to a fluid medium or liquid coolant. The heat sink is a kind of passive heat exchanger. We will see the types and classification in detail because there’s a vast classification of heat exchangers.
- In heat exchangers, the fluids may be separated with a solid wall, or also they can be with direct contact.
- The surface of the heat exchanger plays a vital role as heat exchanges increase with the increase of the surface.
- The temperature difference is also another major factor.
Let’s get in. As I have already said the classification of the heat exchangers is vast, firstly, let’s check out the components of the heat exchangers.
What are the Parts or Components of Heat Exchangers? Description
The heat exchanger has the following parts or components,
- Shell
- Shell side pass partition plate
- Baffle plates
- Tubes
- Tube side partition plates
- Tie rods
- Spacers
- Tube sheets
- Sealing strip
- Expansion joints
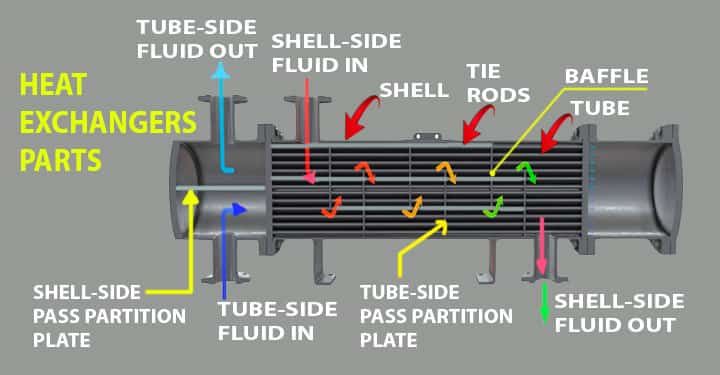
01. Heat Exchanger Parts: Shell
The shell is the one in which the heat exchanger keeps everything inside of it.
- The shell of the heat exchanger is based on the internal pressure.
- Shell is one of the costliest parts of the heat exchanger.
- As per the changing diameter the cost of shell and tube changes.
- Shell is closed by head on both sides either flanged or welded.
- The diameter depends upon the tube bundle diameter, the size of shell ranges from 6 inches (152mm) to 60 inches (1520mm).
02. Shell side pass partition plate
In most of the heat exchangers the single pass shell is used. The shell side pass partition plate is provided to avoid the cross of temperatures between the hot fluid and cold fluid that causes the unfavourable temperature difference.
There are many highly rated course available on the heat exchanger design, operation & maintenance
and can avail heat exchanger calculation
as well.
03. Baffle plates
The baffle plates are used to perform mainly the two functions,
- The baffles are used in the shell which directs the fluid stream across the tubes to increase the velocity of shell-side flow and thus improving the shell side heat transfer coefficient. So, basically, the baffle plates increase the turbulence in the shell-side fluid.
- Secondly, the baffle plates indirectly support the tubes and reduce the vibrations in the tubes. Different types of baffle plates are used. Like, segmental baffles they are really popular, orifice baffles, disc, and donut baffles.
The baffle spacing is determined carefully because the spacing directly affects the heat transfer coefficient and pressure drop. Usually, the standard baffle cut is 15% – 40%. Baffles can be of different categories, like –
- Cut-segment baffles,
- Disc & doughnut baffles,
- Orifice baffles
04. Heat Exchanger Parts: Tube
The tube used in the heat exchangers size ranges from 6.35mm to 63.5mm. The tubes carries either hot or cold fluid according to the process. Also, the number of tubes used depends upon the requirement.
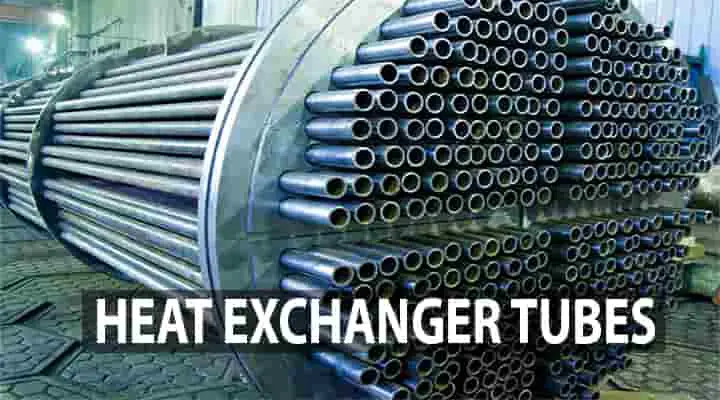
- A lot of different sizes are available in the markets.
