What is a piston pump? Any idea! In this article, we will learn all the details about piston pump along with definition, parts, construction, how does piston pump works, applications. Let’s explore!
What are Piston Pumps? Definition
Piston Pump Basics
Let’s start with the basics of the piston pump! We all use pumps in our daily lives. A pump is a device that converts mechanical into the hydraulic head.
- The pump has specifically 2 types- positive displacement pump and dynamic pump.
- Positive displacement pumps are those which provide a pump fix amount of fluid by changing/moving boundary at each stroke.
- Whilst dynamic pump is those where the velocity of the fluid is increased which in turn is used to increase pressure.
- The positive displacement pump is further divided into a rotary pump and a reciprocating pump.
Gear pump, vane pump is rotary pump while piston pump, diaphragm pump and plunger pump are reciprocating pumps. Reciprocating pumps provide fixed discharge at very pressure while rotary pumps provide low-pressure discharge.
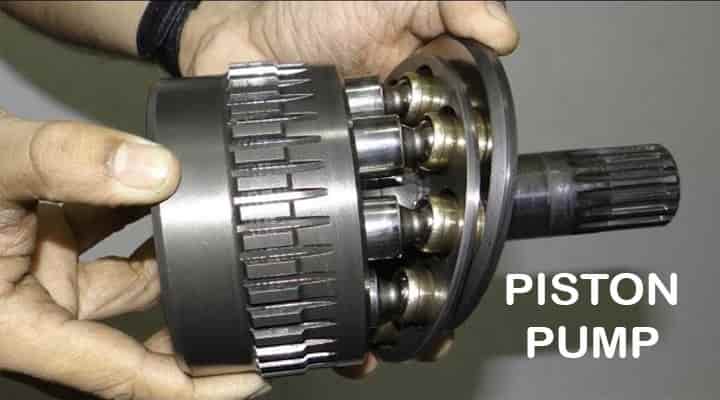
Piston pumps are highly efficient, and they have a long service life. They give a high-pressure rating of up to 500 bar. Hence, this pumps are highly preferred in hydraulic systems.
Piston Pump Definition
The piston pump is defined as a pump that uses pistons to transfer liquids or gases from one place to another.
- These are positive displacement pump,
- High pressure application, these types of pumps are widely used,
- High pressure is created due to piston’s movement,
- Piston pump
has robust construction,
- Highly efficient,
- In drilling, irrigation, etc. this types of pump are used.
Parts of Piston Pumps
This pump is a bit complex in construction it has very less clearances between its moving parts. It provides steady discharge at high pressure. Other variants are also the same as this one with minor modifications. Hence it becomes very important to study each of its parts in detail. Let’s see the parts of the straight axis piston pump which is widely used.
Housing is made of non-rust and strong material, generally steel alloy. It houses parts such as valve plate, cylinder block, piston assembly, shoe plate, swashplate, and driven shaft.
Cylinder block
It is mounted on the drive shaft, so it rotates at the same speed as that of the shaft. This part has axial bores into it. They are generally 8 to 12. The piston moves up and down into these bores. This block has tight clearance with housing. This pump gets its name due to its axis. The axis of the drive shaft is the same as that of this cylinder block and hence it is called a straight axis piston pump. On its one end, there is a valve plate connected to the inlet and outlet port and on another end, it has piston and swash plate assembly.
Piston assembly
Piston moves in the axial bores of the cylinder block. This piston is connected to the shoe plate by the shoe joint. This shoe plate is mounted on a swash plate. Pistons are generally 8 to 12 in number. They are always in even number. They move in the axial direction that is they perform reciprocating motion in the axial bores.
Rotating Barrel
A rotating barrel is used to house the piston assembly. It has slots and pistons are fitted into it. It is designed in such a way that whenever the rotating barrel rotates, pistons will also rotate. This mechanism helps to displace the fluid in the piston pump.
Intake Port
This is nothing but the part where liquid or gas input is given.
Discharge
This is the discharge side.
Port Plate
The Port plate is another important part that is used to separate the fluid from the intake port and discharge port. Whether the working fluid is a liquid or gas, it has to pass through this port plate.
