In this article, we will learn what are water chillers in HVAC system, along with the definition, meaning, working, types, selection, applications, advantages, disadvantages, etc. Let’s explore!
What are Water Chillers in HVAC? Definition & Meaning
Water Chillers are widely used machines to remove heat from a liquid, and they are extensively used in industries. There are several chiller options available. The application, cooling temperature requirements, and cooling characteristics need to match the needs when choosing one. Significant parameters to ponder are the operating temperatures and pressures.
They vary in size; small chillers are available for smaller applications. While commercially or industrially, large chiller units are required, but the basic principle stays intact, and they provide cooling for HVAC systems as well as for the process industries.
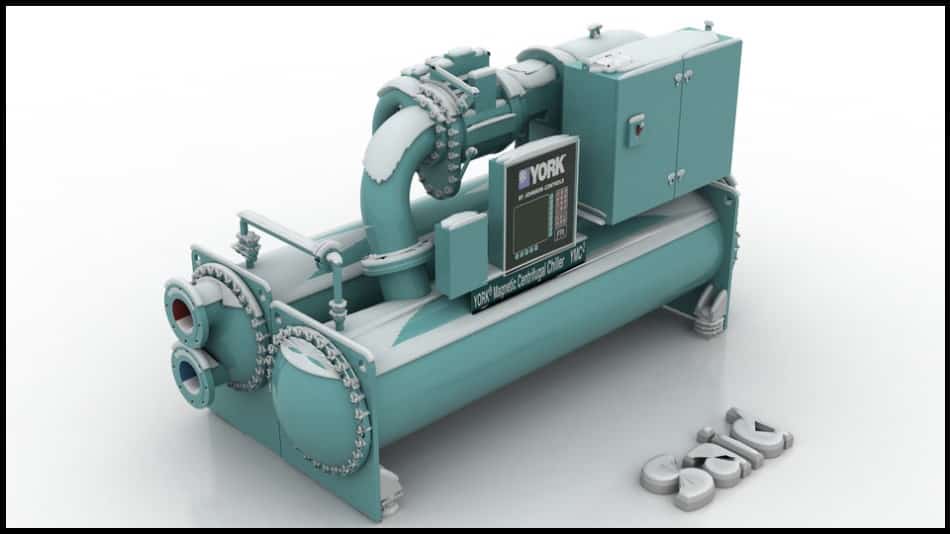
Chillers are significant to use. Machines are never 100% efficient, and they produce a lot of heat as a by-product that needs to be removed. If not removed, it can cause many issues such as reduced production times, equipment shutdowns, and premature equipment malfunctioning. Hence, it is essential to incorporate cooling into air conditioning systems and industrial process to prevent such problems.
- Industrial chillers function through a refrigeration system that removes heat and transfers it to somewhere else.
- They are used to lower the temperature of machinery, industrial spaces, and process fluids.
- Hence, these industrial chillers play a vital role in temperature regulation in several industrial operations such as HVAC systems, injection molding, oilfield production, metal plating, and food processing.
- Similarly, chillers are also found in medium to large-sized buildings to produce chilled water for air conditioning.
- All types of chillers differ slightly; however, the essential components and working principles stay intact.
Principle of Chiller’s Operation
Chillers operate on some principles. They are:
01. Phase change in Chillers
The liquid coolant or refrigerant undergoes a phase change and transforms into a vapor or gas when heated. This is one of the most common properties of a refrigerant. This phase change started in the evaporator. At normal pressure and temperature, refrigerant starts evaporating, which means liquid refrigerant changes its phase into vapor. This gaseous refrigerant or coolant will condense back into liquid when supercooled.
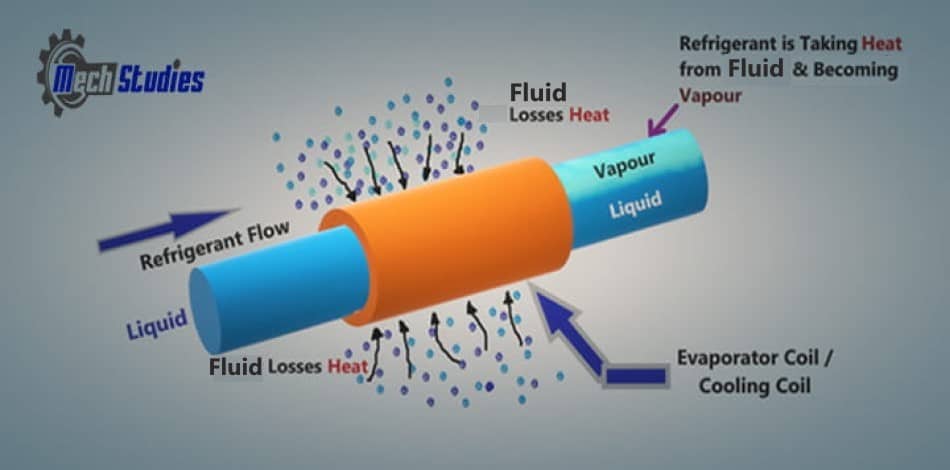
Look at the image. Refrigerant flows as liquid, gradually taking heat from surrounding fluid, then evaporating and simultaneously converting into vapor. We know that, for evaporation, the refrigerant has to take heat from somewhere, and here, it is adjacent to the surface of another fluid.
02. Heat flow in Chiller
Heat flow is an important aspect that takes place in chillers. Heat energy always flows from an area of high concentration of heat to an area of low concentration of heat. The heat is transferred from the load system/process (especially where the load occurs, for example, AHU coils) then it goes to the refrigeration circuit (i.e. chillers) and finally to the condenser circuit where it is exhausted to the atmosphere.
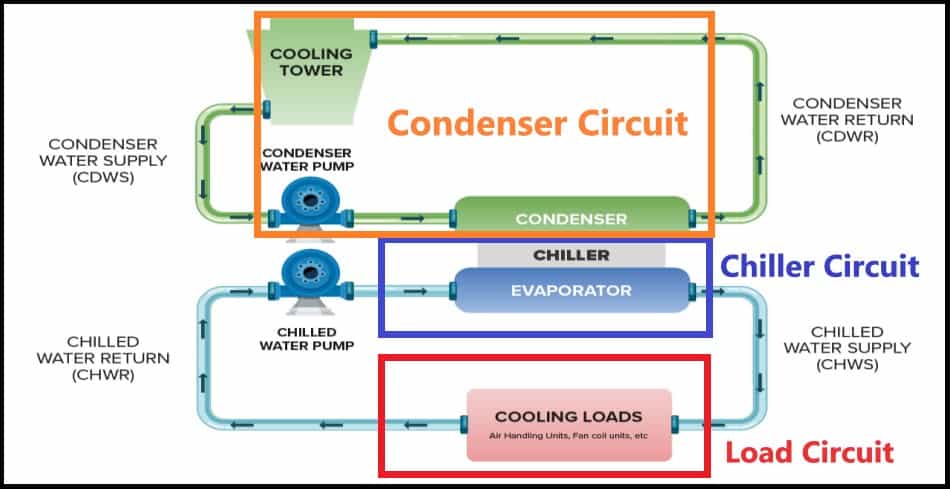
Load system/circuit ——-> Refrigeration circuit ——–> Condenser circuit
03. Boiling point of Refrigerant
We know that boiling point and pressure have a relationship. If pressure is increased then the boiling point will increase and if pressure is decreased then the boiling point will be decreased. An example of boiling point of most used refrigerant R 410a has been added for reference.
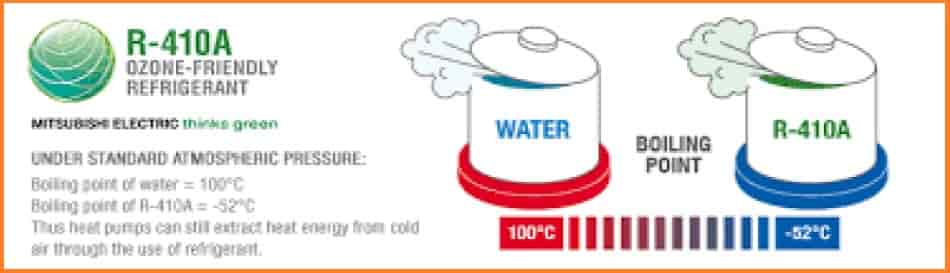
Hence, the boiling point of the refrigerant reduces when pressure on the refrigerant decreases and the boiling point of the refrigerant increases if the pressure of the refrigerant increases. These are the basic working principles of chillers. The essential components of chillers and working are further discussed in-depth in terms of these principles.
