Reciprocating and rotary compressors are two common types of mechanical devices used to increase the pressure of gases for various applications. Reciprocating compressors operate through a piston-driven motion, drawing in gas and compressing it within a cylinder.
They are ideal for high-pressure tasks and variable load demands. On the other hand, rotary compressors use rotating mechanisms, such as screws or vanes, to compress gas. They offer continuous and smooth operation with fewer vibrations, making them suitable for steady-state conditions. Each type has distinct advantages and limitations, making the choice between them crucial for efficient system design.
Reciprocating vs Rotary Compressor: Overview
Reciprocating and rotary compressors represent two fundamental approaches to gas compression, each with distinctive attributes that cater to specific industrial and commercial needs. Exploring their contrasting features facilitates the selection of the most suitable compressor for varied applications.
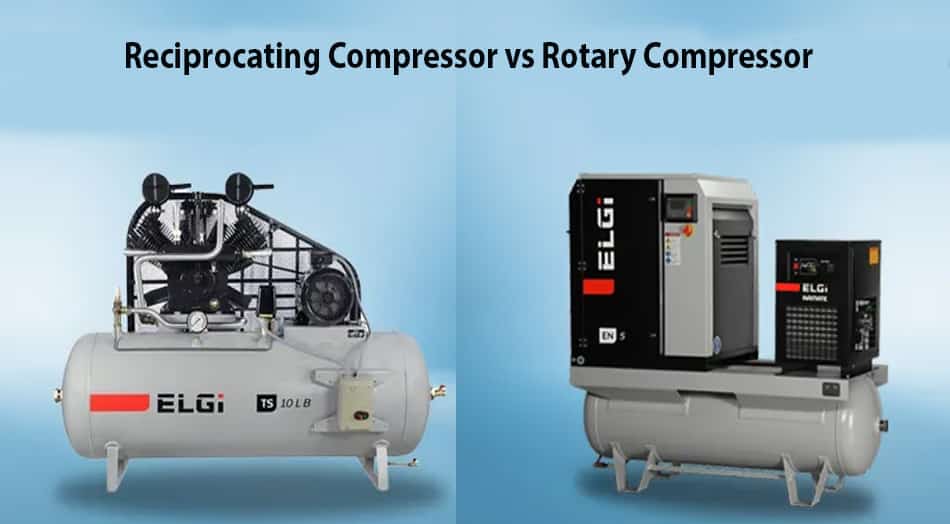
Reciprocating Compressor
- Driven by a piston-cylinder mechanism, converting linear motion into gas compression.
- Optimal for high-pressure tasks and applications with variable load demands.
- Demonstrates higher efficiency at lower compression ratios, making it versatile for various gases.
- Accommodates a broad spectrum of pressures and gases, enhancing adaptability.
- Maintenance complexity arises from numerous moving parts; ongoing innovations are streamlining upkeep.
- The operation generates elevated vibration and noise levels, necessitating noise mitigation measures.
- Emphasizes upfront cost considerations, making it a cost-effective choice for initial investments.
- Found in refrigeration, air conditioning, and as a power source for pneumatic tools.
Rotary Compressor
- Leverages rotating components (screws, vanes) to compress gases, delivering continuous and uniform operation.
- Flourishes in steady-state scenarios, ensuring consistent gas compression devoid of abrupt fluctuations.
- Compact and lightweight due to simplified construction, suitable for space-restricted installations.
- Minimal vibration and noise emissions, rendering them favorable for noise-intolerant environments.
- Attains peak efficiency at higher compression ratios, excelling in specific operating conditions.
- Ideal for applications with stable pressure requirements, encountering limitations with volatile pressure changes.
- Initial investment tends to be higher, but routine maintenance procedures are typically straightforward.
- Popular in settings prioritizing noise reduction, space optimization, and long-term efficiency, e.g., air compressors, and refrigeration units.
