Do you have any idea about the CNC machine! It is the abbreviation of Computer Numerical Control or Computerized Numerical Control. It means the machine is controlled by an inbuilt computer. In this case, we are going to learn every sort of detail about the CNC machine and its operation, types, working principles, evolution, advantages, disadvantages, and much more stuff with CNC rapid prototyping. Therefore, without any further delay, let’s dive straight into the world of CNC machines along with its Rapid Prototyping.
What is a CNC Machine & It’s Rapid Prototyping? Definition
CNC Machine Basics
CNC machine is a symbol of modern technology. Over time technology and computers have evolved. The high-precision computer control has gained the power to perform most of the operations.
- With the advancement in technologies now the error has gone where human’s word majorly involved in the manufacturing industry.
- Nowadays much of the manufacturing is overpowered with computer programming inputs.
- One of the high precision manufacturing techniques is CNC machining.
CNC Machine Definition
Many of us may or may not possess the knowledge of CNC machines. Therefore, to make you people understand we are going to explain CNC machines in a simplified manner.
We have already seen lathe machine, shaper machine, slotter machine, milling machine, etc and all are operated manually. When these machines are controlled by computers inbuilt within the machine itself, and the operations are performed based on the software inputs, the machine will be called CNC machines. As the name suggests, it is known to produce prototypes directly from a soft copy file present on the computer.
- The computer numerically controlled device is an electromechanical device used to perform manipulation of tools from various axes.
- This device is used to generate the physical part of any computer design in a file commonly called additive manufacturing.
- Only it is an automated machine capable of machining various tools by using computers.
By using computers, we meant that it produces output from a coded, programmed set of instructions without the intervention of any manual operator operating the machining. It is one of the computerized manufacturing techniques that work based on preloaded patterns.
CNC Rapid Prototyping
CNC rapid prototyping refers to a manufacturing technique of producing functional product prototypes where a digitized version of the product to be reproduced is developed. Then, the code for the CNC machine is reconfigured to create the prototype. Since its a subtractive process, the employed CNC equipment removes the workpiece material to shape the resultant prototype.
As opposed to additive rapid prototyping, CNC prototyping can produce prototypes with similar aesthetic and functional characteristics as the final product.
History of the CNC machine
CNC machining is one of the revolutionary mentions in the field of manufacturing. Upon computers for its various operations. In the year of 1940 and 1950s for the first time when CNC machines were developed, it relied on a popular telecommunication storage technology called punch tape or perforated paper tape. This perforated paper tape technology is now out of the market as the data medium was quickly transformed from analogue to digital.
How Does a CNC Machine Work? Working Pprinciple
Typically, a set of instructions is fed into a computer by the user, and it executes the operation by directing the machine to produce the required output. Transforming things has never been easy. Additionally, when you want to change a stocked piece of material into a block of plastic, then you need a CNC machine for the process to occur.
- CNC machines work similarly to other prototype development technologies that are known to produce various prototypes such as CAD (Computer-Aided Design), FDM (Fused Deposition Modelling), and many more.
- Nowadays, computer-aided manufacturing is mainstream because of convenience and efficiency.
- Computers regulate this process of manufacturing and prototype cutting.
- Due to the present automation in computer-aided manufacturing, the working process has been easier than conventional tasks.
- Sometimes to make the exact cut the manufacturing process required for the utilization of various sizes of tools.
- In CNC machines, these tools are combined into standard units or sets from which cutting can be performed.
- The CNC works digitally provided instructions made on various software such as Mastercam for Solidworks.
- Both of these software come under the computer-aided manufacturing or computer-aided design segment, stored in the memory from the input program.
- The data is then transformed to control position and velocity signals. The movement of control access or spindle.
- In the case of unmatchable programmed data, action is required.
- According to the direction of the machine axis, the speed control unit is known to work harmoniously with the CPU.