Parts of Water Chillers in HVAC system
A chiller is an essential component of HVAC systems that provides cooling by removing heat from water or air. It is used in commercial, industrial, and large-scale residential applications. Chillers consist of various components that work together to facilitate the cooling process. Here are the major key parts of a chiller:
- Compressor
- Condenser
- Evaporator
- Expansion valve
- Power panel
- Control unit
- Water box
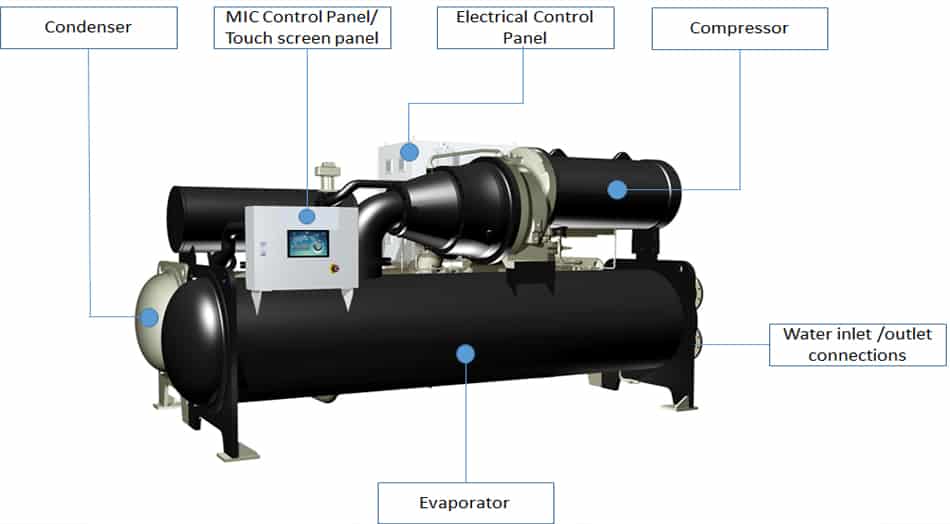
In addition to the major parts, there are many auxiliaries in each chiller, however, the same depends on the manufacturer, type of application, capacity, energy efficiency requirements, etc. For example, we have attached a part diagram for a Carrier made high efficiency chiller. Here, many other components have been added.
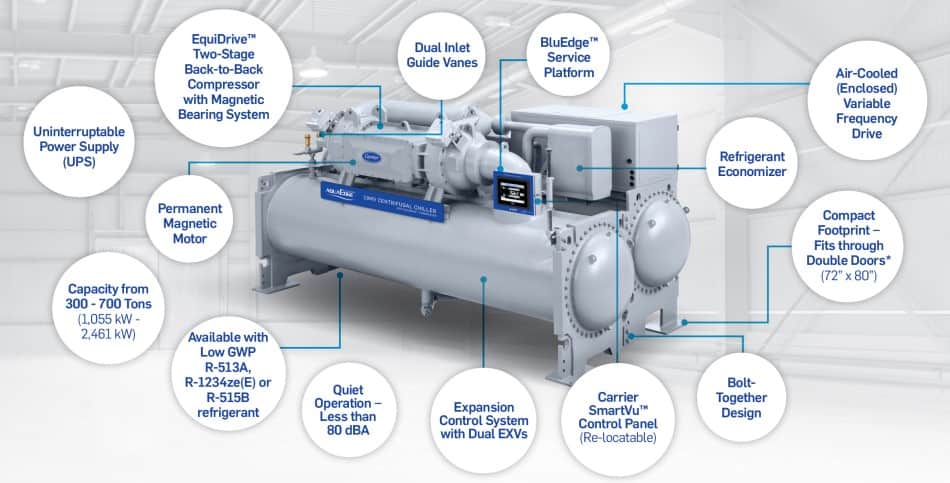
Compressor | Pressure Relief Valve |
Condenser | Power Panel |
Expansion Valve | Control Panel |
Evaporator | Water Box |
Refrigerant | Refrigerant Economizer |
Receiver | Variable Frequency Drive |
Suction Line | Inlet Vane Guide |
Discharge Line | Oil Pump |
Vibration Isolator | Foot and Nut/Bolt |
Oil Separator | Lifting Lug |
Let’s see all the components of water chiller in a chiller water system design.
01. Compressor
There are numerous types of refrigerant compressors; the widely used ones include scroll, screw, centrifugal, and reciprocating types of compressors.
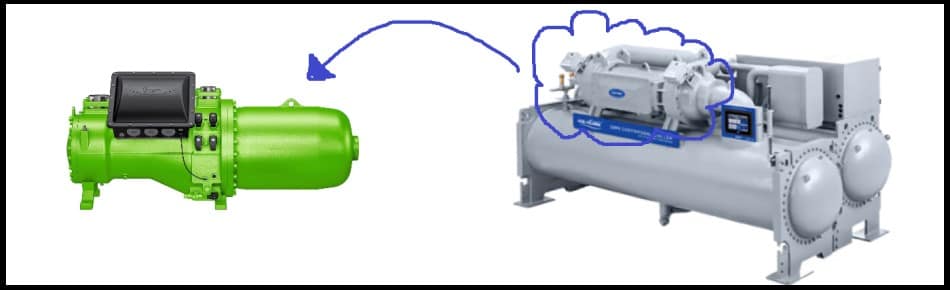
- Each of them has its own merits and demerits, but the compressor is the prime component of the chiller.
- It is located right between the condenser and evaporator of the chiller and is insulated.
- There is a motor attached either externally or internally to the compressor as a driving force.
02. Condenser
The condenser is located next to the compressor, right before the expansion valve. The evaporator picks up heat from the refrigerant, and this heat needs to be removed.
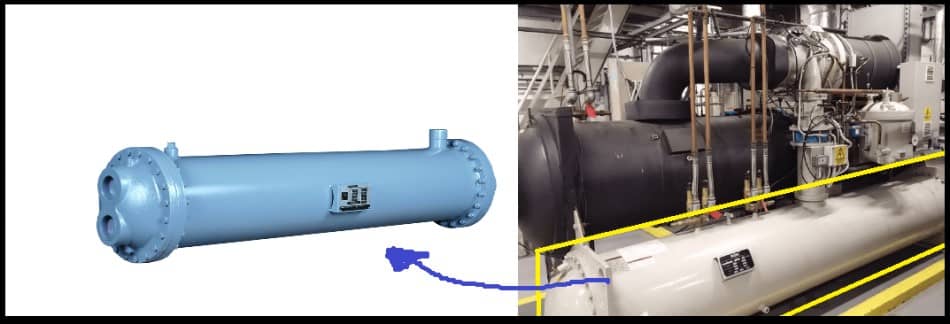
- For this purpose, the chillers have condensers installed in them.
- The function of the condenser is slightly different in water and air-cooled chillers.
- They are among the types of chillers discussed in detail in the “types” section of the blog.
03. Expansion valve
There is a valve present between evaporator and condenser, which is known as an expansion valve. The common types of expansion valves fitted in chillers include pilot-operated thermal expansion valves, electronic expansion valves, thermal expansion valves, and fixed orifice expansion valves.
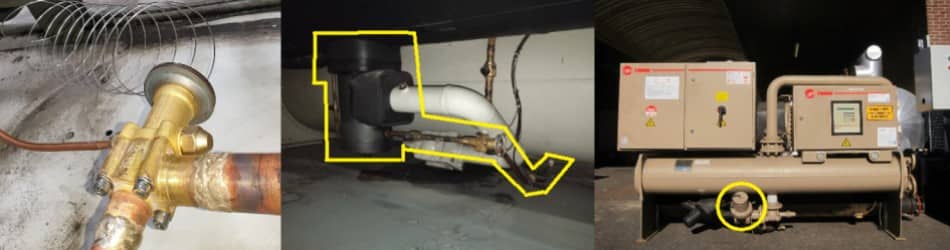
- Despite the different types, the primary function is the same.
- Expansion valves function by increasing refrigerant volume and decreasing the pressure to easily pick the extra heat from the evaporators.
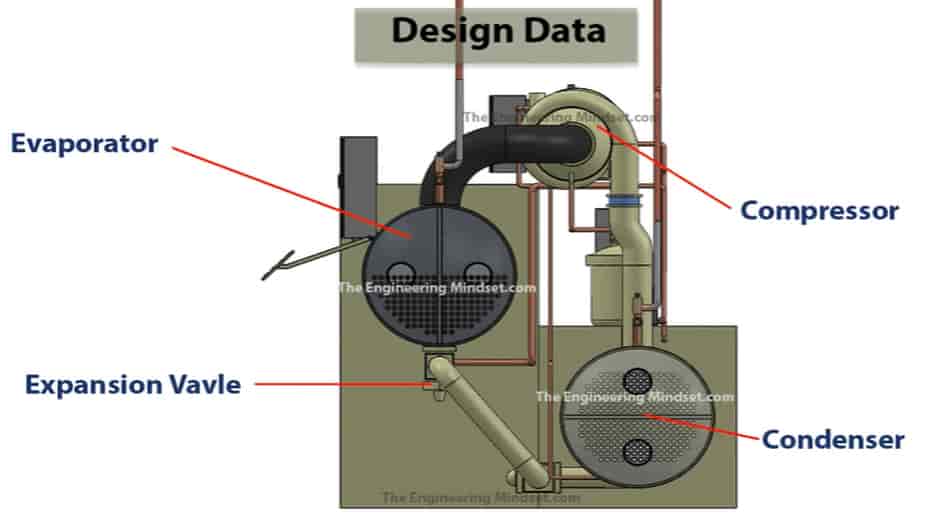
04. Evaporator
Between the expansion valve and compressor, there is an evaporator. The primary purpose of the evaporator is to collect the extra heat and move it into the refrigerant, which sends it further to the cooling tower.
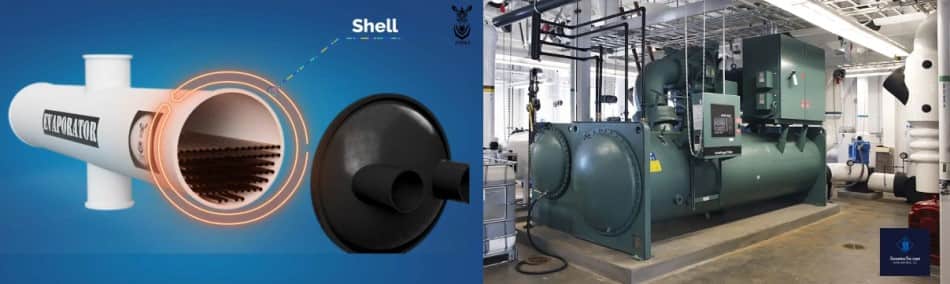
- When heat is extracted from the refrigerant, water cools down.