Shaft
The shaft is the most vital part of piston pumps like all other types of pumps. It coupled a rotating barrel and swashplate. Now, let’s try to understand what swashplate is.
Swash plate
The shoe plate is the one to which pistons are connected by a spherical joint/ shoe joint. This shoe plate is then connected to the swash plate. This plate is mounted at a specific angle to the axis of rotation. It provides an angle to the shoe plate which affects the discharge of the pump. So, as we change this angle, the discharge of the pump also changes.
Importance of swash plate
- To achieve change in the discharge of pump.
- To change stroke length of pump by changing angle of swash plate.
This is achieved by simply changing angles. Imagine if the swash plate is perpendicular to the axis, then there will be no suction and no discharge. This is because the stroke length of the piston will be minimum, and it will occupy the space of bore in the cylinder leaving no space for entry and exit of fluid. So, the piston will remain at the same position and the whole assembly will keep rotating.
When the angle is slightly inclined in such cases pistons will now reciprocate as their stroke length will keep changing with the rotation of the cylinder block. This results in creating empty space in the bore where liquid gets sucked and gets pushed out through the delivery port. The point to be noted is space that got created in the bore is related to the amount of piston moved out of the cylinder as it is connected to swash plate. Then this space is directly related to stroke length. Stroke length is in turn related to the angle of swash plate. So as soon as swash plate will have more angle, the piston will move farther away from the bore creating more space and which in turn will give more discharge. Hence angle of the swash plate is of immense importance in this pump.
How Does Piston Pumps Work?
Basic Working Principle
We have already seen that there are few types of piston pumps, let’s see the working principle of straight axis piston pumps for understanding. Let’s learn the basic working principle of piston pumps first to understand the concept. After this section, we will elaborate on the working principle of all individual types of piston pumps.
The working principle shall be as follows,
- As a positive displacement pump, piston pump creates high pressure by piston action
- A power source is connected to the pump for creating piston action
- Nos of piston depends on the application, pressure requirements
- Controlling device is mandatory to control the flow as well as status of flow
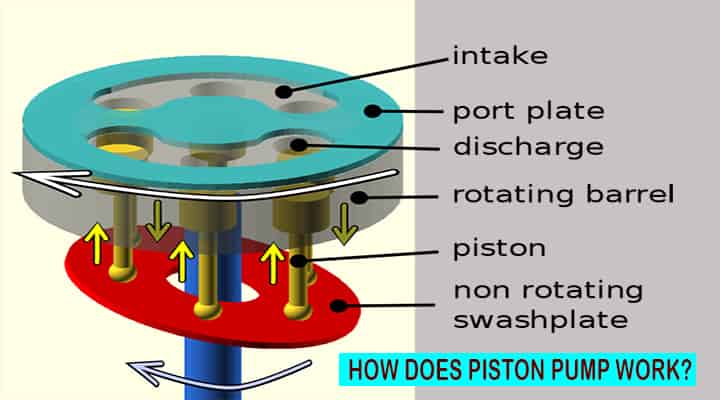


Let’s try to understand each type of piston pump along with parts and working philosophy,
Working Philosophy of Piston Pumps
Prime mover provides haft power to drive shaft. When the drive shaft starts rotating, the cylinder block mounted on it also starts rotating. As the cylinder rotates, piston assembly also rotates with them. But pistons are connected to shoe plates at some angle, this means they will start to reciprocate at their position and will perform sliding motion. The point where swash plate is closest to the cylinder block, near this point piston will occupy more space in the cylinder bore while at the point where swash plate is away from cylinder block, they will be pulled out of the bore towards swash plate as they are connected to it. The shoe plate is also rotating with the cylinder block, so this creates a situation where at a time some pistons are in bore and some out of it, this is used to create pressure difference to suck fluid in and pump fluid out.
So, when pistons are move to another end, to the farther side of swash plate, fluid gets sucked in from the suction port in this empty bore. As the cylinder block rotates causing the piston to move inwards and at this position, the piston moves into the bore to push fluid out. This process goes on simultaneously as some pistons are performing suction while some pistons are pushing out fluid and hence output obtained is a smooth and continuous discharge.