CNC Machine Working Schematic
Look at the simple diagram to understand the working procedure,
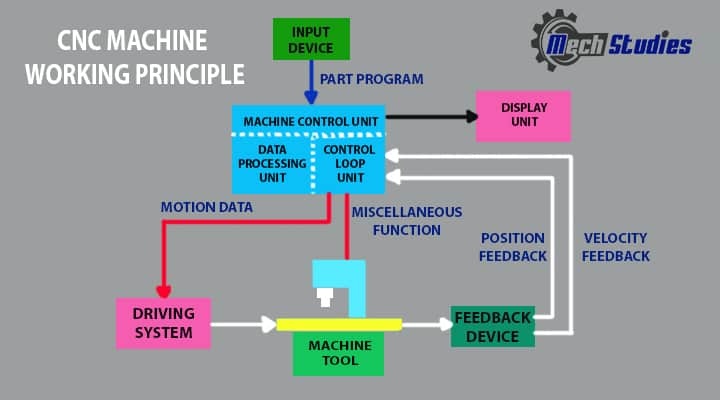
- Step-1: There are few input devices like magnetic tape reader, tape reader, etc. are used in CNC machine.
- Step-2: Write & insert the part program codes (G&M) into the Machine Control Unit.
- Step-3: Once the program inserted in Machine Control Unit (MCU), all the data is processed and the respective motion commands to be sent to the driving system.
- Step-4: The drive system has two functions, (1) to control the motion and (2) to control the velocity of the machine tool.
- Step-5: During the operation, it is required to record the position and velocity measurement of the machine tool. A Feedback system is used to do that.
- Step-6: This feedback system sends a feedback signal to the Machine Control unit. It encountered all errors and send new signals accordingly.
- Step-7: There is a display unit in the CNC machine to track all the commands, errors, programming, etc.
Primarily, CNC machines can create many things from various materials such as
- plastics,
- metals,
- aluminum,
- wood and many more.
Parts of CNC Machine
This automated machine whose motion can be controlled contains the following components, which are enlisted. Lets explore CNC machine Parts below:
Command function
This component of CNC is known to accept and interpret commands from its code.
- It contains a controller that can read all the codes, and it has a function to interpret design along with required moves.
- This part of the CNC is highly automated and ensures the proper controlling operation of the system.
Motion system
The motion system of the CNC machine ensures proper printing of the desired output. It is responsible for matching the input from the preloaded pattern guide to forming the cuts. You can check a very nice video on CNC machine,
Check a very nice video from Tomasz Skwarcan
Feedback system
Being designed by humans, we have added one more function to the CNC machine, and that is a feedback system. This segment of the CNC machine makes sure that the whole process of interpreting and producing a design is suitable to the user or not. It is a kind of review system where you can put your feedback into the system for its betterment in the next move.
In connection to a numerically controlled system to perform various functions of a machine tool with input. Here is the list of inscribed elements of the machine:
- Input devices
- Central processing unit
- Programmable logic controller
- Machine control panel
- Servo control unit
- Display unit
For the data transfer from a computer to CNC machine, a serial communication port is used, and it follows the international standards for communication. CPU is the core of a CNC machine as it controls the whole system. You can explore: YIJIN Hardware CNC machining parts manufacturer
CNC Machine is a highly precision equipment which needs a high level of service as well and each part needs to be checked throughly to get the best result as well as to avery its reduction of efficiency. However, please keep in mind the CNC machining service should be done from highly experienced personal or companies.
Tips to Choose the Best CNC for Rapid Prototyping
For many years, CNC machining has been evaluated for rapid prototyping operations. CNC prototyping holds immense value even though alternative additive prototype production technologies compete in the manufacturing industry arena. While additive prototyping processes may be appropriate for developing aesthetic prototypes, CNC machining gets a preference for developing practical ones.
Here is a comprehensive guide covering why CNC is the best fit for rapid prototyping and how we can figure out the best CNC machine for these purposes. Now, before moving on to choosing the best CNC equipment for rapid prototyping, it’s imperative to understand why even choose CNC prototyping in the first place.
Top 8 Reasons Why We Should Prefer CNC for Rapid Prototyping
Compatible with several materials
CNC prototyping is a viable option for operating with various industrial materials. Because CNC prototyping is utilized for prototypes requiring high mechanical strength, materials ranging from metals and alloys like aluminum, stainless steel, and brass to plastic polymers like PPE, HDPE, and others like wood and foam can be used.