Why to Learn About Reciprocating vs rotary compressor Difference?
Learning about the distinctions between reciprocating and rotary compressors offers multifaceted benefits across diverse sectors. Engineering professionals, technicians, and industrial experts gain invaluable insights as they navigate the intricate landscape of compressor selection. Armed with this knowledge, they can make well-informed decisions that align compressors with specific application demands, whether it’s a high-pressure task or a scenario with variable load requirements. This deliberate choice contributes to enhanced operational efficiency and reduced energy consumption, aligning with sustainability goals.
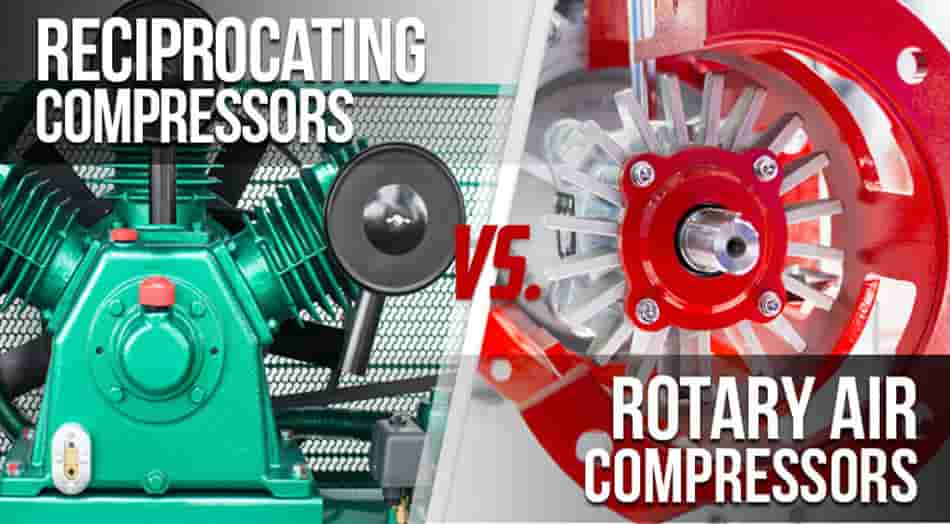
The significance of comprehending the differences between reciprocating and rotary compressors is far-reaching. It empowers stakeholders at every level, from individual professionals to entire industries, to make choices that amalgamate efficiency, sustainability, safety, and innovation. As technology advances and industries evolve, this knowledge remains a cornerstone of progress.
Reciprocating vs rotary compressor: Working Principle
While reciprocating compressors and rotary compressors have different operating mechanisms, both offer critical solutions for a wide variety of compression requirements, regardless of their differences. A deeper understanding of their functions and their respective applications can be gained by gaining insight into their working principles.
Reciprocating Compressor: Working Principle
Reciprocating compressors employ a piston-driven mechanism, creating a rhythmic dance between motion and compression. This mechanism involves a sequence of steps that orchestrate the gas compression process:
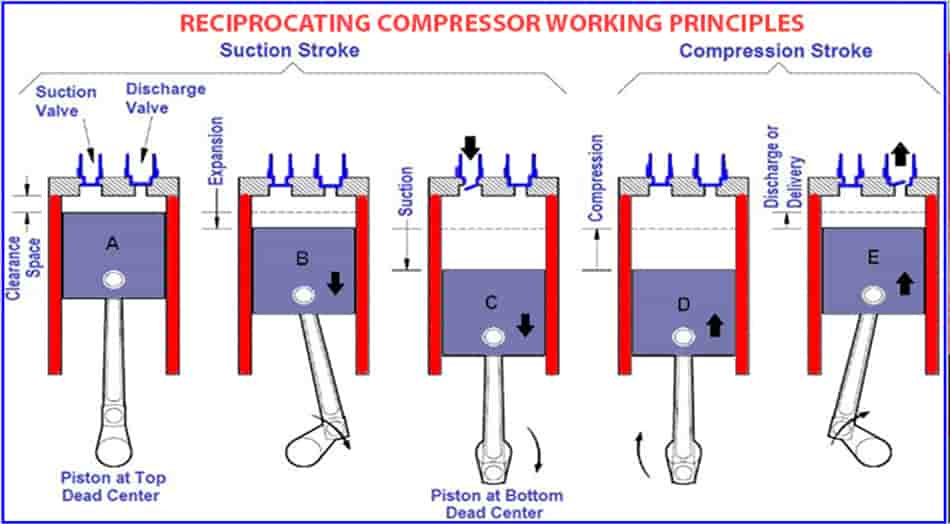
Reciprocating compressors employ a piston-driven mechanism for gas compression.