- The chilled water is then utilized in producing cooling.
- It then returns to the evaporator so that the unwanted heat is removed again. In this way, the cycle continues.
05. Refrigerant
The refrigerant is the medium that circulates through the chiller system, absorbing and rejecting heat as it changes state from liquid to gas and vice versa. Common Types of Refrigerants are R-134a, R-410A etc.
06. Receiver (Refrigerant Receiver)
The refrigerant receiver stores excess refrigerant, ensuring that there is always enough refrigerant in the system for optimal operation. It also acts as a buffer to maintain the refrigerant flow. Typically located between the condenser and expansion valve.
07. Suction Line and Discharge Line
These are the refrigerant pipes that connect the various parts of the chiller. The suction line carries the low-pressure refrigerant gas from the evaporator to the compressor, while the discharge line carries the high-pressure refrigerant from the compressor to the condenser.
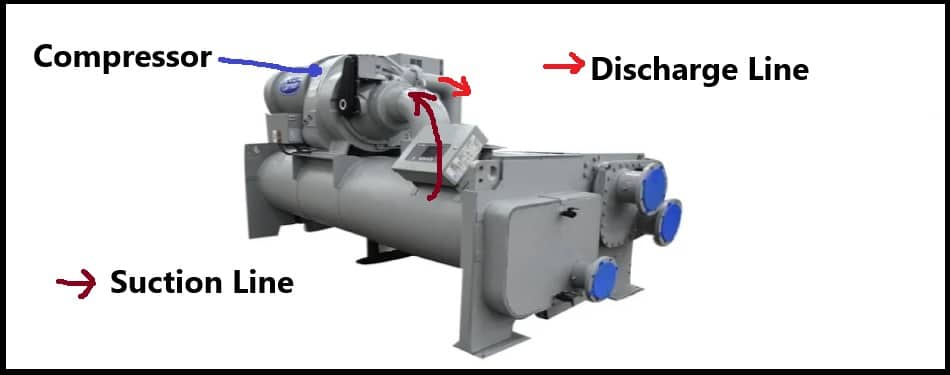
08. Vibration Isolators
Vibration isolators are used to absorb vibrations from the compressor and other moving parts, preventing them from being transmitted to the surrounding environment and structures.
09. Oil Separator
In some chiller systems, the oil separator helps separate oil from the refrigerant to ensure efficient compressor operation and prevent contamination of the refrigerant system.
10. Pressure Relief Valve
The pressure relief valve is a safety device designed to protect the chiller from high-pressure conditions that could damage the system. It automatically releases refrigerant if the pressure exceeds safe levels.
11. Power Panel
The power panel is mounted on chillers in industries; it may be mounted directly to chillers or fixed to the room’s wall where the plant is located.
- The power panel constitutes many power cables, and its function is to control the flow of electrical power to the chillers.
- The primary components of the power panel are circuit breakers, starters, speed controllers, and power monitoring equipment.
12. Control unit
The control unit is located on the chiller. It monitors several aspects like the chiller’s performance and has adjustments for the proper functioning of the chiller.
- In case of emergencies, it can generate alarms and automatically turn off the system to prevent hazards.
- For remote control and monitoring, BMS connections are also available in the control unit.
13. Water box
Water boxes are present along with condensers and evaporators in water-cooled chillers. The number of entrances in the water box depends on the number of passes in the evaporator and condenser.
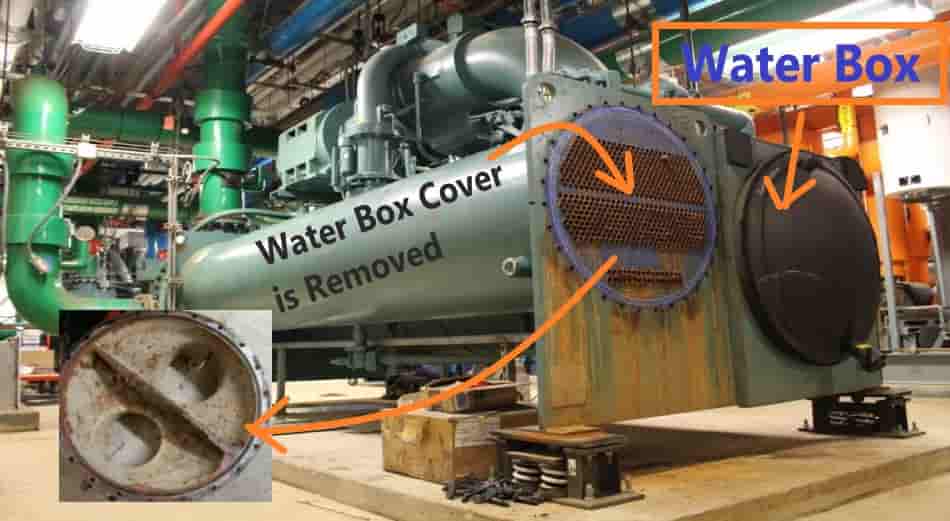
The primary function of water boxes is separating the entrance and exit paths and also aids in directing the flow. You can explore AHU video with Site Tour
How Does Water Chiller Work?
After discussing the working principle and components, let’s get into the working process of chillers. A pumping system circulates cool water or glycol solution (for process chillers) from the chiller into the required areas. The cool fluid removes unwanted heat from the process when hot liquid returns—the heat transfers from the system to the chiller by water.
Different types of pumps are used in chilled water systems. Chiller is a part of a chilled water system. Below pumps are used for chilled water system.
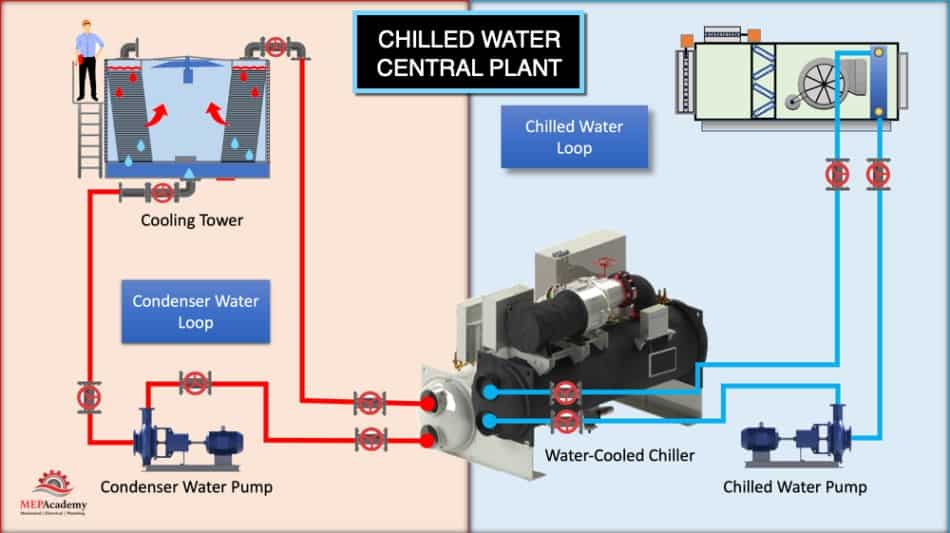
- Chilled water pumps for circulation of water from chillers to the system or building or process which needs to be cooled.
- Condenser water pumps for circulation of condenser water between condenser and cooling towers.
- Dosing pumps are provided for the chemical dosing in chilled water pipes to reduce the formation of scale.
A chemical compound known as a refrigerant is present in chillers. There are several types of refrigerants depending upon the required temperatures. For examples,
- R134a
- R410a
- R1234yf etc.
However, the basic principle of compression and phase change of refrigerant from liquid to gas and back to liquid stays intact. This whole process of phase change, heating, and cooling is known as the refrigeration cycle.
The refrigeration cycle begins with a low-pressure liquid/gas mix that enters the evaporator. The heat from process water or water/glycol solution boils the refrigerant inside the evaporator. It results in a change from a low-pressure liquid into a low-pressure gas.
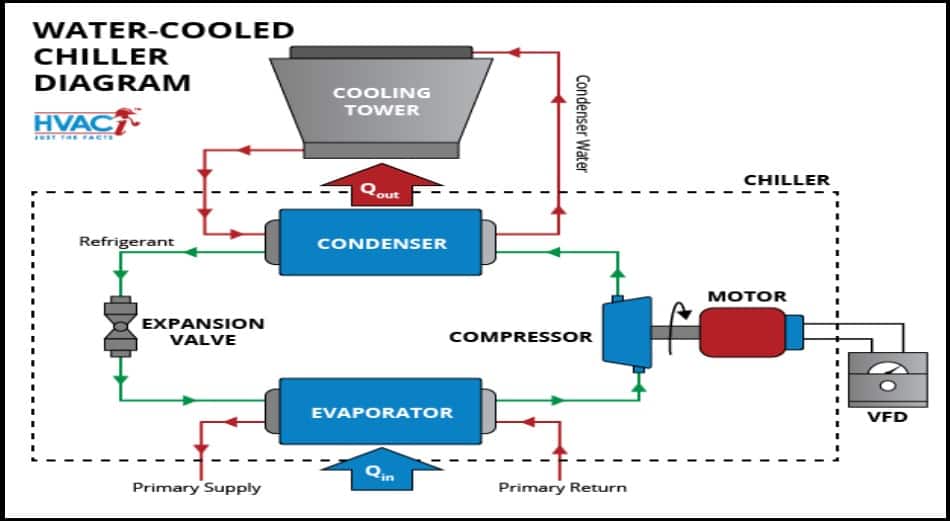
Now, the compressor compresses low-pressure gas into high-pressure gas. This high-pressure gas enters the condenser, where ambient air or condenser water removes the heat. In this way, the high-pressure gas converts to a high-pressure liquid.