Operational for long hours
CNC machines can operate all day long without requiring any personnel assistance. If it takes a long time to produce a prototype, the controller can specify the settings and design parameters, and the equipment will function accordingly. Thus it makes the entire manufacturing process time-efficient.
Additionally, CNC machines have a quicker turnaround. It implies that they can produce thousands of prototypes in a brief period. The equipment will operate swiftly and accurately after the design files are finalized, and the procedure is laid down.
Accurate digital to physical prototype conversion
CNC prototyping implies the development of the prototype as a digital model or simulation. The prototype only gets manufactured after the digital simulation demonstrates the prototype’s proper functionality. It makes sure the developed prototypes comply with the product specifications.
Final products demonstrate functional and aesthetic precision
We can develop look-alike-work-alike prototypes seamlessly harnessing CNC technology. It manufactures products that are strikingly identical to those made using the widely utilized bulk production processes. It signifies that a CNC prototype exhibits a high degree of aesthetic and practical comparability, enabling the product developers to contemplate what the finished product should look like, facilitating efficient prototype testing.
Additionally, we can utilize CNC machining to create a single final component or numerous parts to assemble and construct the prototype, depending on the prototype design. Consequently, CNC machining creates a durable, practical part that nearly mirrors the finished, marketable product.
High dimensional accuracy and consistency
CNC prototyping involves designing the CAD models with the requisite product dimensions. Since CNC machining is governed by a computer system and connected to a computer design file, modifying and changing your prototypes as a function of design improvement becomes streamlined. The dimension can be revised as per demand before the operator receives accurate and perfect product design outputs.
This way, we can meet the accuracy standards for the CAD model. Moreover, CNC machining enables the production of numerous prototypes with multiple, variable designs simultaneously.
Best for manufacturing complex prototype designs
CNC machining has the edge over additive prototyping technologies when it comes to manufacturing intricate, complex geometry products. Product developers and designers enjoy the flexibility to develop sophisticated prototypes as this subtractive production technique supports the customization of intricate details on the workpiece.
Cost-effective manufacturing
Since one doesn’t need to deploy specialized tools or new ones each time a prototype needs to be developed, CNC machining lowers the initial investment expenditures for developing new products. We can direct our capital, resources, and efforts towards production quality assurance and control and other crucial product development operations like prototype testing.
Requires no fixed tooling
Although other production techniques, such as plastic injection molding, require hard dies, this is not the case with CNC machining. CNC machining tools are hardened metal cutting inserts installed in spindles. These cutting inserts are also interchangeable and come in a range of shapes and sizes. As a result, they perform differently. However, if these cutting inserts are arranged properly, they can be exchanged and swapped in minutes.
How to Choose the Best CNC for Rapid Prototyping?
The ideal way of determining the ideal CNC machine for your prototype manufacturing is by analyzing your product requirements. Additionally, it’s crucial to determine the type of materials to be utilized, specify the dimensional tolerances, geometric features to be created, and the operational efficiency of the CNC equipment in response to the product prototypes to be manufactured.
Let’s explore the prominent CNC equipment options at our disposal and understand the pros and cons of utilizing them for rapid prototyping operations to help choose the ideal machinery-
CNC Laser Cutter
In addition to cutting metal, lasers can easily cut a wide range of materials, such as fabrics, polymers, and wood. They can swiftly produce engravings that are shallow but intricate. They are also generally neater, standalone equipment.
However, because lasers generate such high temperatures to cut through the workpiece, its edges may become harder and more brittle. Additionally, laser cuts will create a little dip on the edges while being highly precise, which can hamper the dimensional accuracy requirements.
Moreover, laser cutters are primarily 2-axis tools. So there could be several constraints to the features that laser cutters can produce. Also, while removing layers to increase feature depth is feasible, doing so is quite wasteful in terms of energy use and processing time, and it runs the risk of component deformation due to excessive heat. It significantly diminishes the utility of CNC laser cutters, particularly for rapid prototyping.