- The cycle begins with the intake stroke, where the piston descends, opening the intake valve for gas to enter due to the pressure difference.
- As the piston ascends during the compression stroke, the gas within the cylinder is compressed while the exhaust valve remains closed.
- During the discharge stroke, the compressed gas forces the discharge valve open, allowing the gas to exit the cylinder.
- The re-expansion stroke completes the cycle as the piston descends again, causing the intake valve to open, initiating the process anew.
- This repetitive piston motion facilitates gas intake, compression, and discharge, making reciprocating compressors well-suited for tasks with high pressure and varying load demands.
- The inherent start-stop motion can lead to more vibration and noise compared to rotary compressors
This cyclic ballet of motion and compression characterizes reciprocating compressors. It renders them adept at accommodating high-pressure scenarios and dynamic load demands. However, this rhythmic motion may also generate more vibration and noise.
Rotary Compressor: Working Principle
In the realm of rotary compressors, a different choreography unfolds one characterized by continuous rotation and smooth transitions. The working principle of rotary compressors involves the following sequence:
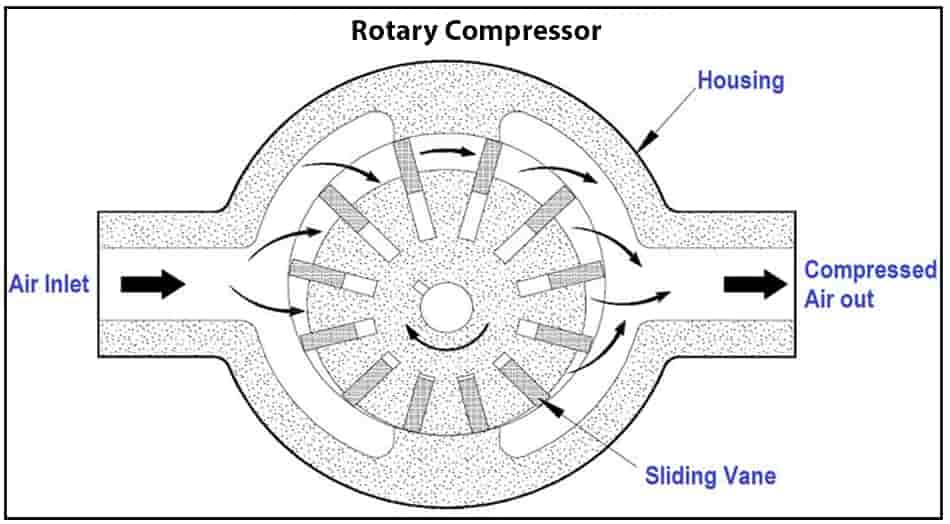
- Rotary compressors achieve gas compression through continuous rotary motion.
- Gas enters the compressor through the inlet port as the rotor’s rotation generates space for its entry.
- As the rotor turns, the gas becomes trapped between the rotor’s lobes and the compressor housing, leading to compression.
- The compressed gas is then discharged through the outlet port as the rotor’s rotation continues.
- The continuous rotary action results in a smoother compression process, making rotary compressors suitable for applications requiring stable and uninterrupted operations.