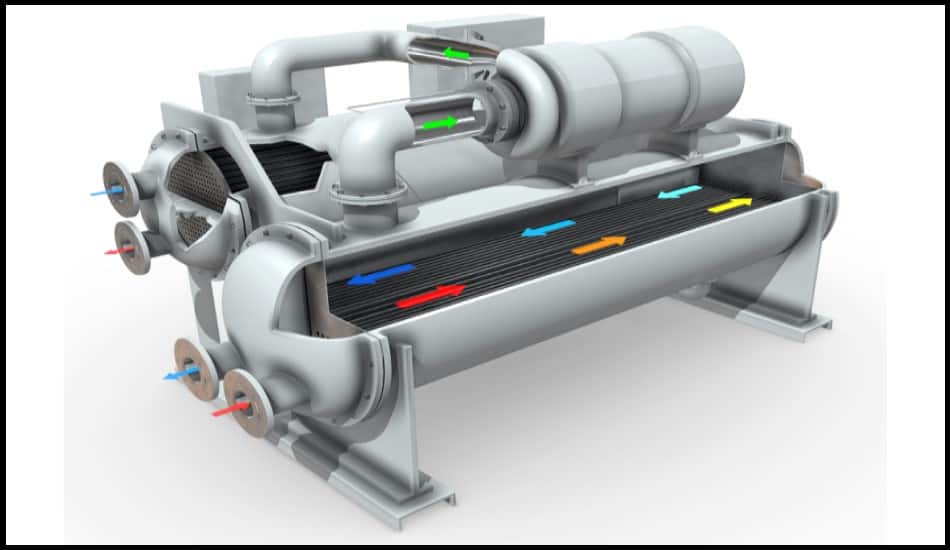
The high-pressure liquid now enters the expansion valve. The valve controls the amount of refrigerant liquid entering the evaporator, allowing the refrigeration cycle to start again. The condensers are of two types; either water-cooled or air-cooled. In the latter, water from the cooling tower is used to cool and condense refrigerants. On the contrary, the air-cooled condenser uses ambient air to cool and re-condense the heated refrigerant gas into the liquid.
Types of Chillers
There are numerous types of chillers. Chillers are both commercially and industrially used for cooling. The types are:
01. Water-cooled Chillers
Water-cooled chillers are the most common type of chillers, and they utilize water from an external tower to cool the gaseous refrigerant in the chiller’s condenser. In this way, refrigerants can undergo a phase change, and the refrigeration cycle goes on.
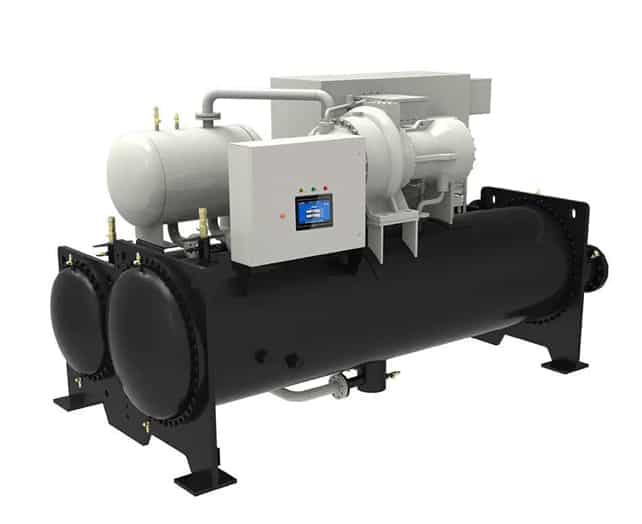
- They are pretty efficient as compared to air-cooled chillers.
- Moreover, they are versatile because they are used for both small-scale and industrial purposes.
- They are compact, portable, and quieter.
02. Air-Cooled Chillers
Instead of water, air-cooled chillers use ambient air for the refrigeration cycle to go on smoothly. Air fans are attached to them, which makes the cooling process pretty speedy. On the contrary, they are preferred less because they produce a large amount of heat. However, they are used in colder areas where heat discharge can keep the place warm. This way, it is beneficial.
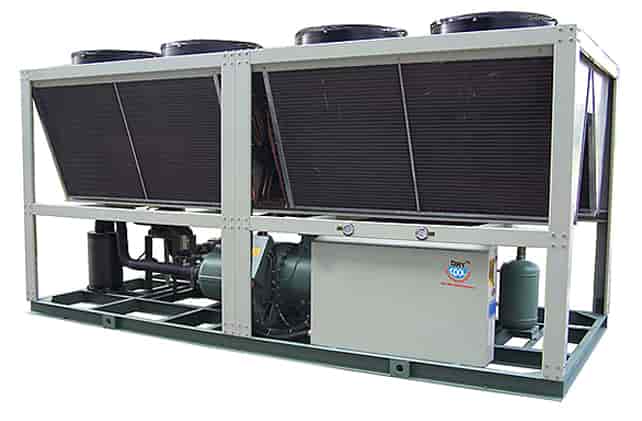
- Air-cooled chillers are cost-effective both in maintenance and installation, and it is available in portable solutions also.
- However, they use cooling fans that are pretty noisy, and Air-cooled chillers have a shorter life span than water-cooled chillers.
Classification of Industrial Chillers
Industrial chillers are further classified into the following types based on the transportation of refrigerant inside the system. The types are discussed below.
01. Vapor compression Chillers
Vapor compression chillers extract extra heat using a compressor to pump refrigerant.
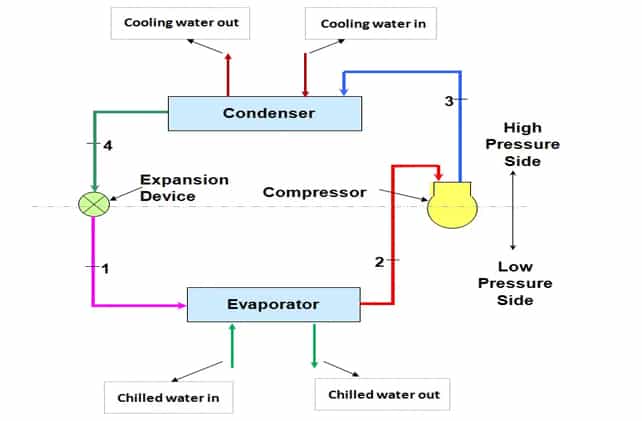
- The primary components stay the same, but it does not have an absorbent medium as in vapor absorption chillers.
- These chillers use electricity, steam, or gas turbines to power a mechanical compressor, and the cooling is produced using a vapor-compression refrigeration cycle.
02. Vapor Absorption Chillers
Vapor absorption chillers transport the refrigerant around the system for cooling using a heat source heated using water or steam.
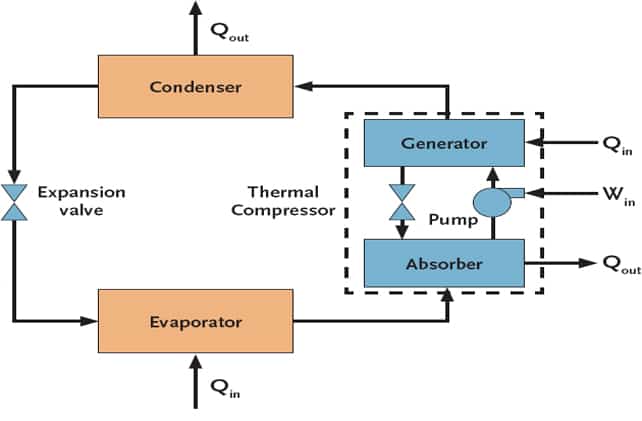
Let us see how a vapor absorption machine looks like at actual:
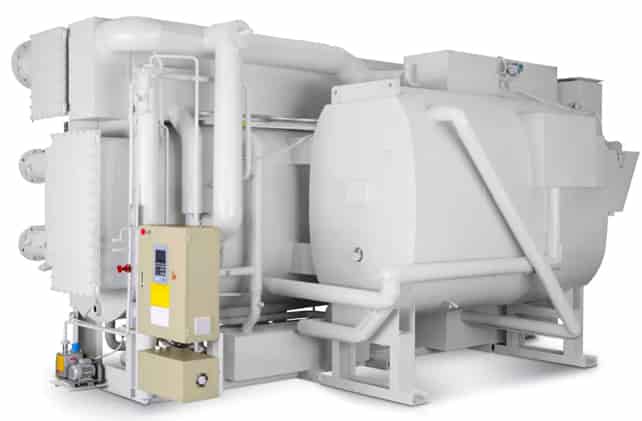
- The absorption medium is ammonia or lithium bromide, and the adsorption solution is regenerated through water or a stream.
- The components constitute an absorber, generator, and pump, and It doesn’t have a compressor as in a vapor compression chiller.