- The thickness of the tubes used in heat exchanger expressed in the BWG (Birmingham Wire Gauge).
05. Tube side partition plate
The tube side passes gives the advantages of increasing the tube side fluid velocity hence improving the tube side heat transfer coefficient but at the expense of pressure drop.
- If the fluid which is used in the tube, doesn’t change it’s phase, it is preferable to use more number of tube side pass.
- The tube side passes are commonly used to improving the heat transfer coefficient.
- The passes can be achieved by various designs like one pass, two passes, etc.
06. Tie rods
The support needed for baffle plates is provided by the tie rods. The rods are generally made from solid metal bar. Generally, four or more tie rods are used to support the baffle plates.
07. Spacers
The spaces do the work of maintaining the space between the baffles. As we have already seen the space between baffles is an important parameter.
- The spacers are generally, pieces of extra available tubes.
- Spacers are passes over the tie rods which restricts the baffles to not to slide on the tie rods.
- This is how the spacers keep and fixes the location baffles to maintain the space between them.
08. Tube sheet
The tubes are the one end of tie rods is attached to the tube sheet also known as the tube plate. Due to the attachment the entire load of the tube bundle falls on the one or two tube sheets.
- Depending on the heat exchanger used the tube sheet numbers are decided.
- The one end of the tube sheet surface is exposed to the tube side of the fluid.
- Whereas the other surface is exposed to the shell-side fluid.
- The joins like expanded tube joint, welded tube joints are used in the tube sheets.
09. Sealing strip
The sealing strip is responsible for reducing the amount of bypass streams of shell side fluid flowing from the clearance between shell side inside diameter and tube bundle diameter.
10. Expansion joint
When the high temperature variation is given to the heat exchanger is expansion join become useful.
- The expansion joint will eliminate the expansion and contraction of the heat exchanger that will eliminate the cracking of the shell.
- If the expansion joint is not provided especially in the fixed tube heat exchanger, then the sheet will not permit the unequal expansion and contraction and hence the development of thermal results causes cracks in the sheet and resulting leakages.
Now we will see the heat exchangers classification with their brief descriptions.
Types of Heat Exchangers: Classifications
The classification of heat exchangers are based on the following:
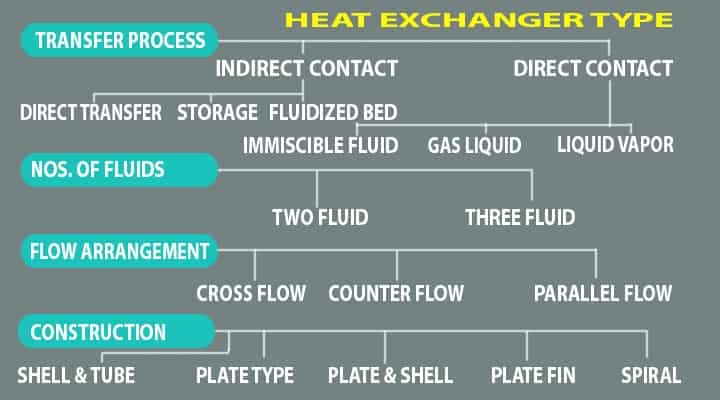
According to the transfer processes
a) Indirect-contact heat exchangers
- Direct transfer type
- Storage type
- Fluidized bed heat exchanger
b) Direct contact type heat exchangers
- Immiscible fluid exchangers
- Gas liquid exchangers
- Liquid vapor exchangers
According to the number of fluids
- Two fluid heat exchangers
- Three fluid heat exchangers
According to the flow arrangement
- Counter flow heat exchanger
- Cross flow heat exchanger
- Parallel flow heat exchanger
According to the construction
- Shell and tube heat exchangers
- Plate heat exchangers
- Plate and shell heat exchanger
- Plate fin heat exchanger
- Spiral heat exchangers
Let’s learn all types of heat exchangers.