Types of Piston Pumps
Piston pumps are classified into a few types. These are as follows,
- Straight axis piston pump
- Bent axis piston pump
- Variable displacement piston pump
- Stationary cylinder Radial piston pump
- Rotating cylinder Radial piston pump
Description of All Types of Piston Pumps
Straight axis piston pump
We have already learned straight axis piston pump, let’s explore other types.
Bent axis piston pump
This pump gets its name because axis of rotation of cylinder block makes some angle with axis of rotation of drive shaft.
Construction
Inside housing, one side is port plate, valve plate and cylinder block while on another side there is flange, drive shaft. Both are these connected via universal joint.
Cylinder block
It consists of axial bores which are parallel to the cylinder axis. Cylinder block touches the valve plated. It gets its power via universal joint. Cylinder block rotates around its axis. Piston are placed in these bores.
Piston assembly
Piston in cylinder block is connected to shoe plate by shoe joint/ spherical joint. Pistons reciprocate in the cylinder bore. It performs suction and discharge due to change in position of rotating shoe plate. There are 8 to 12 pistons, and they are always evenly numbered so as to get continuous discharge.
Flange assembly
Drive shaft gets its power from prime mover. Flange is keyed to this shaft and hence it rotates as the same speed as that of the shaft. The axis of drive shaft/flange is intersecting to the axis of cylinder block at some angle. Power is transmitted to cylinder block by use of universal joint. Shoe plate to which pistons are connected by joint is also mounted on flange. It also rotates when drive shaft rotates causing reciprocating motion of piston.
Working
When the drive shaft starts to rotate, the flange will also rotate. The cylinder block will rotate because of the universal joint but at some angle. As the cylinder block is kept at some angle, piston is still connected to the shoe plate. So, there will point where distance between the plate and the piston will be closest and at point, they will be farthest. When they will be closest, piston will occupy space in the cylinder bore while when they are the farthest piston will get pulled out of this bore creating space. When the piston is moving out of the bore, fluid gets sucked in to cylinder bore. When piston is coming inside the bore piston will push fluid out.
So, for half the rotation some half part of the cylinder block will be performing suction while same half part will carry discharge function in next half rotation. This way at any point of time some piston will be performing suction while some piston will be providing discharge. This allows this pump to give continuous discharge.
Angle at which cylinder block’s axis meets central drive axis will determine the stroke length of piston which in turn will decide the discharge of pump.
Variable displacement piston pump
As the name suggests, the discharge of the pump can be varied as per need and application.
Construction
The majority of the construction is the same as that of the straight axis piston pump. Inside the casing, the cylinder block is mounted on the drive shaft. The cylinder has axial bores in which the piston reciprocates. The piston is connected to the shoe plate which in turn is connected to swash plate. The cylinder block is touching the valve plate on one end from where suction and discharge are carried out. Swash plate plays role in determining discharge, the more is the angle with the central axis with drive shaft more will be discharged while lesser the angle, the lesser will be the discharge.
Swash plate is mounted in a yoke-like mechanism. It is connected to one end by swash plate valve. This swash plate will push swash plates from one end to the backside due to which angle between shaft plate and central axis changes, which in turn changes the stroke length of the piston. Change in stroke length affects the discharge of the pump. This yoke can be moved by using any mechanism like manual control, servo control and pressure control.
Working
When the drive shaft rotates, the piston starts to reciprocate due to its connection with swash plate. When swash plate moves backward due to swash plate valve, the tilt angle increases. This causes piston to move in and out of cylinder axial bores. At some point, piston will be closest to swash plate while at some point it will be the farthest. When it is farthest fluid gets sucked in while when it is the closest fluid get pushed out of the cylinder bore.