- Rotary compressors exhibit lower vibration and noise levels compared to reciprocating compressors, making them favorable for noise-sensitive environments.
- The compact and streamlined design of rotary compressors is well-suited for applications with space constraints.
This continuous and uninterrupted performance underlies rotary compressor efficiency, particularly in scenarios demanding steady, uninterrupted operation. Unlike reciprocating compressors, which produce in a staccato rhythm, rotary compressors produce in a more harmonic and less loud manner, making them a popular choice in settings where peace and quiet are important.
In sum, the working principles of reciprocating and rotary compressors each have their own choreography which is one that’s marked by rhythm and cycles, the other by continuous rotation. The selection between these two depends on the nuances of pressure demands, load dynamics, noise tolerance, and spatial availability.
Reciprocating vs rotary compressor: Which is more Efficient?
To holistically analyze the relative efficiency of Reciprocating Compressors and Rotary Compressors, it is essential to delve into an extensive exploration of their characteristics and applications. By conducting a thorough examination, we can uncover a comprehensive understanding of their respective strengths and suitability for diverse operational scenarios.
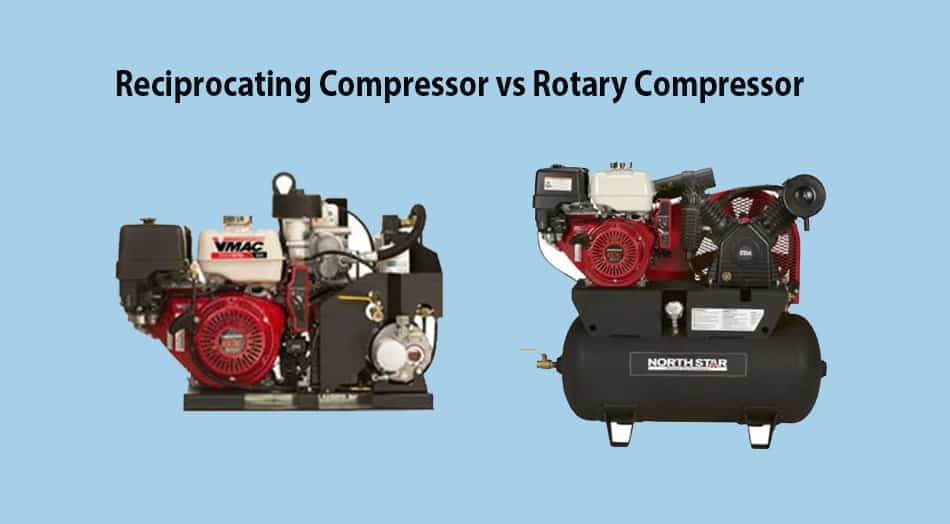
Presented below is an even more detailed table that delves into an expanded spectrum of efficiency aspects associated with both Reciprocating and Rotary Compressors:
Efficiency Aspect | Reciprocating Compressor | Rotary Compressor |
Compression Method | Piston-driven back-and-forth | Continuous rotary motion |
Efficiency | Higher efficiency at low loads | More consistent efficiency |
Capacity Control | Step or stepless capacity | Continuous capacity modulation |
Vibration & Noise | Can be noisier and vibratory | Generally quieter and smoother |
Maintenance | More maintenance due to parts | Reduced maintenance complexity |
Size and Portability | Bulkier and less portable | Compact and portable designs |
Initial Cost | Generally lower initial cost | Potentially higher upfront cost |
Energy Consumption | More variable energy usage | Generally stable energy demand |
Application Range | Suitable for smaller systems | Versatile for various sizes |
Cooling Efficiency | Well-suited for high pressures | Effective cooling in most cases |
Environmental Impact | Emissions and noise concerns | Generally lower environmental impact |
Adaptability | Limited adaptability to changes | Adaptable to varying conditions |
Lubrication | Frequent lubrication needed | Reduced lubrication requirement |
Heat Dissipation | Potential overheating issues | Effective heat dissipation design |
Lifecycle Costs | Higher overall lifecycle costs | Lower overall lifecycle costs |
Market Availability | Widely available and common | Available with varied options |
Speed Control | Limited speed control options | Enhanced speed control methods |
Energy Efficiency | Varied energy efficiency based on load | Consistently high energy efficiency |
Carbon Footprint | Potentially higher emissions | Generally lower carbon footprint |
Innovation | Limited recent innovations | Continuous innovation in design |
Installation Flexibility | Limited installation options | More installation flexibility |
Oil Contamination Risk | Risk of oil contamination in output | Minimal risk of contamination |
Material Compatibility | Restricted to certain gases | Compatible with various gases |
Remote Monitoring | Limited remote monitoring | Enhanced remote monitoring |
Maintenance Intervals | More frequent maintenance needed | Longer intervals between maintenance |
Noise Reduction | Limited noise reduction options | Advanced noise reduction methods |
Control Systems | Conventional control systems | Advanced control and automation |
Resilience | Susceptible to certain conditions | Higher resilience in various environments |
Lifespan | Comparatively shorter lifespan | Longer operational lifespan |
Efficiency under Load Variations | Less efficient at varying loads | Consistently efficient performance |