Heat Exchanger based on Transfer Process
Indirect-contact heat exchangers
This classification is dependant upon the contact between the fluids. The flowing fluid is separated using the solid wall. So as the name suggests the indirect heat exchanger as the fluid will flow separately separated by the solid wall between the two fluids. The indirect contact ones are divided into three types.
Direct transfer type
There is no direct mixing of the fluids happening in this heat exchanger so don’t go by its name.
- The heat transfers in this heat exchanger continuously from hot fluid to cold fluid.
- The examples are direct types ones are tubular exchangers, extended surface exchangers.
Storage type
The storage type heat exchanger is also known as the regenerative heat exchanger. In this heat exchanger the fluid flow in an alternative way through the same flow passages and the heat transfer is intermittent.
- In storage type HE, the hot gas transfers over the heat transfer surface, whereas the thermal energy in form of hot gas is stored in the matrix wall.
- Thus, the hot gas will get cooled during the matrix heating period.
- Later the matrix will give up its thermal energy and is absorbed by the cold fluid.
Fluidized bed heat exchanger
In this heat exchanger, the one side of two fluid exchangers is immersed in a bed of finely divided solid materials. This type of heat exchanger is commonly seen in drying, mixing, coal combustions, and waste heat recovery systems.
Direct Contact Type Heat Exchangers
In the direct contact type, the two fluids come directly in contact with each other. They exchange heat and then separated. Let’s see some more types of direct contact type heat exchangers.
Immiscible fluid exchangers
The two immiscible fluids are brought into direct contact in this heat exchangers. The immiscible fluids are the one that won’t mix to give a single phase. The examples are water and oil.
Gas-liquid exchangers
In these exchangers one of the fluids is gas and other one is the liquid mostly low-pressure liquid.
- They are separated after the energy exchange.
- The gas-liquid exchangers 90% of energy transfer is done by evaporation of liquid.
- The applications include spray drier, spray tower, etc.
Liquid vapor exchangers
Steam is partially condensed using the cooling water in this heat exchanger. Also, sometimes the water is heated with the waste heat steam through direct contact in the exchanger. Examples are desuperheaters, open feedwater heaters.
Heat Exchangers based on Number of Fluids
Two fluid heat exchanger
The two fluid heat exchangers are the most commonly used. Because obviously there is need of two fluids for heat transfer for – ,
- heating,
- cooling,
- heat recovery and
- heat rejection.
Three fluid heat exchanger
The three fluid heat exchangers are mostly used in the cryogenics and some chemical processes. Like, air separation systems, helium-air separation units, etc.
Heat Exchanger based on Flow Arrangement
This classification depends upon the fluid flow inside the heat exchangers. It has three types as follows.
- Counterflow hear exchanger
- Crossflow heat exchanger
- Parallel flow heat exchanger
Counterflow heat exchanger
The counter flow heat exchangers fluids flow in the opposite directions. They are generally used for liquid-liquid and condensing and gas cooling applications.
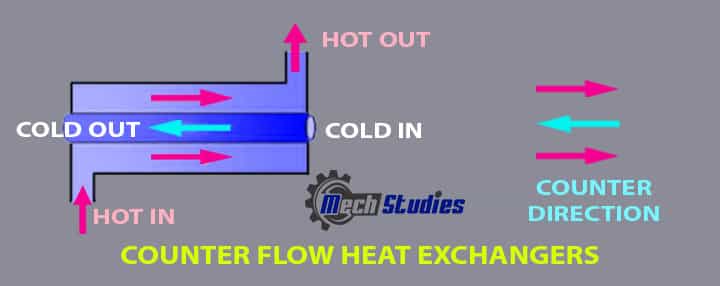
- The fluids flow parallel to each other but opposite in directions.