03. Screw Chillers
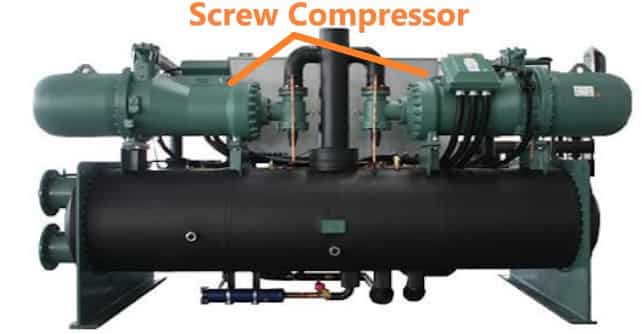
Screw chillers are vapor compression chillers, and it uses a screw compressor to move coolant through the system. They are most suitable for high-rise buildings and offer high energy efficiency. Other benefits include low maintenance costs, quiet working, and compact installation.
04. Centrifugal Chillers
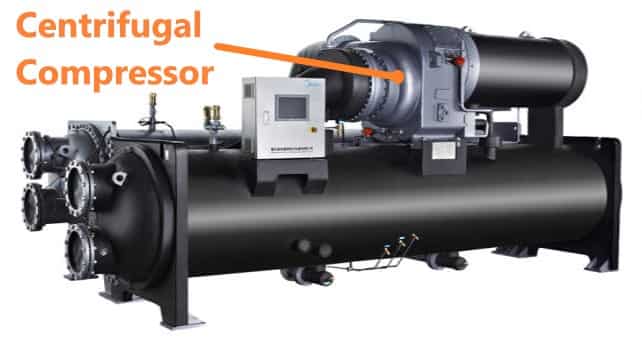
Centrifugal chillers are vapor compression chillers best for medium to large-scale cooling operations. They comprise an evaporator, compressor, condenser, and expansion valve fitted with a rotating impeller which aids in compressing the refrigerant and then transporting it through the system.
05. Reciprocating chillers
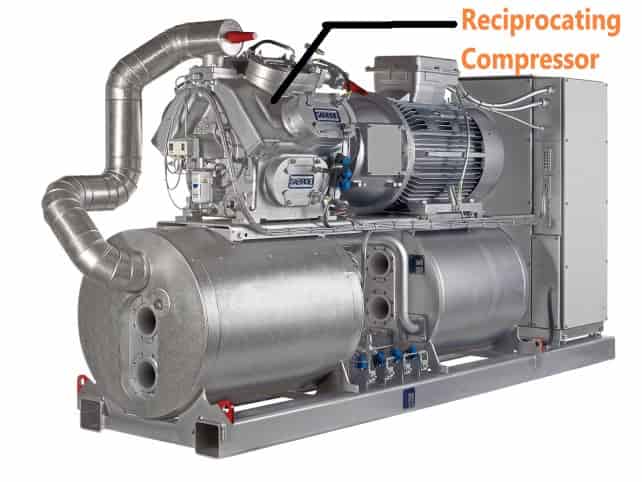
Reciprocating chillers use reciprocating compressors. They are pretty efficient as they deliver small refrigerant quantities at high pressure.
06. Scroll chillers
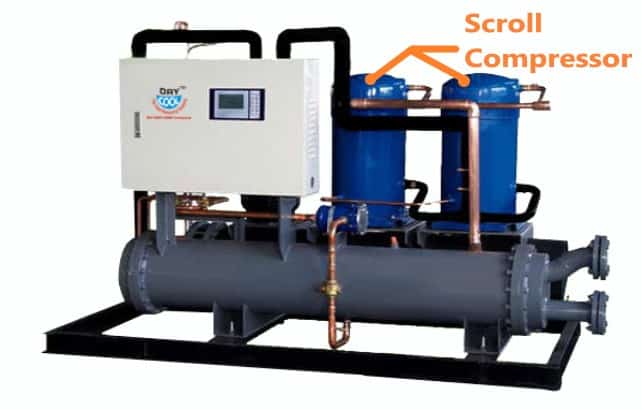
Scroll chillers constitute two spiral plates, one fixed and the other rotating to compress the refrigerant—the momentarily separating scrolls with a solenoid valve and electric modulation controls capacity.
How Do You Select Chillers in HVAC System?
Every environment is different, and every application requires a specific chiller for best results. There are several factors to select a chiller to ensure to meet the specific cooling needs of the applications. Below is a quick guide that will help you in selecting the appropriate chiller for your application.
01. Determine Cooling Load Requirements
Cooling Capacity: Estimate the total heat load (in tons or kilowatts) that needs to be removed from the system by various method like manual heat load calculation method, or Hourly analysis program (HAP) method, Elite software, or using simple Excel sheet using equations in line with standards.

For air conditioning, the cooling load is often expressed in tons of refrigeration (TR), where 1 ton = 12,000 BTU/hr. In many industrial projects, the load is expressed in kilowatts (kW) as well. Remember 1 TR = 12 BTU/hr = 3.516 kW. For example, as per calculation, the cooling load comes for a Substation 500 kW or 500/3.516 TR or 143 TR.
02. Determining the Cooling Medium, Temperature, and Flow Rate
After knowing the heat load, determine the coolant type, temperature, and flow rate. It is determined through the method of heat transfer from the process to the type of coolant used. The location of project matters. For example, if the location is in Sweden, the outside temperature may be -10 deg C or -15 deg. C and the cooling medium alone water is not practical as water will be changed its phase from liquid to solid ice. To avert this problem, propane is added in the water in proportions. However, this is not required if you select a chiller in Middle east!
03. Temperature Differential
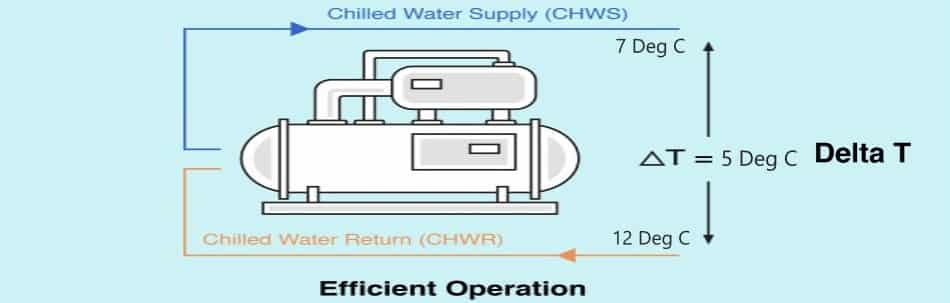
Consider the temperature difference between the inlet and outlet fluid temperature (Delta-T), as it affects the chiller’s performance.
04. Select the Type of Chillers
After knowing the cooling capacity, the type of chiller needs to be selected, whether it is air cooled, or water cooled or type of chillers based on compressor etc. shall be selected.
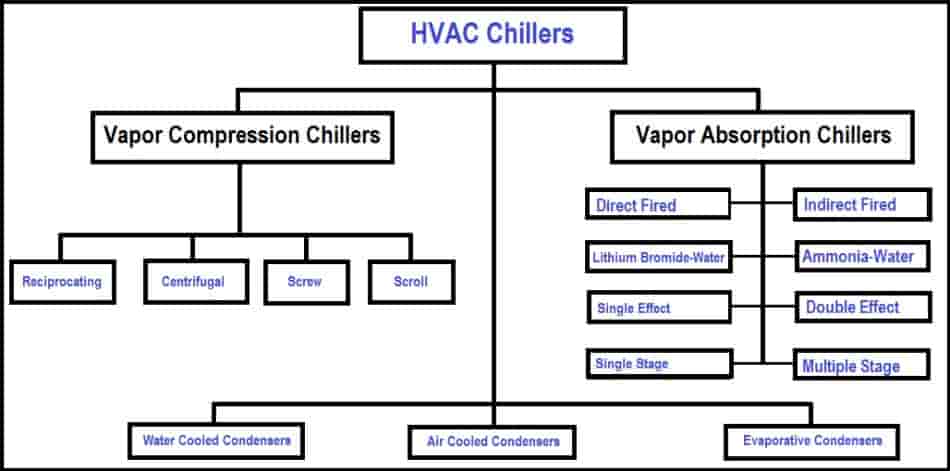
- Air-cooled Chillers: Best for small to medium-sized applications, where the system’s cooling needs don’t justify the cost or space requirements of a water-cooled system. Many times, individual building needs chiller and there is scarcity of water, that time air cooled chiller is the best option.
- Water-cooled Chillers: More efficient for large-scale applications and offer lower operating costs, but require access to a cooling tower or water source.
- Geothermal Chillers: Used in areas with access to geothermal resources for more sustainable cooling.
Each type has its own pros and cons in terms of efficiency, cost, and maintenance.
05. Consider Operating Environment and Space
Indoor or Outdoor Installation: Depending on your space, you’ll need a chiller suitable for either indoor or outdoor installation. Air-cooled chillers are installed outdoors as hot air from condenser are exhausted through condenser fans, while water-cooled chillers can be installed indoors or outdoors.
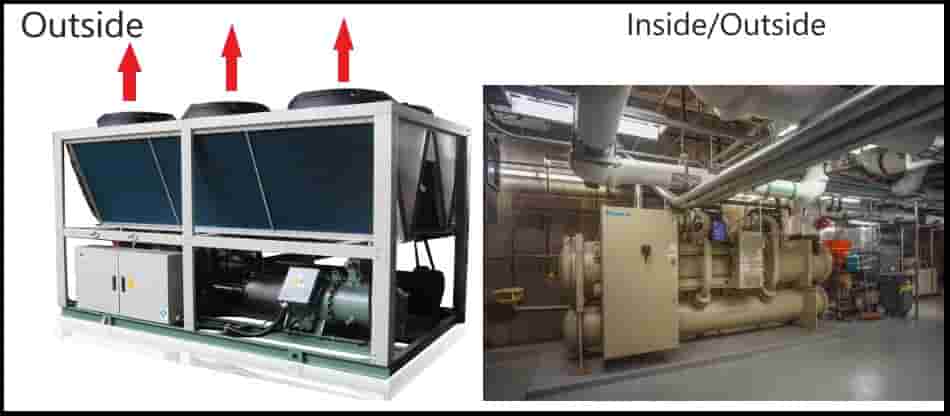
Ambient Temperature: The chiller must operate effectively within the local climate conditions. Ensure the unit can handle the highest and lowest expected temperatures.