CNC Plasma Cutter
A CNC plasma cutter is an economical, efficient, and prompt means to cut through different conductive materials and is frequently used for steel sheet metal operations. Even though there are some multi-axis plasma cutters available, they are mostly 2-axis tools.
Rapid prototyping CNC plasma cutters have some restrictions due to their intrinsic 2-axis design, poor-to-moderate cut quality, and stringent workplace safety regulations. Nevertheless, a CNC plasma cutter can emerge as the best equipment if you want to improvise a fabrication/welding process in the prototyping settings.
CNC Router
CNC routers feature gantry frames with a substantial bridge arching over the worktable, enabling the operator to create a significantly bigger work area without compromising floor space. CNC routers are efficient in milling engineering plastics and polymers, large wood panels, and softer metals like aluminum.
Furthermore, they can mill in three axes, enabling them to produce more intricate features than the previous CNC machines discussed. It is where they can offer relevance while developing rapid product prototypes with complex features incorporating chamfers, counterbores, and pockets.
But, most machine operators neglect routers due to their limitations in stability and precision. Thus, generally, they fall short of a CNC mill’s level of accuracy.
CNC Lathe
The sole purpose of lathes is to manufacture rounded components. Lathes have revolving material and fixed equipment, unlike a CNC router. Lathes are best suited for prototypes, particularly when incredibly precise tolerances (less than 0.001″) are required, for instance, cylindrical parts like tubes, bolts, and washers. Still, a lathe is a little too limited in scope to be versatile rapid prototyping equipment except if the products are ideal lathe parts.
CNC Milling
We can encounter a CNC milling machine at almost every prototyping facility. Compared to the other equipment listed, mills are powerful and versatile and can accommodate a broader array of product components and materials. They can produce prototypes with intricate features such as deep pockets, threaded holes, and 3D extrusions.
CNC mills are well known for their dimensional accuracy and typically maintain even minute tolerances, a feature many of the machines discussed above are incapable of. But CNC mills can pose certain challenges to the operators. It requires an experienced CNC machinist to set up and operate the equipment. The work holding must be aligned with the machine’s axis, tools must be loaded and measured, and the proper program parameters must be established.
Also, expert-level CAD/CAM skills are required as it can be tricky to determine the proper cutting tool, spindle speed, feed rate, depth, and width of cut. These factors vary according to the material used, and the design features incorporated.
How to Use a CNC?
After learning so many things about CNC, you must have been thinking about how to operate or what are the skills required to handle the CNC machine in programming as well as metalworking. These CNC machines are known to make full use of CNC machines to manufacture things. There are many technically trading schools and apprenticeship courses that offer complete tutorials of CNC operation. If you want to learn how to use a CNC, then you should be capable of having the knowledge of metal cutting as well as software programming.
CNC Machining Operations
CNC machines are widely used for machining processes in various manufacturing industries from agriculture to aerospace. This machine has so many computer-controlled machining operations. Few of them are listed below,
- Facing
- Drilling
- Milling
- Boring
- Turning
- Broaching
- Threading
- Sawing
- Honing
- Grinding
- Lapping
Which Type of Software is Commonly Used in CNC?
Computer-aided design is the one software that initiates most of the CNC projects. However, there are many different kinds of CAD software packages to create various designs. The following softwares are quite popular as a software tool used for machine cutting,
- AutoCAD,
- Rhino 3D etc.
Another segment of software utilized in CNC is computer-aided manufacturing, known as CAM software. The programs created by CAM software are widely used in the CNC machines as it provides access to the user for setting up the workflow. The user can set tool parts and execute some cutting simulation before any actual cutting process. Overall utilizing computer-aided manufacturing software in CNC machines has made CNC programming easier. Examples of CAM software are,
- Mastercam,
- HSM works,
- Solidworks,
- Edgecam, and
- OneCNC.
Types of CNC Machines
CNC is one of the indispensable contributions in the manufacturing industry. , CNC is an automated tool known for receiving and interpreting the data and controlling the subsequent actions accordingly. Therefore, there are numerous types of CNC machines designed to achieve vivid manufacturing tasks. Most commonly as follows,
- 3D printer
- Routers
- Lathe
- Milling
- Plasma cutter
- Pick & place machinery
So we are going to know a few of them for better conceptual understanding.