This detailed table delves into the efficiency considerations associated with Reciprocating and Rotary Compressors. It includes a wide range of parameters such as installation flexibility, the danger of oil contamination, material compatibility, remote monitoring capabilities, maintenance intervals, noise reduction techniques, control systems, durability, longevity, and efficiency under load changes.
Reciprocating vs Rotary compressor: Which is more Costly?
In the realm of compressors, the decision between reciprocating and rotary options involves a comprehensive evaluation of costs and benefits. While the initial financial outlay may differ, the long-term advantages of one over the other can significantly impact your overall investment. Here’s a detailed comparison of key considerations:
Type | Efficiency | Price Range | Operating Costs | Application Suitability |
Reciprocating | Variable efficiency | $500-$3,000 per unit | Moderate | Small-scale operations, intermittent use |
Rotary | Consistent efficiency | $1,000-$5,000 per unit | Moderate to high | Continuous operations, larger systems |
Differences between Reciprocating vs. Rotary compressor
Understanding the fundamental differences between reciprocating and rotary compressors is critical for determining the best choice for your individual needs. Here’s a more detailed description of the fundamental differences between these two compressor types:
Aspect | Reciprocating Compressor | Rotary Compressor |
Compression Mechanism | Utilizes a piston-driven back-and-forth motion to compress gas within a cylinder. | Utilizes rotating mechanisms such as screws or vanes to compress gas. |
Efficiency | Efficiency can vary based on load and demand, making it suitable for fluctuating requirements. | Offers consistent efficiency across load ranges, ideal for steady-state conditions. |
Maintenance | Requires more frequent maintenance due to its intricate piston and valve components. | Demands less frequent maintenance due to simpler construction and fewer moving parts. |
Size and Portability | Bulkier and less portable due to its larger mechanical components and piston-cylinder system. | Compact and lightweight due to simplified construction, suitable for space-restricted installations. |
Noise and Vibration | Can generate noticeable vibration and noise due to its reciprocating motion and impact loading. | Generally quieter and smoother operation due to the rotary motion’s continuous and even nature. |
Cooling | Efficiency slightly affected by the need for cooling systems to manage higher temperatures. | Features effective internal cooling mechanisms that help maintain stable operating temperatures. |
Application Range | Suited for smaller systems and intermittent use due to its adaptability and versatility. | Well-suited for larger systems and continuous operations that require consistent compression. |
Adaptability | Adaptable to varying demand and load fluctuations, making it suitable for dynamic requirements. | Adaptable to steady-state conditions, excelling in applications that demand stable pressure levels. |
Initial Cost | Generally has a lower upfront cost compared to rotary compressors due to its simpler design. | Often comes with a higher initial investment due to its precision engineering and advanced mechanisms. |
Energy Efficiency | Less energy-efficient at part loads compared to rotary compressors’ consistent efficiency. | Maintains high energy efficiency even at part loads, making it suitable for continuous operation. |
Control | Offers step or stepless capacity control, allowing for adjustments based on demand. | Employs continuous capacity modulation techniques for precise and efficient control of compression. |
Material Compatibility | Limited compatibility with certain gases due to its reciprocating nature and potential oil contamination. | Compatible with various gases and less prone to oil contamination, offering operational versatility. |
Lifespan | Generally has a comparatively shorter operational lifespan due to higher wear and tear of moving parts. | Boasts a longer operational lifespan due to reduced wear and smoother rotary motion. |
Precision and Stability | Potential variation in output due to its cyclic nature and sensitivity to load changes. | Offers stable and precise output due to continuous rotary motion, suitable for consistent processes. |
Industries | Suited for applications with intermittent use, such as pneumatic tools and variable-load demands. | Ideal for applications requiring continuous use, such as air compressors, refrigeration units, and steady-state processes. |