- The counterflow arrangement is considered superior to other arrangements.
- Because the counter flow arrangements produce the highest temperature change in each fluid compared to other fluid arrangements.
Crossflow heat exchanger
In this heat exchanger, the one of fluid is in spiral flow whereas the other one is in the cross flow. The fluids flow in the normal direction to each other. Though the effectiveness of this heat exchanger is lower than the counter flow heat exchanger.
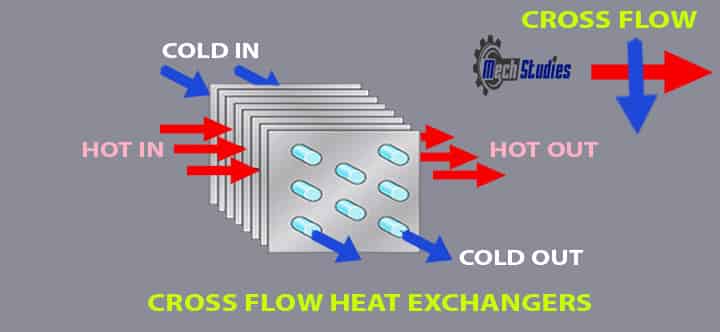
Parallel flow heat exchanger
These are also known as the co-current parallel stream. In this heat exchanger, the fluid stream enters at one end, then they flow parallel to each other in same direction and leave at another end. The parallel flow heat exchanger has the lowest exchanger effectiveness compared to other arrangements.
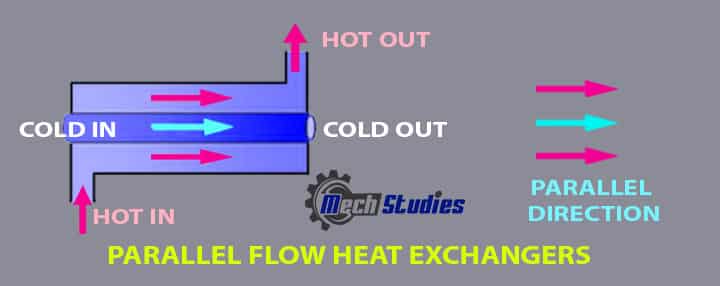
Heat Exchanger based on Construction
Heat exchangers shall be as follows:
Shell and tube heat exchanger
The shell and tube heat exchangers are popular and used in lots of applications. It has a tube box, shell, front and rear end headers, baffles, or fins. As we have seen earlier, the baffles increase the turbulence of fluid and increases the efficiency.
There are few variations of shell and tube heat exchangers are available according to its flow rate and need of support etc. It has series of tubes in which the fluid is present that needs either heating or cooling. One fluid runs inside the tubes other over the tubes.
The shell and tube heat exchangers are used in intercoolers, charging air for combustion engines. The fins are added to increase the heat transfer rates in these heat exchangers.
Plate heat exchanger
The plate heat exchangers consist of lots of thin plates. They are slightly separated and have large surface areas and small fluid flow for heat transfer.
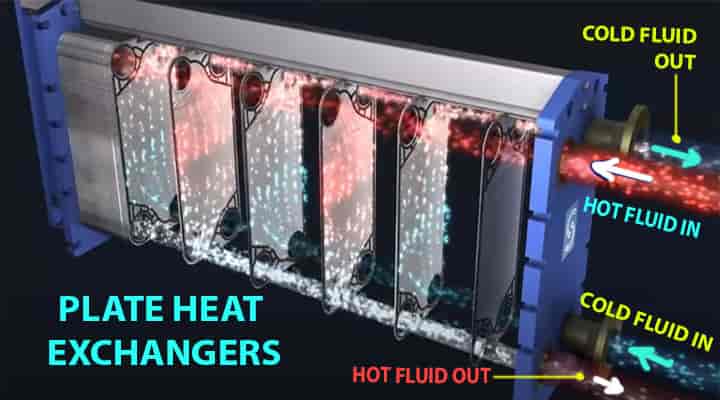
Plate heat exchangers are now more practical with the advancements in gaskets and brazing technologies.