Stationary cylinder Radial piston pump
Construction and working
As the name suggests, it has a stationary cylinder in which the piston reciprocates. There is one crank that is connected to all pistons. Consider here there are 5 cylinder and 5 pistons. All these cylinders are places at an equal angles and in the same plane so the whole pump design is balanced. As the crank is mounted on the rotating shaft it transmits same power to the piston via a connecting rod. Thus, rotating motion is getting converted into a reciprocating motion. So, at some point, some pistons will be farthest to crank while some will be closest to crank. Cylinders have suction and discharge valves. When the piston is giving inward stroke, outer fluid gets sucked in and the same liquid gets pushed out through the delivery port when the piston moves out. So, at the same time some pistons are having inward strokes while some others having outward strokes, so that way supply remains smooth and continuous.
Generally, the cylinder is in an odd configuration of 3, 5, 7.
Rotating cylinder radial piston pump
Construction and working
As the name suggests, this pump has a rotating cylinder block. This block has axial bores. These bores house pistons. This cylinder block is mounted on the shaft. Shaft gets its power from the prime mover. The whole assembly is inside the reaction ring. The reaction ring is mounted inside the casing and it is concentric to the casing. While the cylinder block is away from this center it has some eccentricity so as to achieve reciprocating motion of the piston. Piston remains in contact with the reaction ring and cylinder, this is achieved by centrifugal force and pressure of the liquid. Inlet and outlet ports are provided at the center. Inlet and outlet port are separated by pintle. It is more like a partition in the center.
When the cylinder block starts to rotate, the piston will start moving outwards due to the centrifugal force which always acts away from the center. So the rotary motion of blocks makes the piston reciprocates. As the cylinder block is eccentric to the reaction ring, it will result in a change in the piston s position in each cylinder. At the start of the rotation, the piston will move out slowly which will result in the suction of fluid from the inlet port which is at the center. As the piston will move away from more fluid rushes in, this will happen till half rotation and after half rotation reaction ring will push the piston in and this fluid will get pressurized and at end of the revolution, it will be pumped out by outlet port. This process will go in each piston-cylinder block. That way discharge obtained is smooth and continuous. This whole pump assembly looks a bit like a vane pump. But this is not a rotary pump, it is a reciprocating pump. There are 8 to 12 bores that continuously perform suction and discharge.
Why to use piston pump?
These pumps provide a very high-pressure value up to 850 bar and that too at a good discharge rate up to 45 m/s. they also have high volumetric efficiency.
Materials of Piston Pump
There are different kinds of materials used for piston pumps and it depends on project requirements as well as types of applications. Two things shall be kept in mind for material selection,
- Strength of casing and cylinder materials should meet the operating pressure and temperature requirements.
- Robust construction
- Scratch resistance
- Resistance to chemical attack
- Rust and corrosion free
Few types of materials have been listed for basic understanding,
- Stainless steel
- Brass
- Nickel alloy
- Cast iron
- Plastic
- Ceramics
- Aluminium,
- Bronze,
Advantages of Piston Pump
The advantages of piston pumps shall be as follows,
- Suitable for high viscous fluids.
- Speed is low.
- High efficiency.
- Wide range of pressure.
- Pump discharge is not effected by head.
- Widely used as metering pumps.
- Normally it’s very difficult to manage the force, when there is no flow. However, for this type of pump, force can be easily managed without any flow.
- Pump performance is having negligible effect by pressure of the liquid or gas.
- It can handle abrasives, slurries, etc. without any problem in performance.
Disadvantages of Piston Pump
The disadvantages of the piston pump shall be as follows,
- This pump is heavy.
- Very bulky due to piston assembly.
- Used mainly for low fluid flow rates.
- Flow is pulsating type, separate pulsating dampener is required.
- High maintenance cost
- High operating cost
Applications of Piston Pumps
The applications of the piston pump shall be as follows,
- Irrigation system
- Paint sprays
- Fertilizer industries
- Waste water treatment
- Drilling
- Oil production industries
Manufacturers of Piston Pumps
The manufacturers of the piston pump shall be as follows,
- Moog
- Oilgear
- Parker
- Racine
Conclusion
Hence, we have got a basic idea about piston pumps, it’s types, working philosophy, etc. Any doubt, please let us know. Refer to our most viewed articles,
Like this page
Its good as your other articles : D, appreciate it for putting up.