3D printer
A 3D printer is one of the types of CNC machines known to lay down a small portion of materials.
- It uses the input program to direct where the bits of material can be cut to achieve the desired design or shape of the material.
- It is known to produce 3D parts that are layered mechanism utilization.
- Laser for solid defines the liquid or power over the multiple levels.
Routers
The CNC routers are known to perform a standard operation on three Axis coordinates. While working on three different accesses, the CNC router will cut the material into three dimensions.
- This type of routers is typically used to car large sizes for various kinds of materials such as wood, plastic, metals, and sheets.
- You should know that there are machines that are manufactured to work on 4 5 or 6 axes for intricate designs and shapes.
Lathe
The CNC machine category is quite common in the most manufacturing workplaces. It has the function of turning the workpiece and enables the movement of the cutting tool to perform the task.
- Usually, the typical lathe CNC is of two axes, but furthermore, the axis can be added according to the requirements.
- To make the desired shape let it is responsible for the rotation of a spindle and exerting pressure against grinding or carving tool inscribed in the machine.
- Usually, it is being used to manufacture spheres, cones or cylinders that are symmetrical.
Milling
Milling CNC is a type of machinery that offers higher accurate moves to carve out the exact coordinates on the workpiece.
- The manual milling machine involves the usage of handwheels and screws to carve out the workpiece effectively.
- There is an array of multiple types and sizes of a milling CNC machine to run on additional axes.
Plasma cutter
With the advent of technology in the manufacturing sector, it has been embellished using lasers as the technology. Therefore, the CNC plasma cutter is known to utilize the laser for cutting purposes. This type of CNC is specifically used to shape hard materials such as metal sheets or workpiece plates.
Pick and Place Machinery
Pick and place machines are manufactured in a way to operate similar to a CNC router. Instead of cutting various materials, this machine can pick up many components using suction power and move it to the required place. This machine is widely utilized to make computer motherboards or other assembling work.
Advantages of Using CNC Machine
The invention of CNC machines is a boon to the manufacturing sector. It has made things easy, quick and effective. Here, we are going to list some advantages of using CNC, which is the primary reason behind its success in the manufacturing industry.
- Less human error
- Consistent machining in each go
- Precise operations
- An efficient way of operation
- Quick work
- Fast production
- Less wastage
- Even less knowledge of machine can do things.
- Hassle-free operation
- May result in a prosperous business
- Production switching has gone simple.
- Reduction in indirect costs
- Enhances productivity
- Automatic control
- Boosts quality
- Improvised automation
Application of CNC Machines
From the availability of CNC machines in various areas, it is widely used in the manufacturing industry as we have already stated above. Other than that it is used to manufacture innumerable things like cabinets, furniture, musical instruments, aluminium and brass machining etc.
The presence of CNC machines is versatile and known to contribute to multiple industries. Because of its extraordinary ability to produce customized tools, it is widely used in the sectors where customization matters. Use of CNC machining to manufacture and produce various kinds of stuff in the following industries,
- medical,
- aerospace,
- oil and gas,
- transportation,
- electronics,
- marine,
- military and
- defence etc.
The rapid customization ability of CNC machining has empowered it in the manufacturing of multiple designs and shapes to objects.
Conclusion
These were some of the basic information about CNC machining. The invention of CNC machining has increased our productivity to produce things according to our requirements. There are many more aspects that need to be explored, such as its coding, more types of CNC machines, crashing and position control, and many more. We have tried to carve an outline mechanism of CNC machines in this article.
In addition, CNC machine overview, We have covered all aspects of choosing CNC equipment for rapid prototyping, and it’s evident that this subtractive production process outsmarts the additive manufacturing ones as far as building prototypes on a considerable scale is concerned. CNC tools make it relatively convenient to produce products that exhibit aesthetics, dimensional and tolerance accuracy, functionality, durability, and marketability. Also, we found out that out of all the CNC equipment employed for rapid prototyping operations, CNC milling comes out as the most comprehensive one, despite a high barrier to entry. We are hoping that you’re enjoying the learning process.