Plate and shell heat exchanger
The plate and shell type heat exchanger combines the plate heat and shell tube heat exchanger. The plate and shell exchangers offer high heat transfers, high pressure high operating temperatures, compact sizes, etc.
Plate fin heat exchanger
It has sandwiched passages consisting fins that increases the effectiveness of the unit.
- The design of these heat exchangers includes crossflow, counterflow coupled with the fins.
- They are made of aluminium alloys that give them high heat transfer efficiency.
Spiral heat exchanger
In the spiral heat exchangers, the shell is replaced by the coiled tube. It allows the two fluids to flow parallelly to each other. The spiral heat exchangers have the advantage of highly efficient use of space which can be used to gain some improvements in the performances.
How Does Heat Exchanger Work?
Let’s take the working principle of the heat exchanger with shell & tube type. We will try to understand it step by step.
Basic Principle
The heat exchanger is worked based on the second law of thermodynamics. We have already learned that heat flows due to the temperature potential or temperature difference. It means always heat flows from a hotter body to a cooler body. Heat can flow by three process,
- Conduction
- Convection
- Radiation
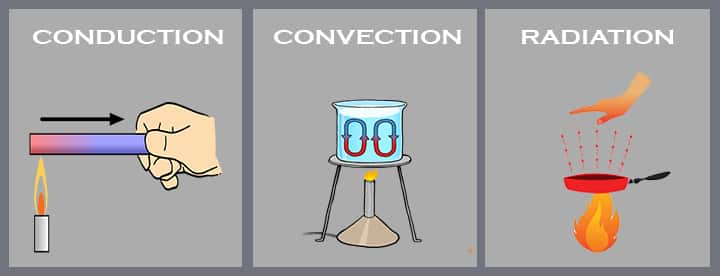
Within these three processes, the conduction and convection processes are widely used in heat exchangers.
Working Process
Take a shell and tube type, heat exchanger. It has two parts, shell and tubes. Many tubes are placed within the shell. Two different types of fluids are used,
- The fluid is to be cooled, it is called hot medium
- The fluid which will cool or cooling medium.
The cooling medium is passed through the tubes within the shell and the fluid which will be cooled is filled the shell around the tubes. In refrigerant shell and tube types chillers, the refrigerant is the medium to be cooled, basically, its a hot medium, and water is the cooling medium.
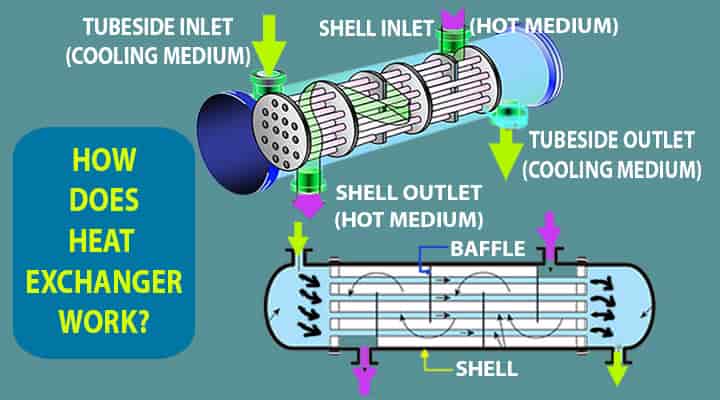
The process shall be as follows,
- The cooling medium, the water enters the shell through the cooling water INLET and exits through cooling water OUTLET.
- Refrigerant enters to the tubes through hot medium INLET and exits through hot medium OUTLET.
- Baffles are used in the shell with some intervals to avoid turbulence as well as increase efficiency.
- Hot medium and cooling medium has temperature difference.
- Due to this temperature difference, heat transfer happens from the hot medium to the cooling medium.
- Hot medium releases heat and becomes cool.
- Cooling medium takes up the heat and becomes hot.
The temperature of the hot medium can be controlled to meet the process requirements by the followings,
- Increase the flow of the cooling medium.
- Reduce the pressure of the cooling medium.