Operating Principle | Utilizes a piston-driven motion to draw in and compress gas within a cylinder. | Leverages rotating components to compress gas, delivering continuous and uniform operation. |
Noise Level | Can be noisier due to its start-stop motion and impact loading during compression strokes. | Generally quieter due to its smoother rotary motion and reduced impact on compression. |
Cooling System | Can require additional cooling systems to manage the heat generated during compression. | Features effective internal cooling mechanisms that dissipate heat, maintaining operational efficiency. |
Speed Control | Offers limited speed control options due to its piston-driven mechanism. | Employs advanced speed control methods, allowing for precise adjustments and modulation of capacity. |
Environmental Impact | Can potentially raise emissions and noise concerns in certain settings due to its operating characteristics. | Generally has a lower environmental impact due to quieter operation and reduced emission potential. |
Innovation | Limited recent innovations compared to rotary compressors, due to its mature technology. | Undergoes continuous innovation in design and technology, incorporating advanced features for enhanced efficiency. |
Maintenance Intervals | Requires more frequent maintenance intervals due to its numerous moving parts and wear-prone components. | Demands longer intervals between maintenance due to its streamlined design and reduced wear factors. |
Capacity Range | Offers variable capacity based on design and load requirements, catering to a range of application needs. | Provides high flow capacity options, making it suitable for applications requiring significant air volume. |
Control Systems | Utilizes conventional control systems for adjusting capacity and managing compression. | Incorporates advanced control and automation systems for precise modulation and efficient operation. |
This extensive chart delves into the distinctions between reciprocating and rotary compressors. You can make an informed choice that aligns with your project’s unique requirements by considering factors such as vibration, speed control, lifespan, capacity control, energy efficiency, adaptability, lubrication, heat dissipation, material compatibility, precision, initial cost, application flexibility, environmental impact, and control systems.
Reciprocating vs rotary compressor: Pros & Cons
Reciprocating Compressor Pros & Cons:
Pros | Cons |
Simple design and construction | Potential for more vibration and noise |
Lower upfront cost | Maintenance can be more frequent and involved |
Suitable for small-scale applications | Lower efficiency at varying loads |
Adaptable to varying demand | Reduced continuous duty suitability |
Ease of maintenance and repair | Overall lifespan might be shorter |
Widely available and common | Limited capacity for high flow rates |
Can handle variable pressure requirements | Prone to wear and tear of moving parts |
Well-suited for intermittent operations | Limited suitability for large-scale systems |
Familiar technology and service expertise | Limited efficiency in high-speed operations |
Rotary Compressor Pros & Cons:
Pros | Cons |
Consistent efficiency | Higher initial investment |
Quieter and smoother operation | Limited adaptability to varying loads |
Compact and portable design | Possible complex maintenance and repairs |
Better suited for continuous operations | Potential for higher energy consumption |
Longer operational lifespan | Reduced efficiency under lighter loads |
Less vibration and noise | Limited capacity for extremely high pressures |
Energy-efficient at part loads | Limited suitability for small-scale applications |
Reduced risk of contamination | May require specialized skills for maintenance |
Precise control of output | Sensitive to variations in intake conditions |
Can handle higher flow rates | Can have limitations in extreme temperature condition |
These tables give a complete overview of the many benefits and drawbacks of both reciprocating and rotary compressors. By taking these extra considerations into account, you can conduct a more complete assessment and select the type of compressor that best matches with the unique objectives and goals of your project.