06. Choose the Right Refrigerant
R-410A, R-134a, and R-32 are common refrigerants used in air conditioning and cooling systems. Each refrigerant has different properties such as pressure, efficiency, and environmental impact.
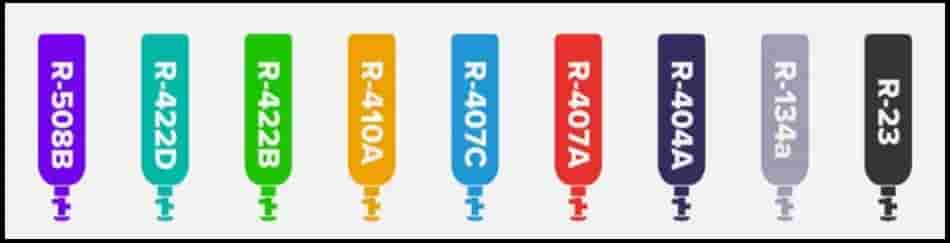
Look for refrigerants with low Global Warming Potential (GWP) as well as Low Ozone Depletion Potential (ODP) if sustainability is a priority.
067. Energy Efficiency and Operating Costs
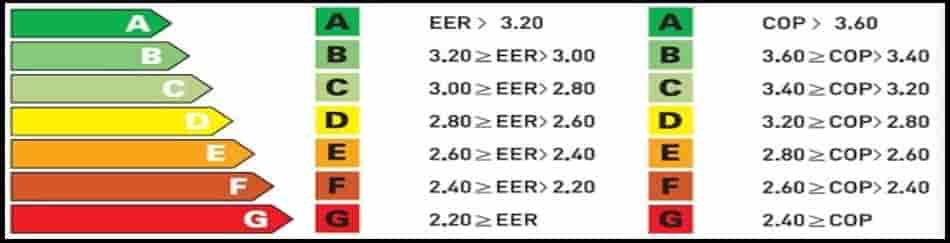
EER and COP: Look at the Energy Efficiency Ratio (EER) and Coefficient of Performance (COP), which measure the chiller’s efficiency. A higher number indicates better performance.
08. Part Load Applications
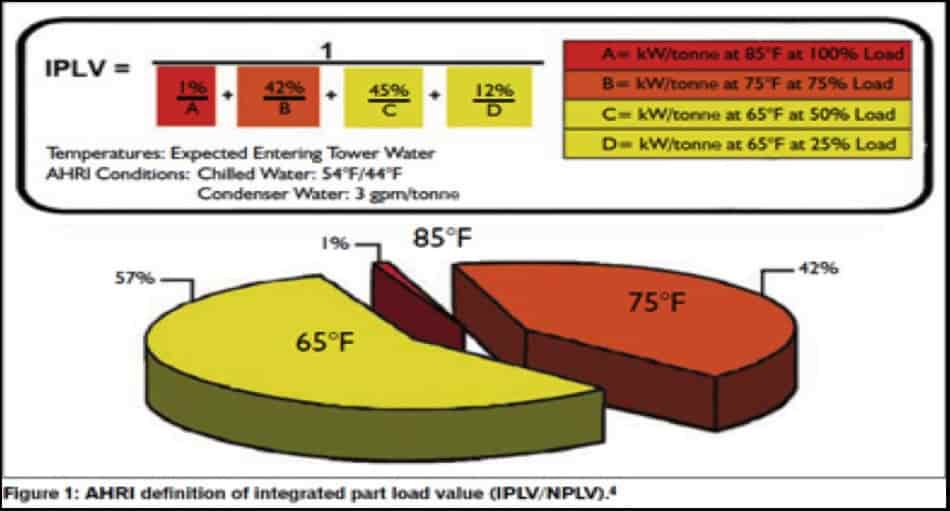
Depending on the application, if part load is application, then IPLV value shall be taken into considerations.
09. Variable Speed Drives:
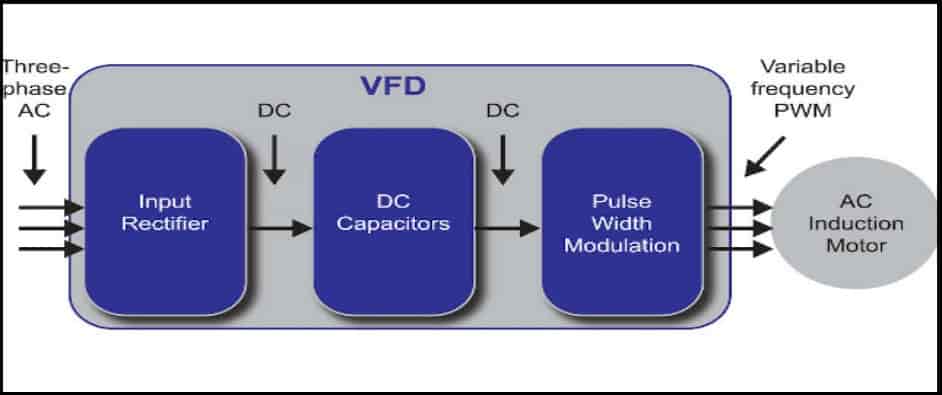
Consider chillers with variable-speed compressors, which can adjust their output based on cooling demand, improving efficiency and reducing energy costs.
10. Know the Performance Curves of Chiller
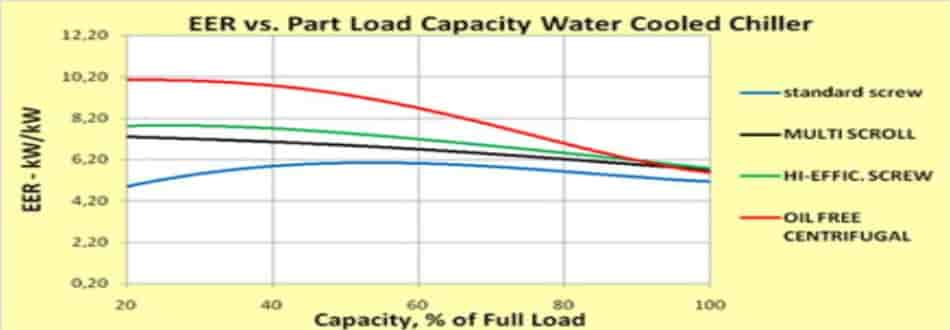
Use the chiller performance curves available with each model. Considering the application, an appropriate frame size is selected, and the capacity of the chillers and safety margins are taken into consideration.
11. Maintenance and Reliability
Choose chillers with easy access for maintenance, and check the reliability and service history of the brand. Coil removal space shall be kept in mind as it takes much space.
12. Warranty and Service Support:
Make sure there is adequate warranty and service support available locally.
13. Size
Ensure the chiller has enough capacity to handle peak loads, but isn’t oversized, as this can lead to inefficiency and higher operating costs.
14. Scalability
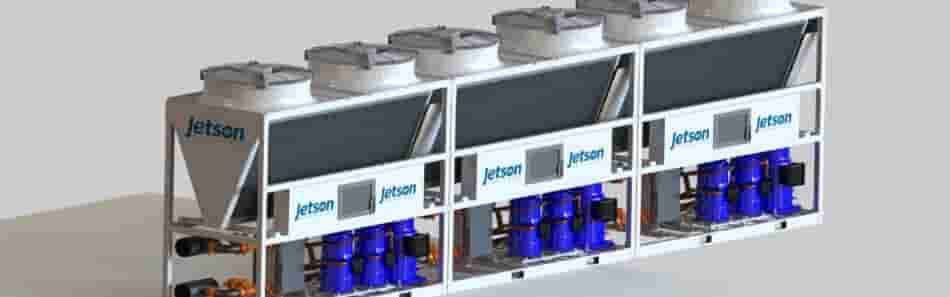
Some chillers are modular, meaning additional units can be added if future cooling needs increase.
15. Noise Levels
Consider the noise level of the chiller if it is installed in a noise-sensitive environment. Water-cooled chillers tend to be quieter than air-cooled ones.
16. Compliance and Regulations
Ensure the chiller meets all local codes and regulations related to energy efficiency, environmental impact, and safety.
17. Budget
Consider the initial cost of the chiller, as well as long-term operating and maintenance expenses. Opt for a balance between cost and efficiency.
18. Customization and Features
Some chillers come with features like smart controls, remote monitoring, or built-in redundancy to improve operational efficiency and prevent downtime. These may add to the cost but provide long-term benefits.