- Installing the bypass valve to control the hot medium etc.
Heat Exchanger Equation
To design a heat exchanger, the basic equation is considered as,
Q = U A ΔT,
Where,
- Q: Heat transfer rate between the two fluids in watt,
- U: Overall heat transfer coefficient in m2-K/w,
- A: Heat transfer surface area in m2,
- ΔT: Log mean temperature difference in oK,
Now, what is LMTD?
LMTD
Let’s try to understand LMTD. Consider A side implies hot medium entry and cooling medium out and B side implies hot medium outlet and cooling medium entry.
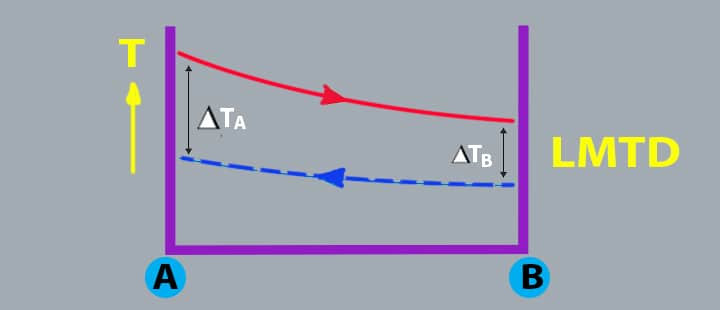
LMTD or logarithmic mean temperature difference is expressed as,

- ΔTA = Temperature difference of fluids at A
- ΔTB = Temperature difference of fluids at B
Materials for Heat Exchangers
The materials of heat exchangers are based on the applications and project requirements. Few materials are listed for the basic idea,
- Copper,
- Steel,
- Nickel,
- Titanium,
- HDSS,
- DSS,
- Brass,
- Hastelloy,
- Ceramics,
- Plastics, etc.
Heat Exchanger Selection Considerations
We have already got a basic idea about heat exchangers, now, how to select a heat exchanger? Let’s see the factors which need to be considered during heat exchanger design.
- Structural strength,
- Type of applications,
- Size and capacity requirements,
- The type of fluids,
- Properties of fluids,
- Temperature requirements,
- Pressure drop,
- Space constraints,
- Materials,
- Capital cost,
- Ease of maintenance etc.
Applications of heat exchanger
The applications of heat exchanges are as follows,
- The heat exchanger is widely used in the industries for cooling and heating or large-scale industries.
- In lots of industries, the waste heat is just wasted, but the heat exchanger can utilize the waste heat and use it to heat different stream in the process.
- They are used in waste water treatments, refrigeration industries, wine and beer making, petroleum refining, nuclear power etc.
- The heat exchanger is used to take heat from the engine’s oil system in aircrafts.
- Pharmaceutical industries and food, beverage industries.
Advantage of Heat Exchanger
There are so many advantages, as follows:
- It can increase or decrease fluids.
- High heat transfer efficiency.
- A variety of suitable materials can be used.
- A pressure test can be done very easily.
- It can be used in many industries.
- It reduces the cost of the system.
Disadvantages of Heat Exchanger
There are few disadvantages, as follows,
- Difficult to clean the tubes.
- If the heat exchanger incurs a leakage problem, it will be difficult to find out and repair.
- The initial cost is high.
- Pressure drop is a common problem.
Manufacturers of Heat Exchangers
There are a lot of manufacturers available across the globe, few of them are listed,
- Sondex Heat Exchangers
- Thermotech
- AIC
- Enerquip
- Industrial Heat Transfer, etc.
Conclusion
So, finally, we have learned the basics of heat exchanger along with the basic definition, parts, types, applications, advantages, disadvantages, etc. Do you want further study? Hey, check out most interesting articles,
Appreciate it for this marvelous post, I am glad I found this website on yahoo.
It’s nice that you talked about how heat exchangers are devices that transfer heat between two or more fluids. I was skimming through a book earlier and I learned a little bit about heat exchangers. From what I’ve heard before, it seems there are even establishments nowadays that offer solutions for heat exchangers.