Which Type of Compressor Should You Choose?
When selecting between rotary and reciprocating compressors, a thorough evaluation of your specific requirements is essential. For varying demand scenarios, rotary compressors offer steady efficiency, while continuous operations benefit from their reliability. Energy efficiency should match your needs; rotary compressors maintain stability, unlike reciprocating ones. Maintenance frequency varies reciprocating compressors demand more due to moving parts. Noise-sensitive environments favor rotary compressors, known for quieter and less vibrating operation. Rotary compressors excel in adapting to demand changes and precision requirements.
Consider initial cost versus long-term value; rotary compressors may have a higher upfront expense but offer extended lifespan. Factor in total ownership costs, including maintenance. For confined spaces, rotary compressors’ compact design is advantageous. Environmental impact and industry compliance play roles, as do supplier availability and expert consultation. Testing both types in your context aids decision-making. Long-term goals, scalability, and operational factors, such as oil contamination risks and environmental conditions, should guide your choice.
Choosing between rotary and reciprocating compressors depends on demand, efficiency, maintenance, noise, adaptability, cost, environment, compliance, and long-term goals. Expert advice and testing help inform the decision.
People May Ask: FAQs
Which compressor type is more suitable for continuous operations?
Rotary compressors are better suited for continuous operations due to their consistent efficiency, smoother operation, and ability to handle uninterrupted duty cycles. Their continuous rotary motion makes them ideal for applications where steady and reliable compression is essential.
What are the advantages of rotary compressors in terms of space utilization?
Rotary compressors have a compact and lightweight design, which makes them ideal for installations with space restrictions. Their streamlined construction allows for more flexibility in positioning and is favored in settings where efficient space utilization is a priority.
How do these compressor types handle changes in temperature?
Reciprocating compressors might encounter challenges with overheating, especially under high-temperature conditions, due to their start-stop motion. In contrast, rotary compressors are designed with effective heat dissipation mechanisms, making them more suitable for operations in varying temperature environments.
Are reciprocating compressors more cost-effective than rotary compressors?
Reciprocating compressors generally have a lower initial cost compared to rotary compressors. However, the long-term advantages of rotary compressors, such as consistent efficiency and longer operational lifespan, can offset their higher upfront investment.
In what scenarios would you recommend using a reciprocating compressor?
When cost-effectiveness and smaller-scale applications are important, reciprocating compressors are recommended. Simple, versatile, and adaptable, they are commonly used in industries that value simplicity and flexibility.
Conclusion
Finally, the choice between reciprocating and rotary compressors hinges on a range of factors. Reciprocating compressors offer cost-effectiveness and adaptability for smaller-scale applications, while rotary compressors excel in consistent efficiency and suitability for continuous operations. Efficiency, maintenance, noise levels, adaptability, and industry standards must all be weighed to make an informed decision.
Selecting the right compressor is not just about mechanical preferences; it’s a strategic step towards improved operational efficiency, reduced energy consumption, and alignment with specific industry demands. By understanding the distinct attributes of each type and their alignment with unique application needs, stakeholders can drive innovation, enhance productivity, and ensure sustainable progress in a dynamic landscape