19. Area Classifications
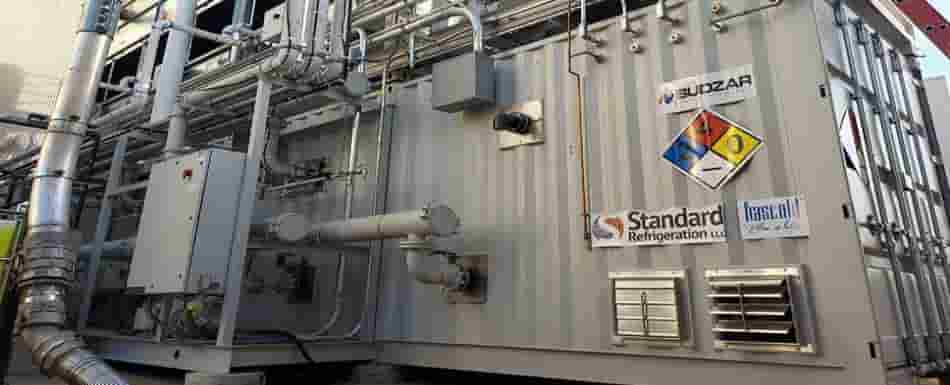
The classifications of chillers are one of the most important factors in the selection. If the chiller is to be served in a hazardous area then the protection shall be considered accordingly. For a Zone 2 area, the chiller shall be selected for Zone 2 only.
20. Life of Chillers
The life of the plant has a proper consideration for selection of chillers.
Select a chiller based on the specific needs of your system, the space available for installation, energy efficiency, and long-term reliability. It is required to check with chiller supplier or consultant to ensure that the selection is suitable for your applications.
What are the Common Issues Arise in Chillers?
Machines work well, but sometimes issues arise. Chillers are also machines, and there are a few common issues that you may face. They include:
01. Corrosion
Metal tubes (copper or carbon steel) are used to construct chillers, and their primary function is transferring water between the chiller and climate-controlled space.
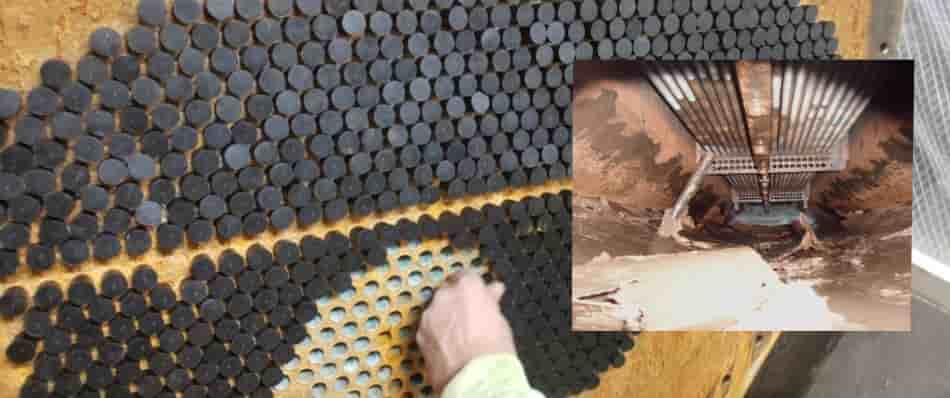
- Corrosion occurs because of oxygen, but we can overcome the risk through appropriate preventive measures.
- If the water treatment is inadequate, the system is vulnerable to sediments, minerals, and bacteria.
If sediment or bacteria builds up, the oxygenation level is disrupted, and metal corrodes. When two metals are used at some point in the system, there is more risk for corrosion.
It is due to differences in the electrochemical properties of both metals. Corrosion is terrible since it can cause leakage and damage the chiller and surrounding area, reducing the efficiency of chillers.
02. Maintenance problems
It is necessary to ensure that chillers are working correctly, for this maintenance is required. If not maintained adequately, it can lead to corrosion, clogging, loss of efficiency, and numerous other issues.
- The cooling towers need to be cleaned from time to time to prevent clogging in pipes due to the accumulation of particulates or sediments.
- Hence ensuring power maintenance is vital for the maximum efficiency of chillers.
03. Electrical issues
The electrical system inside chillers is complex and is vulnerable to malfunctioning. A high voltage surge can throw off balance and cause wear and tear in the whole electrical system.
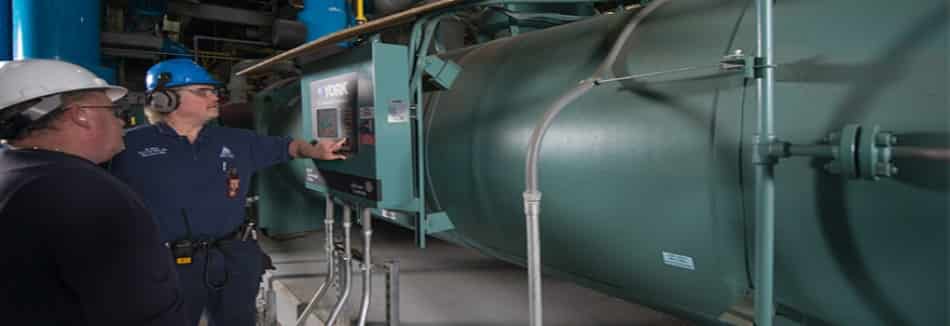
- Similarly, overloading the chiller can cause overheating, which results in electrical issues.
- Apart from this, the wires and cables may become loose over time, resulting in electrical malfunctioning.
General Arrangement (GA) Drawing of Chillers
A Chiller General Arrangement (GA) Drawing is a layout that provides a detailed illustration of the chiller system, typically showing the key components and how they are arranged in relation to one another for installation and operation. This drawing is essential for understanding the spatial relationships and ensuring proper installation.
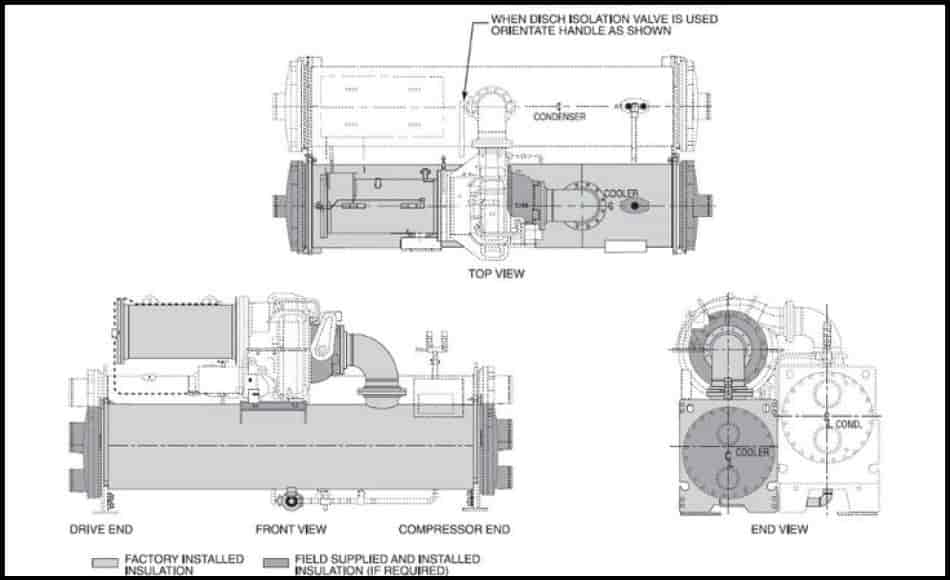
The main chiller body, which contains the compressor, evaporator, condenser, and expansion valve. Often highlighted as part of the chiller unit and typically located in the center or as part of a modular unit. Piping showing the flow of refrigerant from the compressor to the evaporator, through the condenser, and back to the expansion valve. The electrical connections for the chiller, including control panels and breakers. Locations for the control system, sensors, and monitors that allow for automation of the chiller operation. General Arrangement Drawing includes Top View, Side View, Isometric View, Installation Layout, Dimensions, Clearances, Flow Directions, Connection Points, Scope etc.
3D Models of Chillers
Creating or obtaining a 3D model of a chiller typically involves several options, depending on your specific needs, software expertise, and whether you’re looking for an existing model or want to create a custom one. Here are your main options for getting a 3D model of a chiller using CAD Software’s (AutoCAD, SolidWorks, Revit, etc.).
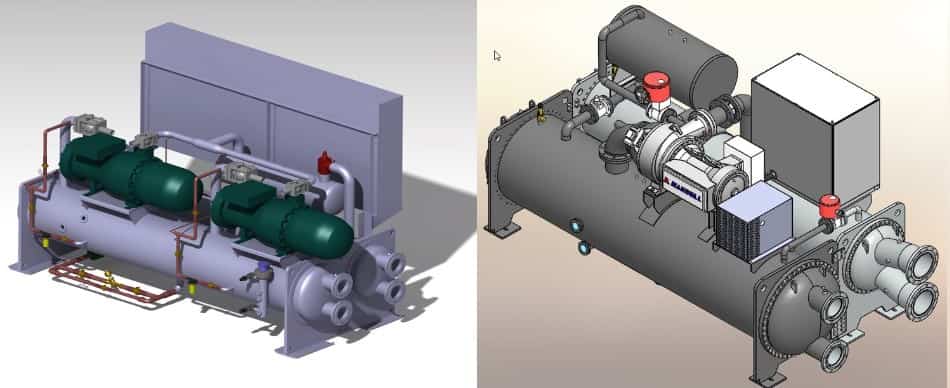
Many times, we get the 3D model of chillers from the suppliers like Carrier, Trane, York, Daikin as well.
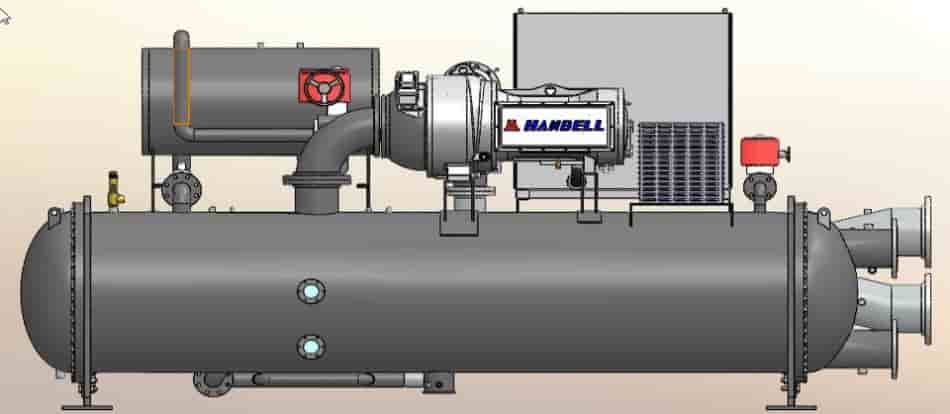
Explanation of Chiller Control Philosophy
Chiller control philosophy refers to the guidelines and strategies used to manage and optimize the operation of a chiller system. It ensures that the chiller operates smoothly, efficiently, responds to demand changes, and maintains the required cooling performance under various conditions. This philosophy is essential for energy savings, system reliability, and maintaining comfort or process requirements.
01. Setpoint Control
Temperature Setpoint | The desired temperature of the chilled water (supply temperature) is typically set based on the requirements of the building or process. For HVAC systems, this might be 42°F to 45°F (5.5°C to 7°C), while for industrial cooling, it might vary. |
Return Water Temperature | The system may also monitor the return water temperature to adjust the chiller’s operation to optimize performance. Return water temperature may be around 12°C. If the return water is hot than expected, the chiller may need to increase its cooling capacity. |
02. Load Variations
Load Changing | Chillers adjust their cooling capacity in response to the changing load demands of the system. The load is based on how much cooling is required at any given time, which can vary depending on factors like external weather, occupancy, heat generations, operations, or industrial process requirements. |
Variable Speed Control | Many modern chillers use variable frequency drives (VFDs) to modulate the compressor speed, allowing the chiller to adjust its cooling capacity based on demand. This improves efficiency and reduces energy consumption during partial load operation. |
Two-Stage or Multi-Stage Control | Some chillers operate in multiple stages, where different stages (compressor stages or evaporator flow rates) are activated depending on the load |
03. Lead-Lag Control (for Multi-Chiller Systems)
Lead-Lag Operation | In systems with multiple chillers, the control system alternates the operation of each chiller to balance wear and tear across the units and ensure redundancy. The “lead” chiller is the first to operate, while the “lag” chiller follows, activating as the load increases or if the lead chiller fails. This helps prevent one chiller from running too frequently, which can prolong equipment lifespan and improve system reliability |
04. Chiller Efficiency and Energy Optimization
Resetting Setpoints | Chillers can adjust their setpoints based on ambient conditions, such as outdoor air temperature. For example, if it’s cooler outside, the setpoint for chilled water temperature might be adjusted upwards to save energy |
Thermal Storage | Some systems use thermal energy storage (ice storage or chilled water tanks) to produce excess chilled water during off-peak hours, which can be used to meet cooling demand during peak hours. This helps reduce peak energy consumption and operational costs |
Staging Chillers | The system stages chillers based on the actual load. If the load drops significantly, one or more chillers may be turned off to save energy, and if the load increases, additional chillers are brought online. Normally in industry, chillers are considered like 2×100%, 3×50% etc., however, this depends on the project size as well as requirements. |
05. Sequence of Operation
A sequence of operation for the chiller and associated systems ensures smooth and coordinated functioning.
Chiller Start-Up | The chiller starts up only after verifying the necessary parameters (water flow, pressure, etc.) are in range |
Chiller Shutdown | When cooling demand is low or when maintenance is required, the system will shut down the chiller in a controlled manner, ensuring that the remaining chillers (if any) maintain the system’s operational integrity |
Safety Alarms | Control systems monitor operational parameters such as temperature, pressure, and water flow to protect the chiller from abnormal operating conditions. Alarms and fault indications will trigger if limits are exceeded |
6. Integrated Control with HVAC or Building Management System (BMS)
Communication Protocols | Chillers can communicate with a Building Management System (BMS) or Energy Management System (EMS) using protocols like BACnet, Modbus, or LonWorks. The BMS enables centralized control, optimization, and monitoring of the chiller system along with other HVAC and building systems |
Demand Response | A BMS can optimize chiller operation by integrating it with external energy management systems. For example, during periods of peak energy demand, the chiller operation can be adjusted or temporarily shut off to reduce energy costs |
Data Logging and Remote Monitoring | A control system records data such as operating hours, energy consumption, and fault history. This data can be used for predictive maintenance and troubleshooting |
07. Chilled Water Flow Control
Flow Control Valves | A modulating valve may be used to control the flow of chilled water to the system, ensuring the right amount of chilled water is delivered based on the cooling demand |
Temperature Differential Control | A differential pressure controller or flow sensor is used to maintain the correct balance between chilled water supply and return water, ensuring the system operates efficiently |
08. Load Shedding and Redundancy
Load Shedding | In some systems, if the cooling demand is less than the system’s capacity, the control system may “shed” load by turning off unnecessary pumps or shutting down cooling units, reducing the operational energy consumption |
Redundancy | If one chiller fails, the system can automatically bring another chiller online to take over the load, ensuring that the cooling demand is met continuously |
Applications of Chillers in HVAC
Chillers are widely used on a small and large scale. The applications are given below:
- Restaurants use chillers to keep the area cool because many customers visit and eat food inside restaurants.
- They are globally used in shopping malls. Many people visit malls, so it’s essential to keep the temperature at normal levels to ensure a comfortable environment for customers.
- Mechanical industries manufacture gadgets and other electrical products on a large scale. Hence, large quantities of heat are produced. For the machines to work correctly, it is crucial to maintain an average temperature. Chillers are used for cooling here.
- Large buildings typically use water-cooled chillers with centrifugal or turbocor compressors within a central plant cooling system. They additionally use air-cooled chillers for producing cooling in computer or communication rooms.
- Medium-sized buildings with a cooling load of 200 – 400 tons of refrigeration or 700 – 1,400 kW use water or air-cooled chillers with screw or turbocor compressors.
- Small buildings with cooling loads under 200 tons or 700 kW use scroll compressors, Turbocor compressors, and air-cooled chillers.
- Absorption chillers are used when there is an abundance of high-quality waste heat or cheap heat. We mostly find them in hospitals and buildings with heated swimming pools. Moreover, commercial office-type buildings also use these types of chillers.
- Beverage industries involve pasteurizing, cooking, and mixing. These different processes need an environment within a specific temperature range, and Chillers can maintain that temperature range very efficiently and effectively.
- Plastic industries widely use chillers because there is a lot of machinery involved in manufacturing plastic. One of the critical steps is cooling the hot plastic, which is achievable using chillers. Hence, it keeps the equipment cool, and the industries work appropriately.
- Magnetic Resonance imaging is significant in the field of medicine. MRI scanners generate a large quantity of heat, and MediChillerslers are used to keep them cool and make them last longer.
Advantages of Chillers in HVAC
There are numerous advantages of using chillers in businesses. Some of them are listed below.
- Industrial machines overheat, and it may result in the collapse of machinery. It would be costly to replace them. Hence, chillers are used to protect machines or equipment.
- Chillers circulate water; therefore, they are cost-effective.
- They are more practical and efficient than water towers.
- They are installed with special units. Chillers produce heat exhaust during operation, but these special units recover the energy and utilize it as a cycle.
- They are budget-friendly and give higher cooling levels, making them ideal for industrial processes.
- They are not exposed to rain, snow, heat, ice, etc., making them less vulnerable to malfunctioning, ultimately resulting in longevity.
- Water-cooled chillers are widely used and preferred because of their quiet operation.
- Chillers, especially water-cooled chillers, are energy efficient.
- They are available in different sizes to tackle space constraints.
- The use of water makes them safe for people who are in constant contact with the system.
Disadvantages of Chillers in HVAC
Along with the advantages, every system or machine has disadvantages, and some of them are discussed below.
- It’s a hassle to install water-cooled chillers resulting in higher labor costs.
- Air-cooled chillers produce large quantities of heat at the site.
- Maintenance such as periodic inspections, water treatments to remove impurities, and regular cleaning of the chiller’s machinery is required. With more parts, the care becomes hectic, especially in water-cooled chillers.
- A mechanical room is needed to house a water-cooled chiller.
- In case of a water shortage, water-cooled chillers can’t be used.
- Chillers operate less efficiently if the surrounding environment is humid.
We have made a Detailed HVAC Design Engineering Course for Design Professionals, Freshers which you simply can love it.
Conclusion
The article gives an insight into the working principles, types, categorization, application, merits, and demerits of Chillers in HVAC systems. Chillers are widely used on large and small scales to remove heat from liquids, and it comes in several types like water-cooled and air-cooled chillers.
Industrial chillers are categorized into different types: vapor compression, vapor absorption, screw, scroll, centrifugal, and reciprocating chillers. These cost-effective and budget-friendly machines are globally used, but they are vulnerable to malfunctioning due to corrosion, electrical issues, and negligence in maintenance. Therefore, it’s vital to ensure adequate care for proper working.
In case you are looking to upgrade your career in HVAC by qualifying Certified HVAC Designer (ASHRAE), you can take our course in Udemy. In addition, if you want to pursue our detail HVAC design course
, please contact us.